Innovative Welding Techniques Beyond Conventional Tools
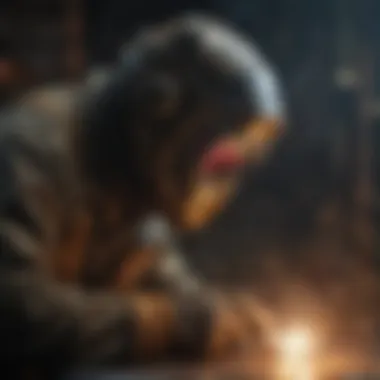
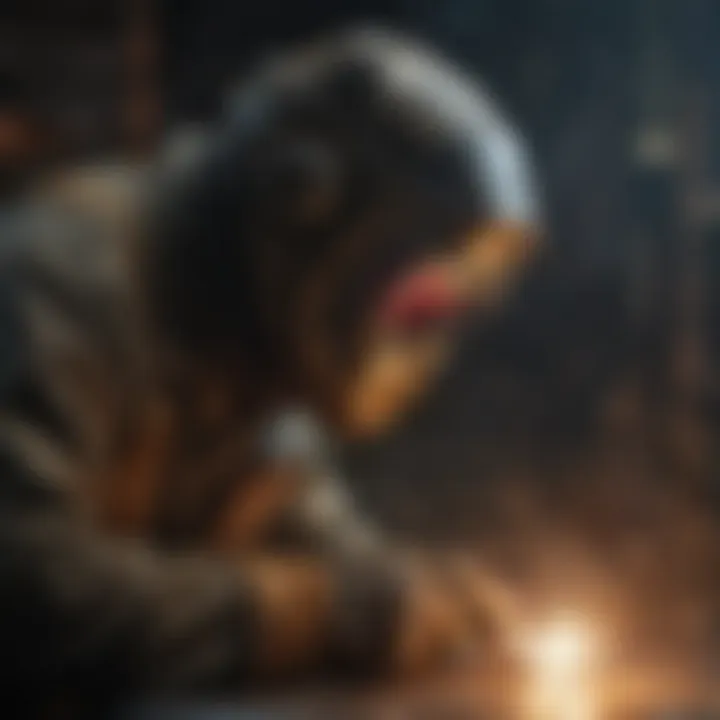
Intro
Welding has traditionally relied on specific equipment such as arc welders or gas torches. However, there exists a variety of alternative methods for joining materials that do not require these conventional tools. This exploration enables individuals, particularly in agriculture, to be more resourceful and effective in their projects. By understanding these non-traditional techniques, farmers and DIY enthusiasts can address various challenges in field applications and repairs without heavy machinery.
Definition of Key Terms
To clarify the discussion, it is essential to define some key terms:
- Welding: The process of joining materials, typically metals or thermoplastics, by melting the workpieces and adding a filler material.
- Non-conventional welding: Methods of welding that do not depend on traditional equipment. This includes techniques like soldering, brazing, or using specific heat sources that are more accessible.
- Filler material: A substance added to the weld pool to reinforce the joint. This can range from metal rods to other substances depending on the method used.
Understanding these terms provides a foundation for diving into alternate welding techniques.
Relevance in Agriculture, Horticulture, and Agronomy
Non-conventional welding methods present significant advantages across agricultural practices. In horticulture, flexibility is essential, as tools need to adapt to various materials and conditions. For example, gardeners may need to repair metal trellises or build customized tools. In agronomy, the ability to create or mend equipment without access to heavy machinery can enhance productivity. Often, repairs need to happen quickly and with minimal costs. Using alternative welding methods allows farmers to maintain their tools efficiently while reducing their reliance on outside services.
The relevance extends beyond immediate repairs. Innovative welding techniques promote creativity in design and function, helping to optimize solutions tailored specifically for agricultural challenges. Engaging with these methods not only improves functionality but also fosters a do-it-yourself culture that can empower communities.
Prelude
The exploration of welding techniques beyond the conventional realm holds significant relevance in various fields. Many traditional approaches to welding rely on heavy machinery and specialized equipment. However, the limitations of such equipment can hinder progress in situations demanding flexibility, adaptability, and cost-effectiveness. Given the evolving landscape of agriculture and DIY projects, understanding alternative welding methods becomes not just beneficial but essential for enhancing productivity and innovation.
Understanding these non-conventional approaches equips farmers, agronomists, and DIY enthusiasts with a toolkit to address specific challenges they encounter regularly in their work. With the absence of standard equipment, practitioners can still forge connections between different materials effectively. These methods are often characterized by simplicity, making them accessible to a broader audience.
In addition, the absence of large, bulky equipment influences space management and mobility within work environments. Alternative welding methods also often reduce costs associated with purchasing, maintenance, and operation of conventional machines. As a result, it can significantly impact financial planning and project scalability.
Overall, this article dives into the details of various welding techniques that do not require conventional equipment. From the basics of each method to specific applications, it serves as a comprehensive guide. Readers will gain insights into effective techniques, materials compatibility, and practical applications, thereby expanding their capabilities in agriculture and adjacent sectors.
Understanding Welding Beyond Conventional Techniques
Welding, at its core, involves joining materials, often metals, to create strong bonds. Conventionally, this process utilizes methods like arc welding, MIG or TIG welding, and others that require specific apparatuses. However, reevaluating how we approach this task opens the door to many other possibilities.
Non-conventional techniques like brazing, soldering, and adhesive bonding provide versatile alternatives for joining materials. Each method has its own merits and applications, making them suitable for a range of scenarios where conventional welding may pose challenges.
Brazing, for example, allows for joining metals at lower temperatures compared to conventional welding, which minimizes the risk of warping. Soldering is widely used in electrical applications, effectively connecting components without high heat that can impact delicate circuits. Similarly, adhesives offer a unique route for bonding that eliminates the need for heat altogether.
Beyond these methods, the practicality of using mechanical fasteners deserves consideration. This approach might seem simplistic, but it is effective in many applications without the need for heat at all. By focusing on these alternatives, we not only expand our capabilities in joining materials but also foster a culture of innovation in agricultural practices and beyond.
The Necessity of Alternative Welding Methods
As industries evolve, the need for flexibility in methodologies becomes essential. Alternative welding methods offer practical solutions in scenarios where traditional welding might be impractical or too costly. It is necessary to understand the reasons behind the shift toward these techniques. With advancements in technology and a growing emphasis on sustainability, exploring welding solutions that do not rely on conventional equipment has become increasingly relevant.
Challenges with Traditional Welding Equipment
Conventional welding equipment often involves significant financial investment. Many small-scale operators or DIY enthusiasts find it very difficult to afford the necessary machines, such as MIG or TIG welders. This financial barrier limits opportunities for innovation and repair.
Moreover, traditional welding requires a high level of skill and training. This challenge can exclude many potential users who are eager to engage in metal working or repairs but lack the resources or training to manage standard equipment. Additionally, many traditional techniques involve intensive energy consumption, raising concerns regarding efficiency and environmental impact. In agricultural settings, where energy resource limitations are common, this can be an additional hurdle.
The operational hazards associated with traditional welding must also be acknowledged. Welders are exposed to risks, including burns, fumes, and fire hazards. When working in environments like farms, where flammable materials may be present, these dangers become even more pronounced. Thus, caution must be taken, leading to a consideration of safer, more manageable alternatives.
When Conventional Methods Are Not Feasible
There are situations in which traditional welding methods simply cannot be applied. Firstly, some materials are unsuitable for welding due to their physical properties. For example, certain plastics and composites cannot withstand the high temperatures generated by traditional welding techniques. Alternative methods such as soldering or adhesive bonding become crucial in these circumstances.
Furthermore, certain project locations may present challenges. Remote sites, such as rural agricultural operations or construction areas, may lack the necessary power supply for conventional welders. In such cases, more portable and accessible tools are preferred.
Weather conditions also play a significant role. Rain or wind can create unsafe conditions for traditional welding. Alternative techniques can often be used under diverse conditions, offering resilience against nature's unpredictability. For instance, brazing can be done with simple hand tools that are not affected as much by external conditions.
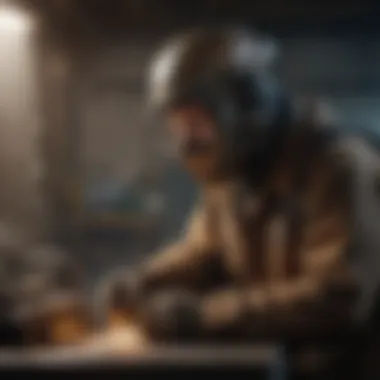
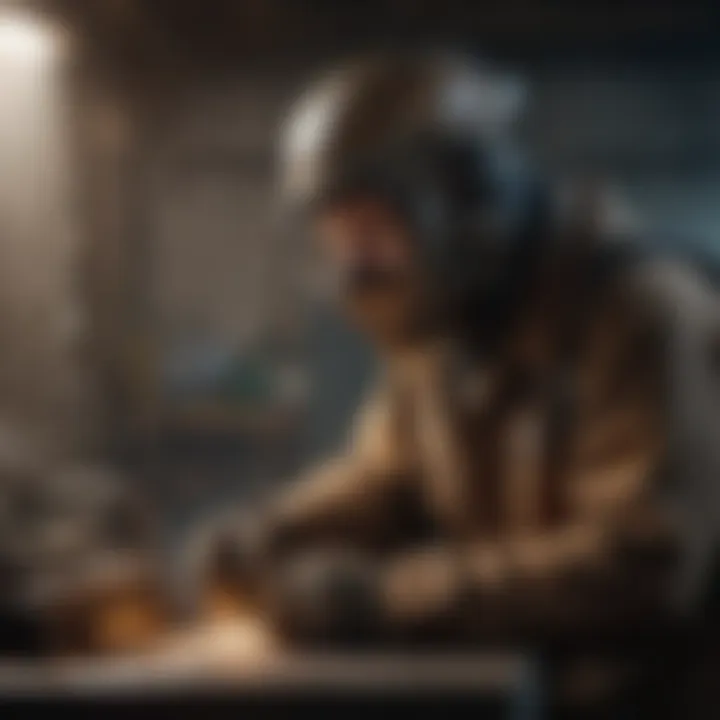
Adopting non-conventional welding methods addresses both practicality and safety concerns while enabling diverse applications across sectors. Therefore, acknowledging and addressing these challenges leads to the necessity of alternative methods, ultimately expanding the toolbox for farmers, builders, and craftspeople.
Common Methods of Welding Without a Welder
In various sectors, including agriculture and construction, conventional welding equipment may not always be available. Consequently, alternative methods of joining materials become crucial. This section outlines common approaches that can be implemented without a welder. These methods often offer unique advantages, such as lower costs, flexibility in applications, and accessibility for DIY enthusiasts.
Before diving into specific techniques, one should consider the materials involved, the environmental conditions, and the desired strength of the joint. Different materials have varied compatibility with non-welding methods. Understanding these details can optimize the process and end results.
Brazing: A Versatile Alternative
Brazing is a bonding technique that involves melting a filler metal above 450°C (about 840°F) to join two base metals. This method is useful due to its versatility and ability to create strong joints without melting the workpieces.
Advantages of brazing include:
- Ability to join dissimilar metals
- Maintained structural integrity of the base materials
- Minimal thermal distortion
- Faster process compared to traditional welding
Common applications of brazing include plumbing and HVAC work. It is essential to properly clean the joint surfaces and choose the right filler metal for effective bonding.
Soldering Techniques for Practical Applications
Soldering is another technique that uses a filler metal, but it typically operates at lower temperatures than brazing. This method is frequently employed in electronics and plumbing, making it particularly relevant for small-scale agricultural equipment repairs.
Key points to remember:
- Flux is important: It prevents oxidation at the joint, allowing for better adhesion.
- Temperature control is essential: This ensures the base metals do not overheat and lose their properties.
Soldering is especially suitable for delicate parts, like circuit boards or thin copper pipes. A soldering iron or a torch can be used depending on the application.
Using Adhesives for Structural Bonding
Adhesives have gained popularity for their ability to join various materials, both metal and non-metal, effectively. The choice of adhesive is critical. Some commonly used adhesives include epoxy, polyurethane, and cyanoacrylate.
Benefits of using adhesives:
- They can bond different materials.
- Usually easy to apply.
- Often cures quickly, leading to less downtime.
- Reduce the need for heavy equipment, making them suitable for field repairs.
However, adhesive bonding can be sensitive to environmental factors like temperature and humidity. Proper surface preparation, such as cleaning and roughening, increases the adhesive's effectiveness.
Mechanical Fasteners: When Welding Isn't Necessary
Mechanical fasteners offer a straightforward solution when welding is problematic or unnecessary. Techniques such as bolting, riveting, and screwing provide reliable joints without the need for heat.
Some advantages include:
- Immediate strength upon installation
- Easier disassembly for maintenance or repair
- Minimal skill required for installation
Mechanical fasteners can be useful in various applications, from securing metal sheets in a shed to constructing large agricultural equipment. The choice of fastener will depend on the materials and the required load-bearing capacity.
In summary, understanding and utilizing these alternative welding methods enhance the capabilities of farmers and enthusiasts alike. They offer flexible, practical solutions, especially in settings where conventional welding equipment is not feasible. The next section explore the materials suitable for these non-welding techniques, ensuring successful applications.
Materials Suitable for Non-Welding Techniques
Understanding the materials that can be used with non-welding techniques is crucial for their successful implementation. The choice of material directly impacts the effectiveness, strength, and longevity of the joints formed through alternative methods. Certain materials may work better with techniques like brazing, soldering, and adhesive bonding. Thus, recognizing their compatibility and properties is paramount for achieving optimal results.
Metals: Considerations and Compatibility
When dealing with metals in non-welding applications, several factors need consideration. First, the melting points and thermal properties of the metals are essential. For instance, metals with lower melting points, such as aluminum and brass, are often more suitable for soldering or brazing techniques.
Compatibility between different metals is another aspect. Not all metals bond well; for example, aluminum and steel require specific preparations and filler materials to ensure a strong bond. Additionally, one must consider the environmental factors influencing the metals, such as corrosion resistance and exposure to chemicals.
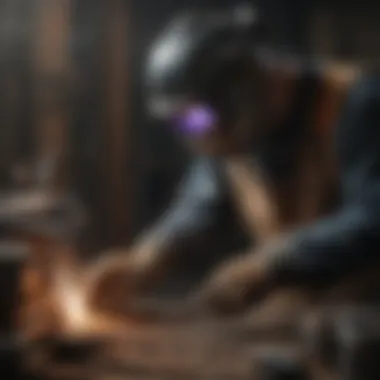
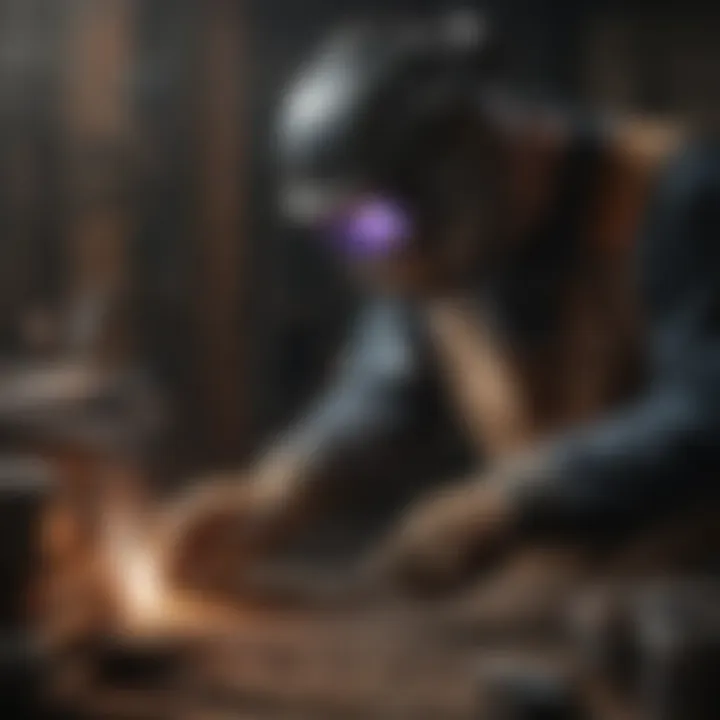
- Aluminum and its alloys: Ideal for both brazing and soldering due to their lightweight and corrosion resistance.
- Copper: Works well with solder but has different requirements when brazing.
- Steel: While thicker steel components may not be ideal for these methods, thinner sections can be effectively joined using innovative techniques.
Furthermore, surface preparation is essential. Metals need to be clean and free from oxides, oils, or any contaminants before proceeding with bonding methods. Proper preparation can drastically improve the adhesion strength of the materials.
"The properties of the material dictate the choices of bonding methods and their success even more than the equipment used."
Plastics and Composites in Non-Traditional Applications
Plastics and composites offer additional possibilities in non-welding techniques. They are versatile and can serve various purposes in agriculture and DIY projects. The diversity in plastics—such as polyethylene, polypropylene, and PVC—can significantly influence the choice of bonding methods.
When working with plastics, it is essential to consider the following:
- Type of plastic: Different plastics require different adhesives or techniques. For example, epoxy adhesives are often chosen for their strength with thermosetting plastics, while cyanoacrylate is suitable for quick fixes.
- Surface energy: High-energy surfaces promote better adhesion. Roughening the surface can enhance the bonding between plastics and adhesives.
- Chemical resistance: Some plastics can be sensitive to chemicals involved in bonding processes. Understanding these properties can prevent future failures in the bond.
Composites, which combine materials such as reinforced plastics, also require careful consideration. Their layered structure could necessitate specialized adhesives or bonding techniques. In contemporary practices, knowledge about their behavior under stress and environmental factors remains vital, as these can directly affect the performance and durability of structures built without welding.
In summary, the type of materials and their respective compatibility and properties dictate the success of non-welding techniques. Both metals and plastics play crucial roles in achieving strong and effective bonds without traditional welding equipment.
Safety Considerations When Welding Without a Welder
Safety is paramount when exploring alternative welding techniques. While non-conventional methods may not involve high heat and complicated machinery, risks still exist. Understanding these safety considerations will help to mitigate potential hazards. Many individuals may not perceive these methods as dangerous, but knowledge and preparation are essential in promoting a safe work environment.
A focus on safety not only protects operators but also enhances the efficiency of the task. Improper practices can lead to accidents, injuries, or damage to materials. Therefore, a diligent approach to safety remains vital, no matter the method employed. This section outlines key elements in ensuring a safe environment when using alternative welding techniques.
Personal Protective Equipment: Essential Gear
Choosing the correct personal protective equipment (PPE) is critical. Regardless of the method, the operator must be prepared. Here are some essential items:
- Safety Glasses: Protect eyes from flying debris and harmful particles. This is crucial when using adhesives or soldering materials.
- Gloves: Consider heat-resistant gloves, even if the heat is not as high as traditional welding. They can safeguard against sharp edges and chemical exposure when using adhesives.
- Respiratory Protection: Inhaling fumes from some non-welding bonding agents can be harmful. A simple mask or respirator is advisable, especially in poorly ventilated areas.
- Apron or Work Suit: A durable work suit can protect skin and clothing from splashes or any other hazardous substances.
It is also important to regularly inspect equipment and gear to ensure it is in good condition. Deteriorated PPE may not provide the required protection, leading to greater risks.
Safe Practices in Alternative Welding Environments
Creating a safe working environment is essential in reducing hazards. Here are some practices to consider when working without traditional welding setups:
- Work in a Well-Ventilated Area: This allows proper air circulation, crucial when using chemical adhesives or materials that may emit fumes.
- Minimize Clutter: Keeping the work area organized reduces the risk of accidents. Loose materials can become tripping hazards or get in the way.
- Keep Flammables Away: When using adhesives or any flammable substance, ensure that flammable items are stored far from the work area.
- Know Emergency Procedures: Have a plan in place for accidents or emergencies. Knowing how to react can mitigate injuries or damages.
"A proactive approach to safety can prevent accidents before they occur."
Implementing these practices ensures a better environment when employing welding alternatives. The aim should be not just to complete tasks but to do so in a manner that safeguards health and well-being.
Applications of Non-Welding Techniques in Agriculture
In agriculture, the adaptability of welding techniques plays a crucial role in maintaining equipment and developing structures. Non-welding methods offer an array of benefits, particularly where access to conventional welding tools is limited or impractical. These approaches not only promote efficiency but also enhance sustainability in agricultural practices.
Benefits of Non-Welding Techniques:
- Accessibility: Many farmers operate in remote areas where traditional welding equipment is not available.
- Cost-Effectiveness: Non-welding methods can be less expensive since they don't require investment in specialized machinery.
- Versatility: These approaches can be used for a variety of materials, including metal, plastic, and composites.
Using alternative techniques allows farmers to address urgent repair needs promptly, minimizing downtime during critical agricultural seasons.
Repairing Farm Equipment Without a Welder
Repairing farm equipment can be a challenging task, especially when traditional welding tools are out of reach. However, several alternative methods can help restore functionality without needing a welder.
- Brazing: This method involves melting a filler metal that has a lower melting point than that of the base metal. Brazing can effectively join metals and is suitable for thicker materials. This technique can be particularly useful for repairing damaged components on tractors or plows.
- Mechanical Fasteners: Bolts, screws, and rivets provide a solid connection and can be used extensively in machinery. Using mechanical fasteners allows for easy disassembly of equipment for future repairs. Farmers can quickly attach parts without needing any special equipment.
- Adhesives: Industrial adhesives can create strong bonds between metal parts. There are specific types designed for high-stress or outdoor conditions. When applied properly, these adhesives can withstand significant forces, making them ideal for quick repairs.
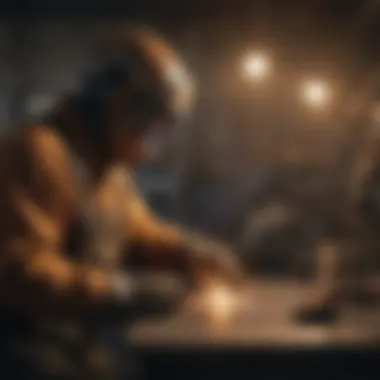
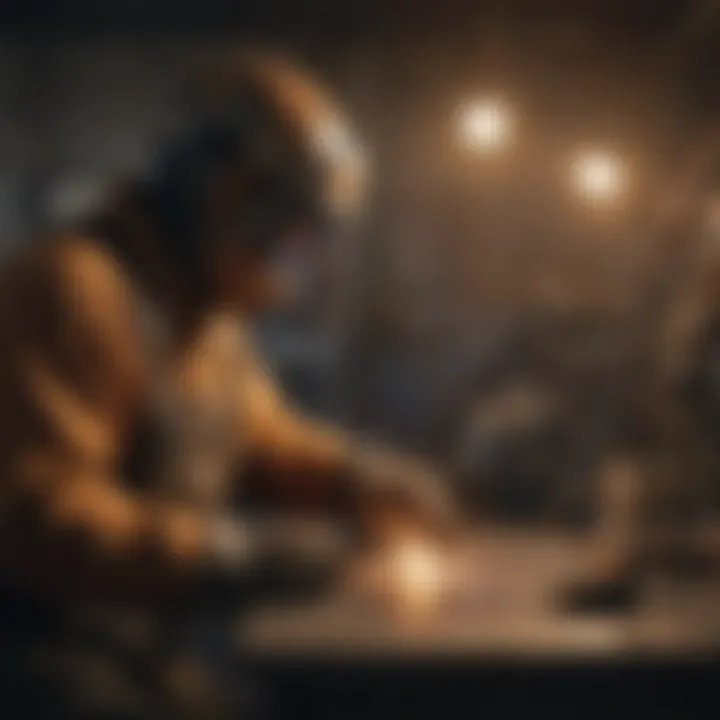
These methods not only facilitate equipment repairs but do so with less complexity and require minimal training, making them accessible to most farmers.
Creating Sustainable Structures in Horticulture
In horticulture, the creation of sustainable structures can benefit significantly from non-welding techniques. The focus on eco-friendly practices aligns with the growing interest in sustainability among many farmers and gardeners.
- Using PVC Pipe: PVC pipes are versatile materials for building structures such as row covers or irrigation systems. They can be easily connected using adhesive or mechanical fittings, which reduces the need for welding.
- Wood and Metal Combinations: Wooden frames can be combined with metal brackets and screws for strength. This method is not only sustainable but also provides flexibility in design while maintaining structural integrity.
- Green Building Materials: Using recycled materials minimizes waste and supports environmental goals. Non-welding assembly methods allow for the incorporation of various materials, making use of what is readily available.
"Sustainable approaches to horticulture not only embrace environmental responsibility but also ensure that farming practices remain viable for future generations."
Economic Considerations of Alternative Welding Techniques
The topic of economic considerations in alternative welding techniques holds significant relevance in today’s rapidly evolving industrial landscape. As traditional welding methods often involve expensive equipment and skilled labor, exploring non-conventional approaches can lead to substantial cost reductions. Farmers and DIY enthusiasts are particularly interested in these solutions, given their need for effective and budget-friendly methods. By assessing the economic impacts, individuals can make informed decisions that align with their financial capacity and project requirements.
Understanding the cost-effectiveness of non-conventional welding methods is critical. Many agricultural applications require frequent repairs and constructions that may not justify the use of costly welding machinery. In this context, alternative methods can provide timely solutions that do not compromise the quality and integrity of the work performed.
Cost-Effectiveness of Non-Conventional Approaches
Cost-effectiveness is a key factor when assessing alternative welding methods. Techniques such as brazing and soldering allow for low initial investment while ensuring robust results. These methods utilize readily available tools and materials, making them accessible to a broader audience. For instance, in rural settings where professional welding services may be scarce, reliance on accessible techniques enables timely repairs and maintenance of essential agricultural equipment.
Benefits of Non-Conventional Approaches:
- Reduced Initial Costs: The tools needed for braze or solder are often affordable and simple to use.
- Less Skill Required: Unlike traditional welding, which often requires years of training, many alternative methods can be learned quickly.
- Flexibility in Applications: These methods can be employed in various contexts, from metal repairs to joining dissimilar materials, providing versatility.
"Exploring these cost-effective alternatives can lead to significant savings while maintaining high standards in agricultural practices."
Investment vs. Return: Analyzing Alternative Methods
Evaluating the investment versus return in alternative welding techniques is essential for farmers and industry professionals. The upfront costs of equipment and material for non-conventional welding should be weighed against the expected benefits.
Key Considerations in Investment Analysis:
- Durability of the Bond: The longevity of the bonded materials can reduce future repairs, translating to long-term savings.
- Time Efficiency: Non-traditional methods often yield faster results, enabling quicker project completions.
- Material Savings: Commonly available and lower-cost materials can be utilized without compromising quality.
Future Trends in Non-Welding Technologies
The exploration of welding techniques without conventional equipment is gaining traction. Understanding the future trends in non-welding technologies is vital for farmers and enthusiasts who may rely on alternative methods in various applications. This section will discuss the importance of these trends, focusing on innovations and research directions that are shaping the landscape of non-traditional welding methodologies.
Innovations in Alternative Bonding Materials
In recent years, there has been a marked advancement in bonding materials that do not require heat or the traditional welding process. One significant trend is the development of high-performance adhesives. These adhesives often exhibit strong bonding capabilities across various substrates, including metals, plastics, and composites. They can be used in numerous agricultural applications, from equipment repairs to structural connections in greenhouses.
Many of these innovative materials have properties that enhance durability, flexibility, and resistance to environmental factors. They can cure quickly at room temperature, making them suitable for on-site repairs. The construction of various agricultural structures can also be simplified through these bonding agents, reducing the need for a full welding setup.
"The potential of alternative bonding materials can lead to reduced manufacturing costs and improved efficiency in construction processes."
Research Directions in Non-Traditional Welding Methods
The academic and industrial communities are increasingly focused on research that aims to unveil new methods of joining materials without conventional welding techniques. This includes looking into topics such as cold joining techniques and the use of ultrasonic vibrations to achieve strong bonds. These methods often entail less energy consumption, making them more environmentally friendly.
Additionally, studies into hybrid techniques that combine several alternative methods are emerging. For example, combining adhesive bonding with mechanical fastening could address some of the limitations of each method when used individually. The benefits of such research are plentiful. They promise enhancements in joint strength, efficiency, and overall adaptability in applications where traditional welding may not be possible.
Overall, the ongoing investigation into non-traditional welding methods underscores a shift in how the agricultural sector can approach material joining. As these methods become defined and standardized through research, practitioners in agriculture will have access to sophisticated techniques that enhance their operations.
This continuous evolution in non-welding technologies is pivotal for staying competitive and accommodating the diverse needs of modern agricultural practices.
End
Summarizing Key Insights on Alternative Welding Methods
The insights shared throughout this article demonstrate that welding does not always require traditional equipment to achieve reliable results. Here are key takeaways to consider:
- Versatility: Techniques like brazing, soldering, and adhesive bonding offer flexibility in materials and processes. Each method has specific advantages depending on the project requirements.
- Cost-Effectiveness: Non-conventional welding methods often reduce the initial investment in equipment. This aspect can be particularly beneficial for farmers and DIY enthusiasts operating within budget constraints.
- Material Compatibility: Knowledge of material interactions is crucial. Understanding which metals, plastics, and composites work best with each method can enhance bonding strength and durability.
- Safety Practices: Ensuring safety remains paramount even when using alternative techniques. Proper personal protective equipment and safety protocols reduce the risk of accidents and injuries.
Through these insights, it is clear that utilizing non-traditional welding methods is not only a practical choice but can also lead to sustainable practices in various fields. The focus on alternative solutions encourages creativity and innovation, paving the way for effective applications in agriculture and beyond. This discussion encourages readers to consider how they can implement these techniques in their own projects, thus rethinking the way they approach welding and bonding.