Essential Guide to Packing Your Mini Excavator Properly

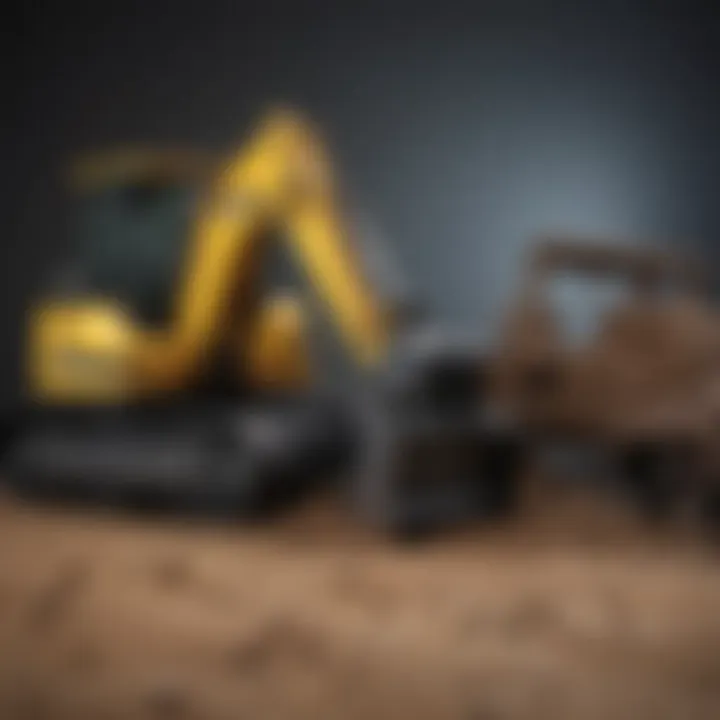
Intro
Packing a mini excavator for transport is a task that requires careful planning and organization. The process impacts not only the efficiency of the machine’s operation on site but also the safety of the personnel involved. Understanding the essential components and techniques involved in packing will greatly enhance effectiveness and minimize potential risks. This guide lays out a comprehensive approach to ensure your mini excavator is packed correctly, making it ready for any task, whether in agriculture, horticulture, or general earthmoving.
Topic Overview
Definition of Key Terms
Before delving into the intricacies of packing a mini excavator, it is essential to define some key terms. A mini excavator refers to a smaller type of excavator, designed for use in tight spaces where larger machinery cannot operate efficiently. Definitions also include terms like attachments—the various tools that can be added to an excavator for specific tasks, such as buckets, augers, or hydraulic hammers.
Relevance in Agriculture, Horticulture, and Agronomy
Mini excavators play a significant role in agriculture and horticulture. They are highly versatile and used for tasks such as digging, grading, and earthmoving. In agronomy, their compact size allows them to operate in smaller fields and gardens that larger machines cannot access. These factors highlight the relevance of understanding how to pack them adequately to optimize their efficiency when deployed.
Current Trends and Innovations
Recent Advancements in the Field
In recent years, mini excavators have seen many advancements. Newer models incorporate improved fuel efficiency and emission control technologies, aligning with global sustainability goals. They are now equipped with smart technologies, allowing operators to monitor performance and diagnostics through integrated software.
Emerging Technologies and Practices
Innovative practices regarding mini excavator usage are emerging. Operators are increasingly adopting telematics, which enables real-time data tracking on machinery performance. This allows for proactive maintenance and better planning during operation, ensuring the machine is always functioning at optimal levels.
Practical Applications
Step-by-Step Guides or How-Tos
To ensure proper packing of mini excavators, follow these steps:
- Clean the Excavator: Ensure that all components of the excavator are free from dirt and debris, which can cause damage during transit.
- Secure Attachments: Remove and securely fasten any attachments separately. Ensure they are safely stored in a way that they will not cause harm to other equipment during transport.
- Check Fluid Levels: Verify that all fluids, including oil and coolant, are at proper levels to prevent leaks during transport.
- Positioning: If using a trailer, position the excavator to maintain balance. The heavy end (typically the rear) should be toward the front of the trailer.
- Secure the Machine: Use straps or chains to fasten the excavator firmly in place, taking care not to damage the machinery.
Tips and Best Practices for Implementation
- Use Quality Straps: Always opt for high-quality, heavy-duty straps to secure the equipment.
- Regular Maintenance: Schedule regular maintenance checks on both the excavator and the transport equipment to ensure everything remains in operational condition.
- Safety Gear: Don’t forget to equip all personnel with appropriate safety gear when loading and unloading equipment.
"Proper packing of equipment is not just about transit; it’s about ensuring the effectiveness and safety of on-site operations."
Being thorough and meticulous in the packing process of a mini excavator can significantly boost not just operational efficiency but also the safety of all involved.
Understanding Mini Excavators
Understanding mini excavators is critical when packing and using this equipment effectively. Knowing their features, specifications, and variants helps you make informed decisions. This understanding leads to better preparation and ultimately improves efficiency on the job site. Mini excavators come in different sizes and capabilities, each serving specific purposes. Proper knowledge allows users to select the right type for their operation and understand how to secure the machine properly for transport.
Definition and Use Cases
Mini excavators are compact construction machines designed for a variety of tasks, including digging, lifting, and hauling. Their size makes them suitable for small construction sites, landscape projects, and even residential work. Common use cases involve trenching for foundation work, landscaping, and utility installation. Their versatility and ability to operate in tight spaces are what makes mini excavators popular among contractors and DIY enthusiasts alike.
Types of Mini Excavators
Conventional
Conventional mini excavators have a rear swing that allows for improved digging capability and reach. The key characteristic of this type is its balance of power and size. These machines are generally easier to operate and can handle larger workloads. A conventional mini excavator is beneficial for project sites where space is not a limiting factor. However, their bigger size can be a disadvantage in tight areas, limiting accessibility.
Zero Tail Swing
Zero tail swing mini excavators have a design that does not extend beyond the track width during operation. This feature is ideal for working in confined spaces, making it a preferred choice for urban projects. The advantage of zero tail swing models is their maneuverability, allowing them to navigate around obstacles easily. The trade-off, however, is often a slight reduction in digging power and reach compared to conventional types.
Compact
Compact mini excavators are designed for agility and ease of transport. Their lightweight and smaller profile make them suitable for smaller sites or residential applications. A compact excavator has a unique feature: the ease with which it can be transported on trailers without requiring special licensing. This makes it a practical choice for contractors who must move their equipment frequently. However, the size also means that they may not be as powerful as their larger counterparts, limiting their use in more intensive digging operations.
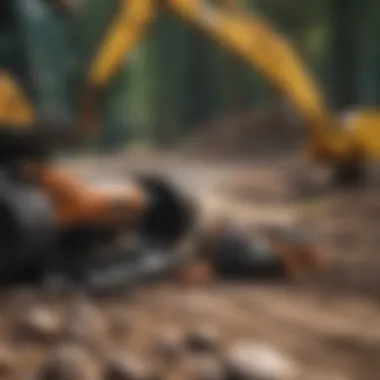
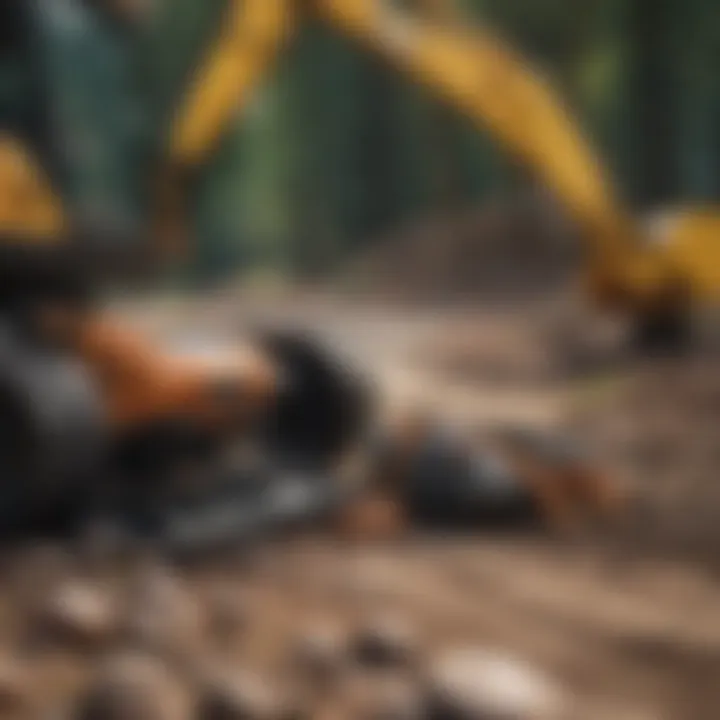
Key Specifications
Operating Weight
The operating weight of a mini excavator refers to its total weight when fully equipped for operation, including the operator. This specification is crucial as it affects both the stability and lift capacity of the machine. A heavier mini excavator generally offers greater stability but may require more robust transport solutions. Conversely, lighter models are easier to transport but may suffer in terms of stability under heavy loads.
Digging Depth
Digging depth is a critical specification as it defines how deeply the machine can excavate. Standard mini excavators typically have a digging depth ranging from 5 to 12 feet. This aspect is important when assessing which excavator suits specific job requirements. A deeper digging capability allows for more flexibility in various projects, such as foundation work or trenching.
Reach
Reach refers to the horizontal distance the excavator can extend its arm, essentially influencing how far it can work from its base without repositioning. Increased reach is important for tasks that require extending over obstacles or when working in tight environments. However, higher reach usually coincides with higher operating weight and may introduce challenges in transport and stability.
Understanding these specifications helps in selecting the most appropriate mini excavator for your needs.
Essential Components of a Hoe Pack
In the realm of mini excavators, understanding the essential components of a hoe pack is crucial. Properly equipping your mini excavator not only enhances productivity but also improves safety and efficiency on-site. The respective components significantly contribute to the overall functionality of the machine, making it imperative to consider their characteristics and applications when planning the packing process.
Bucket Types
Standard Bucket
The standard bucket is often highlighted as the go-to choice for general earthmoving tasks. Its primary characteristic is a wide, flat shape, allowing for effective digging, moving, and dumping of material. Due to its versatility, it is widely used in various applications, including landscaping, site preparation, and roadwork. The unique feature of the standard bucket is its ability to provide a balanced approach to handling different soil types and conditions. However, it may lack the precision needed for specialized tasks, making it less ideal for detailed excavation work.
Digging Bucket
The digging bucket is characterized by its deeper and narrower design, tailored for increased digging power. This bucket is ideal for projects requiring more precise excavation or when working in tight spaces. Its beneficial aspect is that it cuts through tougher soil much more efficiently than a standard bucket. Additionally, the digging bucket often comes with reinforced edges for durability. A disadvantage might be its limitation in moving bulk material, as it is not designed for efficient transporting.
Trenching Bucket
Trenching buckets excel in creating deep trenches for utilities or drainage. Their narrow design allows for digging precise channels without disturbing the surrounding area much. The key characteristic of a trenching bucket is its longer and narrower shape, which is advantageous for specific trenching tasks. It is popular because it increases operational efficiency in particular applications, such as laying pipes or cables. However, its size and design may make it unwieldy for more generalized excavation projects.
Attachment Options
Hydraulic Hammer
The hydraulic hammer attachment is designed to provide powerful impact force to break concrete or other hard surfaces. Its key characteristic is the ability to transform the mini excavator into a demolition tool. This makes it a beneficial option for projects requiring heavy-duty work, allowing for efficient and rapid demolition. A unique feature of the hydraulic hammer is its precise control, which allows operators to handle delicate structures without causing excessive damage. However, it is often associated with higher operation and maintenance costs, which should be considered.
Auger
The auger attachment is designed for boring holes in the ground, making it particularly useful for planting or fence-post installations. Its main advantage is the ability to create consistent and uniform holes with minimal disturbance to surrounding soil. The auger’s feature of various bit sizes caters to different drilling needs, from small holes for planting to larger ones for construction. However, it can be limited in its use on rocky or compacted soils, which can hinder its effectiveness.
Thumb Attachments
Thumb attachments are essential for improving the mini excavator's versatility in gripping and holding materials. They operate by adding a claw-like mechanism on the bucket, allowing for better control when grabbing and moving debris or heavy materials. The thumb's key characteristic is its ability to enhance the excavator's capabilities to perform tasks that require both digging and handling of objects. With a thumb attachment, a mini excavator can transition seamlessly between various tasks, boosting on-site efficiency. However, its installation and operation require proper training to prevent accidents.
Understanding the essential components of a hoe pack is fundamental to maximizing the efficacy of your mini excavator. Each bucket type and attachment option has unique characteristics that cater to varying job requirements, contributing to safe and effective operations.
Preparation for Packing
Preparation for packing is a crucial phase when it comes to mini excavators. This process ensures that all necessary equipment is organized and ready for transport. Proper preparation minimizes delays, reduces risks of damage, and promotes efficiency. Understanding the specific requirements of each job aids in making informed decisions about which equipment to bring. Without thorough preparation, workers may face unexpected challenges that could hinder operations.
Assessing Job Requirements
Assessing job requirements is a fundamental first step in the packing process. Each project presents unique needs, and knowing these will help tailor your packing list. Simply put, understanding the scope of work and the type of terrain can determine which attachments are necessary. For instance, a digging project in a rocky area may require a specialized bucket. Key factors such as duration of the task, expected weather conditions, and site layout must be evaluated. This assessment not only informs packing but also ensures that crew members are adequately prepared.
Inventory of Equipment
Keeping an inventory of equipment enables effective packing. It helps ensure that nothing essential is left behind. An organized equipment list guarantees readiness on site and reduces downtime.
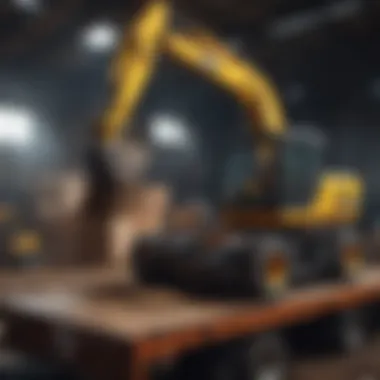
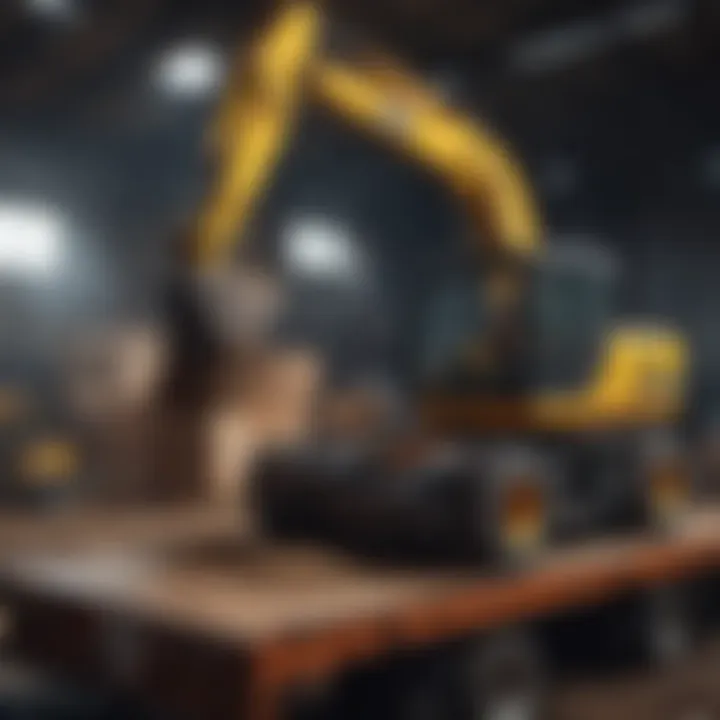
Necessary Tools
Necessary tools encompass the items that enhance the efficiency of the mini excavator. Common tools include wrenches, screwdrivers, and maintenance kits, which are essential for on-site repairs. Their primary characteristic is versatility—they can adapt to different tasks and situations. This aspect makes them a popular choice among operators. The unique feature of these tools lies in their portability, allowing for easy transport and access during operations. A well-thought-out selection of necessary tools is crucial for ensuring that any immediate repair requirements can be promptly addressed.
Safety Gear
Safety gear is indispensable for protecting workers during packing and operation. This includes helmets, gloves, and boots which are designed to withstand harsh conditions. The key characteristic is that these materials are often durable and resistant to environmental factors. The benefit of using quality safety gear cannot be overstated; it reduces the risk of injury, promoting a safer workplace. A notable feature is the comfort they offer, which enables workers to perform their tasks efficiently while remaining secure.
Load Planning
Load planning is vital to ensure that weight and equipment are balanced during transport. It requires careful consideration to achieve optimal stability.
Weight Distribution
Weight distribution ensures that the mini excavator is loaded evenly and within the transport limits. An even load helps maintain balance during transit. The primary characteristic of thoughtful weight distribution is its focus on safety—it aims to prevent tipping or swaying while driving. A good practice is to place heavier items nearest the trailer's axles, which enhances stability. Understanding this concept reduces risks involved in transportation and promotes a safer journey.
Stability Considerations
Stability considerations play a significant role in successful packing. They dictate how equipment is arranged on the transport vehicle. The emphasis here is on minimizing the center of gravity as much as possible. Proper stability prevents shifting loads that can lead to accidents. A noteworthy characteristic of focusing on stability is its impact on the entire transport process; it enriches safety measures by lowering the risk of accidents. Ultimately, applying these considerations enhances the overall packing and transportation experience.
Techniques for Packing a Mini Excavator
Understanding the right techniques for packing a mini excavator is crucial for effective and safe operation. Proper packing techniques not only ensure the integrity of the excavator during transport but also enhance efficiency on-site. By implementing these techniques, operators can minimize the risk of damage to the equipment and improve the overall workflow.
Loading the Mini Excavator
Loading a mini excavator involves strategic planning. First, ensure that the loading surface is level to guarantee stability. Loading ramps should be robust and suited for the weight of the excavator. Begin by operating the excavator onto the trailer or truck bed with caution, keeping the boom low to maintain balance. It is essential to center the excavator on the trailer to avoid shifting during transit.
Strapping and Securing
Once the mini excavator is loaded, securing it is vital. Use high-quality straps specifically designed for heavy equipment. The straps should be placed around the body of the excavator and tightened adequately to prevent movement. Make sure to check the straps after a short distance of travel. Over time and due to movement, there may be some loosening which requires adjustments.
Transport Considerations
Transporting a mini excavator safely involves several key factors, including understanding weight limits and selecting appropriate wagon types.
Weight Limits
Weight limits are a critical aspect when preparing for transport. It is important to know the maximum load your transport vehicle can handle. Exceeding these limits can lead to accidents and equipment damage. Most states impose weight restrictions on highways, which may require special permits for oversized loads. Staying within these limits not only ensures safety but may also prevent fines and potential legal issues.
Wagon Types
Choosing the right wagon type is equally important. Specialized trailers, like tilt bed and lowboy trailers, are often used for transporting mini excavators. Each type of wagon has its unique features which can impact loading and stability during transport. Tilt bed trailers simplify loading as they lower to the ground, making it easier to drive the excavator on. Lowboy trailers, while more stable, may require careful measuring to ensure adequate clearance for the excavator's height.
Taking the time to understand these techniques ensures an efficient moving process. Attention to detail in loading, securing, and transportation can make a substantial difference in the longevity of the equipment and success on the job site.
Safety Measures During Packing
The aspect of safety during the packing of mini excavators cannot be overstated. Proper safety measures ensure not only the well-being of the personnel involved but also the equipment's integrity during transport. Packing an excavator involves several risks such as equipment falling, injuries during loading and unloading, and mechanical malfunctions. Therefore, following safety guidelines is not only prudent but essential for any successful operation.
Personal Protective Equipment
Helmets
Helmets play a crucial role in ensuring safety on-site. They are designed to protect the head from falling objects or accidental impacts. A good helmet should meet regulatory standards, providing adequate coverage and comfort. A common choice among workers is the hard hat, which typically has an outer shell made from high-density polyethylene. This material is durable and can resist deformation under impact. While helmets provide excellent protection, their effectiveness may be compromised if they are not fitted properly or if they are damaged. Therefore, regular inspections for wear and tear are necessary.
Gloves
Gloves are another essential piece of protective equipment. They protect hands from sharp objects, extreme temperatures, and various substances that may be hazardous on the job site. High-quality work gloves, often made from leather or synthetic materials, ensure grip and dexterity while performing tasks. A key characteristic to look for in gloves is cut resistance. However, while gloves enhance protection, they can reduce dexterity if not chosen wisely. Thus, selecting gloves that fit well and are appropriate for the specific tasks is important.
Boots
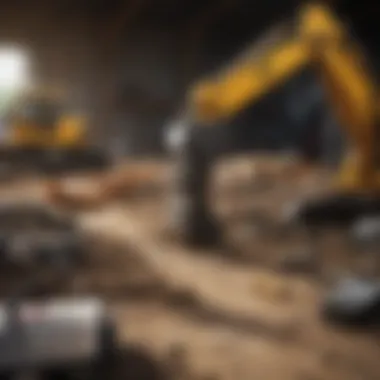
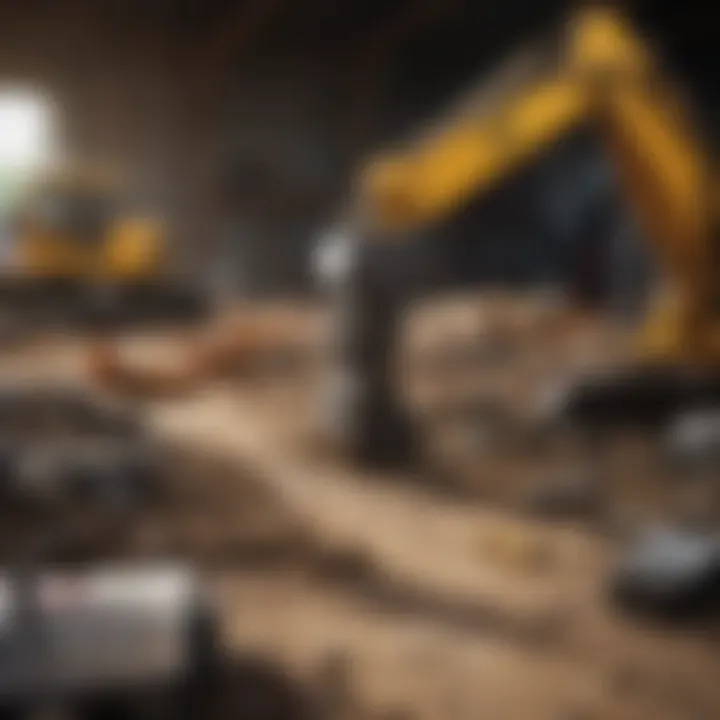
Footwear is vital for protection against injuries that can occur from heavy equipment. Safety boots usually come with reinforced toes that can withstand substantial weight and prevent crushing injuries. They are commonly made from leather or composite materials, offering both durability and comfort. The added benefit of slip-resistant soles also helps in preventing slips and falls in various working conditions. Nonetheless, it is crucial to ensure boots fit well, as ill-fitting footwear can lead to discomfort and affect mobility, particularly during busy operations.
Safe Loading Practices
Communication Signals
Effective communication is essential during the loading process. Clear communication signals prevent misunderstandings that could lead to accidents or equipment damage. Generally, hand signals or radios are used to convey important messages regarding loading and unloading procedures. A key advantage of establishing standardized signals is that they can be easily learned and recalled in high-pressure situations. However, without proper training, there can be confusion which may lead to unsafe conditions.
Loader Operation Protocols
Loader operation protocols are a set of guidelines that dictate the safest way to load and operate machinery. These protocols offer structured procedures that ensure tasks are performed correctly and efficiently. Including pre-operation checks and proper loading techniques are vital components of these protocols. One of the downsides, however, is that they require consistent training and adherence. Without a culture of safety and routine training, these protocols may be neglected, increasing the risk of accidents.
Following safety measures is not merely compliance; it is about fostering a culture of care and responsibility on the job site.
Post-Packing Procedures
Packing a mini excavator does not end with loading and securing the equipment. Post-packing procedures hold significant importance in ensuring the safe and effective transport of the excavator to its destination. These procedures help to affirm the integrity of the packing method and compliance with regulations, while also reflecting the operator's professionalism in handling heavy equipment. The post-packing process emphasizes checks and documentation, which play a crucial role in preventing future mishaps and ensuring all equipment is accounted for before traveling.
Final Inspection
Conducting a final inspection is essential to confirm that the mini excavator is securely loaded and properly balanced for transport. This involves checking the straps and any fastenings used to secure the machine. Ensuring that there are no loose or improper fittings can prevent damage to the equipment and reduce risks during transit. It is also advisable to inspect visibility from the transport vehicle. In some cases, it may be necessary to adjust the position of the excavator if it obstructs the driver's view. A thorough inspection can prevent accidents and ensure safe transportation.
Documentation
Having complete documentation is vital for any job involving heavy equipment. This includes verifying various documents that accompany the mini excavator during transport. Documenting every detail serves as proof of compliance and provides necessary information for logistics and accountability.
Loading Receipts
Loading receipts are a key component of this documentation process. These receipts not only confirm what has been loaded onto the transport vehicle but also outline the condition of the equipment at the time of loading. One specific aspect of loading receipts is their role in protecting all parties involved in the transaction. These documents are often used to resolve disputes over damaged or lost equipment during transit.
A significant characteristic of loading receipts is their detailed nature. They typically include information such as the time of loading, description of the equipment, along with any visible damage at the time. This detailed record is a beneficial feature for operators, as it ensures that there is a reference for the state of the equipment before it is transported. For added clarity, loading receipts help operators track items that might require follow-up inspections or repairs upon arrival.
Inspection Checklists
Inspection checklists complement loading receipts and serve their own important purpose in post-packing procedures. These documents are utilized to systematically verify that all necessary items and procedures have been addressed before transport. The checklist may include aspects such as verifying fuel levels, ensuring all components are securely attached, and confirming that safety gear is also loaded.
The key characteristic of inspection checklists is their structured approach. They help eliminate any chances of forgetting important tasks, making them a popular choice for professionals involved in the packing process. This systematic review aids in identifying any potential issues that could hamper safe transport. Additionally, checklists also serve as a record of the efforts taken to ensure compliance with safety norms.
Having a solid post-packing procedure enhances operational efficiency and minimizes potential issues during transportation. By ensuring every detail is attended to, operators demonstrate diligence and care in their work with heavy equipment while safeguarding their investment against loss or damage.
The End and Best Practices
In the context of packing for a mini excavator, the conclusion serves not just as a summary but as a reinforcement of critical practices learned throughout the article. Proper packing methodologies ensure not only the safety of the equipment but also the efficiency of operations on-site. Observing best practices can minimize the risks associated with transport, ensuring that both workers and equipment arrive safely at their intended location.
The importance of proper preparation cannot be overstated. By following the outlined procedures, professionals can avoid common pitfalls such as overloaded vehicles or disconnected logistics. It's crucial to establish a packing routine to follow for every job. This creates consistency and reduces the potential for errors.
Some key elements to consider when packing include:
- Ensure that all items are accounted for during the pre-packing inventory check.
- Double-check the weight distribution. This aspect is vital for stability during transport.
- Implement safety measures throughout the packing process to protect both personnel and the equipment itself.
Additionally, it is essential to foster a culture of continual improvement. The lessons learned from past packing experiences should inform future practices. By routinely reflecting on what has been accomplished and where there is room for improvement, operators can hone their skills further.
Summary of Key Points
This article has detailed the various aspects related to packing a mini excavator, focusing on:
- Understanding Mini Excavators: Explore definitions, types, and key specifications to comprehend the equipment better.
- Essential Components: Learn about various bucket types and attachment options that can enhance operational capability.
- Preparation for Packing: This includes assessing job requirements and preparing an inventory list to ensure nothing is overlooked.
- Techniques for Packing: Practical steps for loading the excavator properly and securing it for transport.
- Safety Measures: Emphasizing personal protective equipment and safe loading practices to prevent accidents.
- Post-Packing Procedures: Activities such as final inspections and maintaining documentation for accountability.
These points are integral for anyone involved in construction or excavation work, ensuring thorough preparation leads to safe and effective operations.
Continual Learning and Adaptation
In the field of mini excavator operations, the landscape is always changing. What works well today may need adjustments tomorrow. Continual learning and adaptation are essential for staying relevant and effective. This approach requires a willingness to advance one’s skills and knowledge, often through training, workshops, or peer feedback.
For practitioners, it could mean:
- Keeping abreast of new equipment and technologies on the market.
- Participating in hands-on training to refine packing techniques.
- Engaging in discussions with peers on best practices to exchange insights.
By embracing a mindset of growth, individuals and teams can better equip themselves to handle future challenges. It allows them to apply insights gained from past experiences and adjust methods as necessary. In turn, this leads to enhanced operational efficiency in the long run.