Exploring The Hillman Group's Screws for Professionals
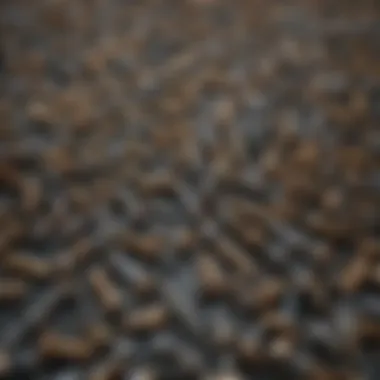
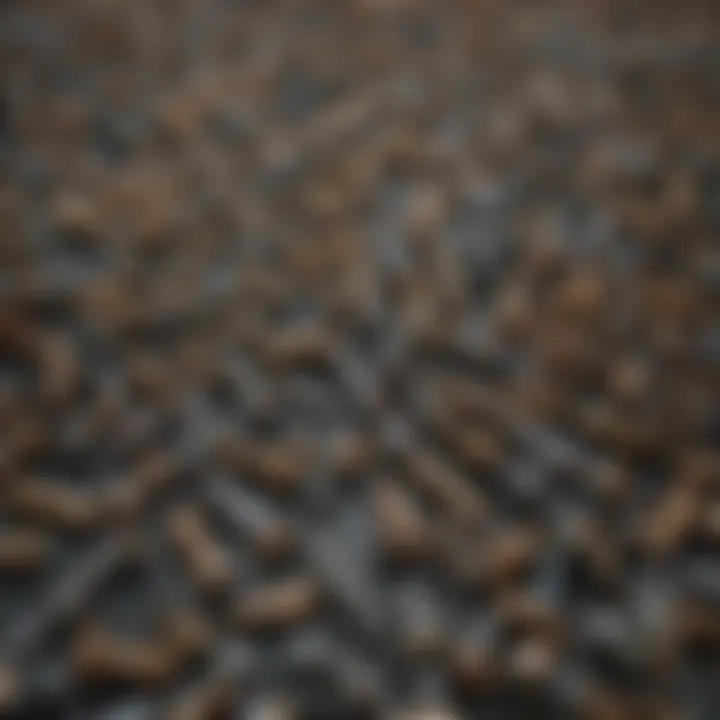
Intro
In various sectors, screws are often taken for granted despite their pivotal role. The Hillman Group, known for its extensive range of fasteners, provides screws that serve a variety of applications. It is essential to understand the nuances of these fasteners, particularly for professionals in agriculture. This article delves into the intricacies of screws produced by The Hillman Group, addressing key terms, relevance in agriculture, and practical applications.
Topic Overview
Understanding screws starts with defining what they are. Screws are essentially cylindrical shafts with helical ridges known as threads. They are used to join two or more materials together, providing a secure connection. Regarding The Hillman Group, the screws come in various materials and designs tailored for specific applications.
Definition of Key Terms
- Screw: A type of fastener typically made of metal that features a helical ridge.
- Thread: The helical structure wrapping around the screw shaft.
- Torque: The measure of the rotational force applied to tighten the screw.
- Material Compatibility: The ability of the screw material to interface with the application material without causing corrosion or degradation.
Relevance in Agriculture, Horticulture, and Agronomy
Screws produced by The Hillman Group play a crucial role in the agricultural sector. They are used in various machinery and equipment, including:
- Farm Implements: Essential for making durable agricultural equipment.
- Greenhouses: Utilized in construction for stability and durability.
- Irrigation Systems: Important for fastening components securely to prevent leaks.
These applications demonstrate how integral screws are in enhancing the efficiency and reliability of agricultural practices.
Current Trends and Innovations
The landscape of fasteners, specifically screws, continues to evolve with advancements in technology and materials. Understanding these trends can aid professionals in making informed decisions about their use in agriculture.
Recent Advancements in the Field
Recent advancements have focused on the development of screws that are resistant to rust and corrosion. This is particularly important for outdoor applications. The use of coatings and specialized materials ensures longevity in various environmental conditions.
Emerging Technologies and Practices
3D printing technology is beginning to impact the screw industry. While still emerging, it offers potential for customization and rapid prototyping of screws tailored to specific needs in agriculture. This innovation could lead to more efficient use of fasteners in various farming equipment.
Practical Applications
Selecting and using the right screws can significantly impact overall operational effectiveness. Understanding the best practices for installing screws is vital for their longevity and effectiveness in agricultural settings.
Step-by-Step Guides or How-Tos
- Choose the Right Screw Type: Consider the material and function. For example, stainless steel screws offer good resistance to rust.
- Inspect the Materials: Ensure compatibility between the screw and the materials being fastened.
- Pre-drill Holes as Needed: This helps prevent splitting of wooden materials.
- Apply the Correct Torque: Use a torque wrench to ensure proper installation, enhancing the screw's holding strength.
Tips and Best Practices for Implementation
- Always account for environmental exposure when selecting screw materials.
- Keep an inventory of various screw types for different applications.
- Train staff on proper installation techniques to maximize durability and safety.
"Screws, while often overlooked, are fundamental in creating resilient and effective agricultural structures and machinery. Understanding their specific uses can greatly enhance farm operations."
By recognizing the intricacies associated with The Hillman Group's screws and their applications in agriculture, professionals can make better, more informed decisions for their farming needs.
Preface to The Hillman Group
Understanding the role of The Hillman Group within the hardware industry is essential for evaluating the screws produced by the company. The Hillman Group stands out for its extensive selection of fasteners, especially screws, which find applications across multiple sectors, including agriculture. Knowledge of this company provides vital context for anyone looking to understand screws' technical specifications, design, and usability.
Their offerings are not just products; they convey a legacy of quality and innovation in screw manufacturing. This section will briefly present an overview of the company and its historical development, demonstrating its influence and relevance in hardware solutions.
Company Overview
The Hillman Group, founded in 1964, has established itself as a leader in the hardware and fastener market. The company specializes in providing a broad range of products, including screws, nuts, bolts, and various other fasteners. With numerous brands under its umbrella, Hillman offers customers significant choices tailored to diverse needs.
The company operates under a model focused on customer satisfaction. Its products are designed not just for performance but also for reliability. As such, they have become a trusted source for professionals and enthusiasts alike.
History and Development
The Hillman Group has undergone considerable transformation since its inception. Originally a small business, it has expanded through strategic acquisitions and a commitment to innovation in manufacturing processes. The firm has embraced technology, adapting to changing market demands, which has led to its reputation as a provider of dependable fastening solutions.
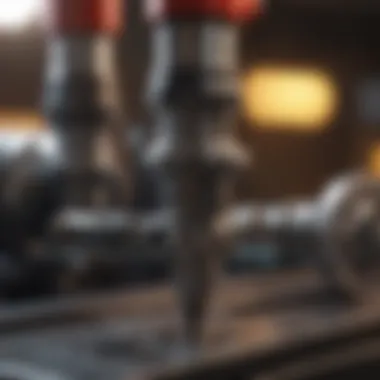
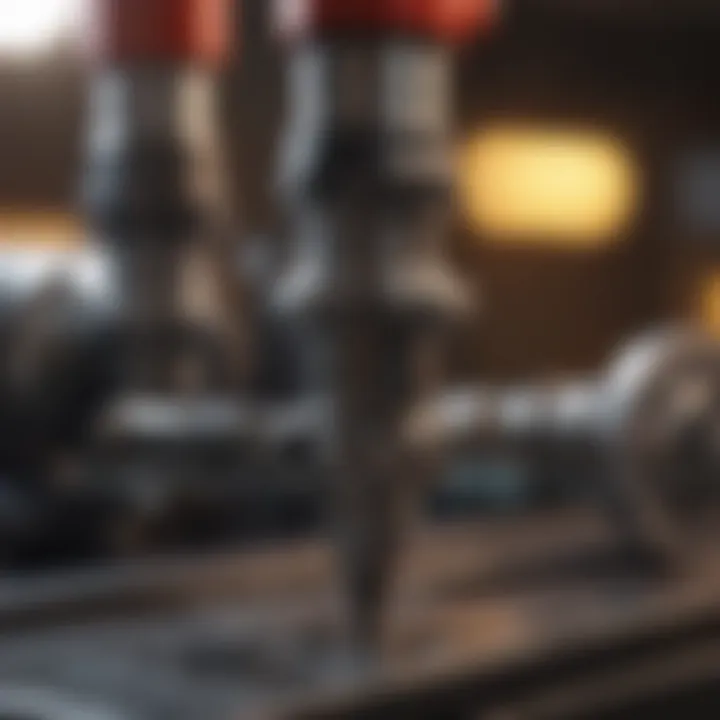
Furthermore, Hillman emphasizes continuous improvement. They invest in research and development, ensuring their products meet modern construction and agricultural needs. This forward-thinking approach is crucial for maintaining competitiveness in a rapidly evolving market.
In essence, understanding The Hillman Group lays the groundwork for evaluating its screws. This knowledge enables professionals—particularly in agriculture—to choose the right fasteners for their projects, ensuring both functionality and durability.
Types of Screws Offered
Understanding the various types of screws provided by The Hillman Group is essential for effective application and selection in agricultural practices. Each screw type serves unique functions and has different merits based on the materials and scenarios involved. This section will elaborate on four primary categories: wood screws, machine screws, self-tapping screws, and hollow wall anchors. Recognizing these distinctions can lead to improved choices and outcomes for farmers and enthusiasts alike.
Wood Screws
Wood screws are specifically designed for fastening materials like wood and are integral in construction and agricultural equipment. Their unique threading allows for superior holding power in wooden substrates, minimizing the risk of stripping or loosening over time. A common feature is a pointed tip, which facilitates easier penetration into wood fibers.
Key advantages of wood screws include:
- Durability: They can withstand considerable loads when properly installed.
- Versatility: Suitable for a range of timber types, making them ideal for agricultural structures.
- Ease of Use: The design often allows for direct insertion without pre-drilling, particularly in softer woods.
Farmers should consider the type of wood being used when selecting wood screws. Different wood species possess varying densities and hardness. Hellman Group offers an array of wood screw lengths and gauges, catering to specific project requirements.
Machine Screws
Machine screws are essential for securing metal parts together, which is common in machinery often used in agriculture. Unlike wood screws, machine screws can be used with nuts or tapped holes, providing a more robust connection between components. Their standardized sizes simplify selection based on the application.
Some of the benefits include:
- Strength: Capable of handling high tension, they are suitable for machinery that experiences significant stress.
- Precision: Available in varied lengths and diameters, allowing for tailored fittings in equipment design.
- Corrosion Resistance: Many machine screws come coated to resist rust, improving longevity in various environments.
It is vital for farmers to assess the mechanical components they are dealing with when choosing machine screws to ensure optimal fit and strength.
Self-Tapping Screws
Self-tapping screws are designed to create their own thread as they are driven into a material, typically metal or plastic. This feature allows for faster installation and can be especially beneficial in repair or assembly tasks. In agriculture, these screws can be crucial when assembling or modifying equipment quickly.
Benefits include:
- Efficiency: They reduce the need for machining or pre-drilling, saving time during installation.
- Adaptability: Suitable for a variety of materials, making them flexible for different agricultural applications.
- Reduced Risk of Errors: Their unique design minimizes the likelihood of misalignment during installation.
Farmers should take care when selecting self-tapping screws to match the material specifications to ensure effective application.
Hollow Wall Anchors
Hollow wall anchors provide a strong hold in drywall, which could be useful for building equipment sheds or storage units. These anchors are designed to expand behind the wall once inserted, distributing the load effectively.
Essential elements of hollow wall anchors include:
- Load-Bearing Capacity: Capable of supporting light to moderate weight, suitable for tool racks or shelving in agricultural buildings.
- Installation Flexibility: Easy to install in various wall thicknesses, allowing for adaptability in different structures.
- Visually Discreet: They do not protrude significantly, offering a cleaner aesthetic in installations.
Farmers should assess the specific requirements of their installation site when choosing hollow wall anchors to ensure that they meet the strength and stability needs of their projects.
Manufacturing Processes
Manufacturing processes are crucial in producing high-quality screws for various applications. For The Hillman Group, these processes not only define the physical characteristics of their screws but also ensure that the products meet industry standards and customer expectations. In an era where precision and durability are paramount, the methods selected for manufacturing can significantly impact the overall performance of screws.
Material Selection
Material selection is the foundation upon which the quality of screws rests. The Hillman Group commonly utilizes steel due to its strength and versatility. In addition, they offer screws made from stainless steel, which provides enhanced corrosion resistance, making them suitable for outdoor applications. Other materials, like brass or nylon, may also be employed for specific functionalities.
Choosing the right material affects several factors: durability, flexibility, and the ability to withstand various environmental conditions. For instance, screws made of carbon steel may be appropriate for indoor projects, but they may fail under moisture exposure unless coated. Thus, understanding the specific needs for agricultural environments is essential when selecting materials.
Production Techniques
The production techniques employed by The Hillman Group reflect a balance between advanced technology and traditional craftsmanship. The initial phase involves cold forming and hot forging processes. Cold forming is energy-efficient and allows for tighter tolerances, which is vital in applications requiring precise fit and function. Hot forging, on the other hand, improves material flow and strength but generally requires more energy.
Once the shaping is completed, screws undergo threading processes, which enhance their ability to grip materials securely. Thread rolling and cutting are common methods, each with its benefits. After threading, surface treatments like galvanization may be applied, ensuring additional protection against rust and corrosion.
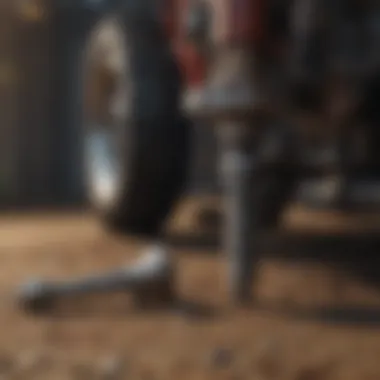
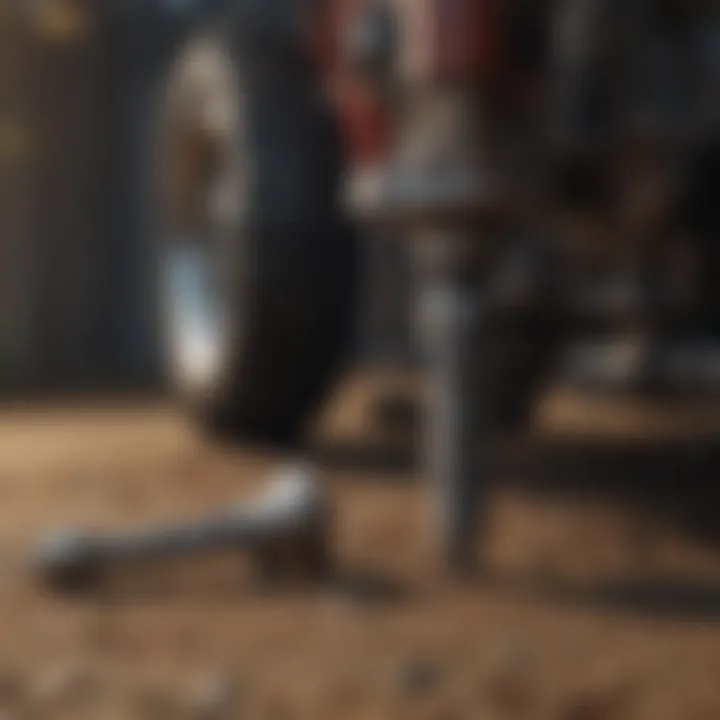
Quality Control Standards
Quality control is the backbone of The Hillman Group's manufacturing integrity. Rigorous standards are in place to monitor various stages of production. Inspections are conducted on raw materials, production processes, and finished products. Testing for dimensional accuracy and tensile strength ensures that each screw can withstand intended loads without failure.
The Hillman Group follows ISO standards and conducts audits regularly to maintain compliance. These practices safeguard against defective products reaching the market. The commitment to quality ensures that farmers and agricultural professionals can rely on the screws for their critical applications.
"A well-manufactured screw can make the difference between success and failure in agricultural projects."
Through understanding these manufacturing processes, users become informed about how different elements impact their selection of screws for agricultural needs. As they align expectations with product capabilities, decision-making becomes more effective.
Specifications and Standards
Specifications and standards are critical in ensuring the quality and effectiveness of screws produced by The Hillman Group. These guidelines not only dictate the dimensions and material grades of the screws but also assure the end-users about their performance in various applications. In agriculture, where screws are used in equipment and structures, adherence to specific specifications helps in maintaining safety and efficiency. Without proper standards, the risk of premature failure increases, which can lead to costly repairs and operational interruptions.
Dimensional Specifications
Dimensional specifications encompass the measurements and geometry of screws, which directly influence their fit and function in different applications. Hillman Group screws come in various sizes, lengths, and head styles to meet the changing needs of consumers. Precision in these dimensions ensures that the screws will fit properly into pre-drilled holes and engage adequately with other components. This is crucial in agricultural settings where the reliability of equipment is paramount.
- Thread Pitch: This refers to the distance between threads, affecting how well the screw grips materials. Different applications require specific thread pitches to optimize holding power.
- Length and Diameter: The correct length and diameter are essential for creating secure joins without risking structural integrity.
- Head Type: Various head styles, such as Phillips, slotted, or hex, affect how the screw is installed and removed, influencing ease of use in field conditions.
Strength and Durability Metrics
Strength and durability metrics play a vital role in the lifecycle and performance of screws. These metrics define how screws will withstand operational pressures and resist breaking under loads. The Hillman Group uses materials that adhere to recognized strength standards, ensuring that farmers can rely on the longevity of their hardware in the field.
- Tensile Strength: The ability of a screw to withstand pulling or stretching forces without failing.
- Shear Strength: This indicates how well a screw can resist sliding forces.
- Fatigue Resistance: Regular use can lead to wear over time, so screws must be capable of withstanding repeated cycles of loading.
Corrosion Resistance Specifications
Corrosion resistance is an important specification for screws, especially in agricultural environments exposed to moisture and chemicals. The Hillman Group incorporates various coatings and materials to enhance corrosion resistance, ensuring longevity and reliability.
- Coated Screws: Many screws feature zinc plating or other protective coatings to prevent rusting and degradation over time.
- Material Choice: Stainless steel is often selected for its natural resistance to corrosion, making it suitable for outdoor use.
- Test Standards: Engagement in standardized testing, such as salt spray tests, assesses how well screws can endure harsh environments without losing strength or function.
"Understanding specifications and standards not only influences the performance of screws but also contributes to overall project success."
Together, these specifications form the foundation upon which The Hillman Group builds its reputation for quality and reliability in screw production.
Choosing the Right Screw
Selecting the appropriate screw is imperative for achieving optimal performance in various applications, especially in agriculture. It impacts not only the structural integrity of installations but also operational efficiency. The Hillman Group offers a variety of screws designed for specific uses, and understanding these options will aid in making informed choices.
Application Considerations
When contemplating which screw to use, first consider the specific application. Different projects demand different attributes. For example, wood screws are essential for woodworking, as they have sharp threads that grip the material effectively. In contrast, machine screws are more suited for metal applications. Evaluating the demands of your project is crucial. Consider the following factors:
- Type of Material: Distinguishing between softwoods, hardwoods, metals, or composites will guide the selection.
- Load Dynamics: Determine whether the screw will face shear loads, tensile loads, or both.
- Environment: A consideration of environmental elements like moisture and temperature is needed for durability.
These considerations will direct one toward the right type of screw, preventing premature failure and ensuring longevity in operations.
Load-Bearing Requirements
Another critical factor in choosing the right screw pertains to load-bearing requirements. Each screw has a distinct load capacity, which is paramount for ensuring the safety and reliability of the installation.
- For heavy machinery or construction, one must choose high strength screws that can support the given weight.
- In softer materials like plastic or certain woods, screws with finer threads or those designed to expand within a hole should be used.
- Always refer to manufacturer specifications for load limits. This ensures that the screw will perform adequately under anticipated weight loads.
The right screw can make the difference between success and failure in structural integrity.
Environmental Factors
Environmental considerations underpin the choice of screws as well. Various factors can influence how screws perform based on their surrounding conditions.
- Corrosiveness: For outdoor applications, screws made of stainless steel or coated with corrosion-resistant materials are preferable to resist rust and degradation.
- Temperature Fluctuations: Thermal expansion can affect how screws hold up in extreme temperatures. Hence, screws suitable for high-stress or high-temperature environments should be selected.
- Chemical Exposure: In agricultural settings, exposure to fertilizers or pesticides may necessitate specialized coatings to prevent corrosion.
While selecting screws, assessing the environment in which they will operate is essential for durability and performance. In summary, thorough consideration of application, load-bearing capacity, and environmental conditions will ensure that the screws used from The Hillman Group not only fit the task effectively but also contribute positively to the larger project goals.
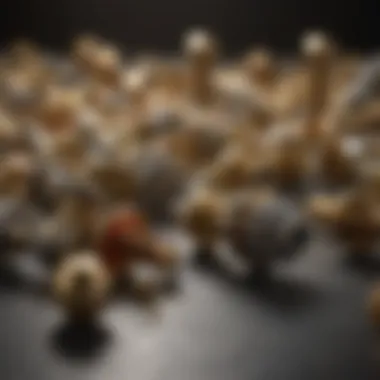
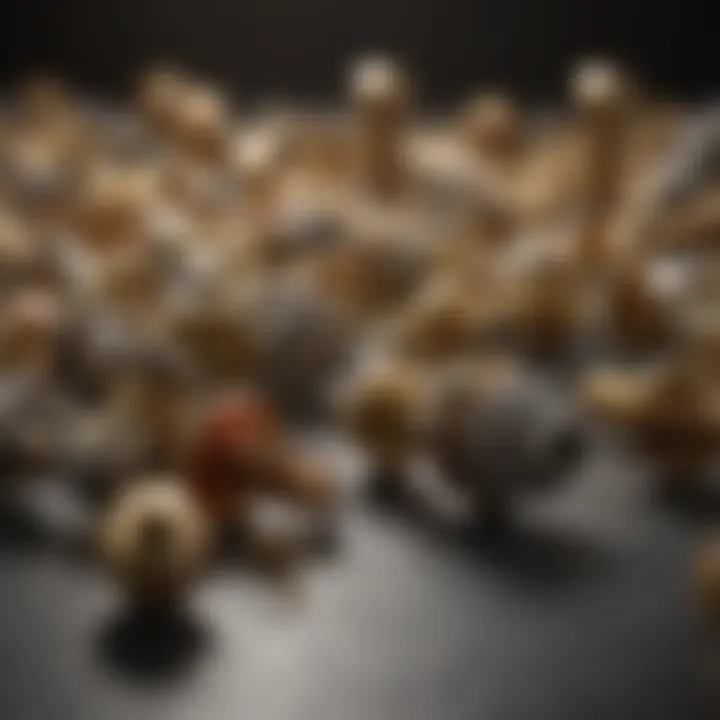
Installation Techniques
Effective installation techniques are crucial when working with screws from The Hillman Group. Proper methods can increase the lifespan of the installation and enhance the overall functionality of the hardware. This section will explore key considerations in screw installation, with specific focus on pre-drilling versus direct installation, torque requirements, and common mistakes to avoid.
Pre-Drilling Versus Direct Installation
The choice between pre-drilling holes and installing screws directly depends on several factors, such as material type and the application requirements. Pre-drilling involves creating a pilot hole before inserting the screw. This method is particularly beneficial when working with hard materials like hardwoods or metals. It reduces the risk of splitting wood and makes the insertion smoother, allowing for better alignment.
On the other hand, direct installation can save time, especially in softer materials. For example, self-tapping screws can often be driven directly into softer woods without damaging them. However, this can lead to issues if the screw generates excessive friction heat, potentially weakening its holding power. The decision should be based on material characteristics and installation efficiency.
Torque Requirements
Understanding torque requirements is essential for successful screw installation. The torque applied to the screw affects its holding capacity. Too little torque might not seat the screw properly, while too much can strip the material or break the screw itself. The torque needs can vary widely depending on screw type, size, and the material it's installed into.
Measurement tools like torque wrenches can help to apply the correct torque consistently. It is also vital to consider that various applications might have different torque specifications based on load-bearing needs. Ensuring the correct amount of torque can optimize the screw's performance, durability, and overall integrity of the joint.
Common Mistakes to Avoid
Inappropriate installation techniques can lead to significant problems. Some common mistakes arise from lack of knowledge or oversight. Here are several pitfalls to watch for:
- Inadequate Pre-Drilling: Bypassing pilot holes in hard materials can lead to splitting or cracking. Always assess material hardness before installation.
- Excessive Torque: Applying too much force can strip the screw head or damage the material. Knowledge of torque specifications is key.
- Incorrect Screw Type: Using a screw not designed for the material or application can result in failure. Selecting the right screw is essential.
- Neglecting Environmental Factors: Weather conditions and exposure can affect installation choices. Consider these factors to ensure longevity of the install.
Ultimately, paying attention to installation techniques and avoiding common errors can enhance the effectiveness of The Hillman Group screws, ensuring optimal performance for agricultural applications.
Environmental Impact
The consideration of environmental impact within the context of screw manufacturing is crucial. This section will elucidate the various factors at play, emphasizing sustainability, material recyclability, and lifecycle assessments. A thorough understanding of these elements not only assists manufacturers in adhering to ecological standards but also benefits end-users who are increasingly seeking sustainable solutions in their agricultural practices. The practices of The Hillman Group in this aspect reflect a commitment to reducing the negative impact on the environment while providing quality products.
Sustainability in Production
Sustainability in production involves creating products while minimizing resource depletion and harm to the environment. The Hillman Group implements various sustainable practices throughout their screw manufacturing processes. This includes the use of responsibly sourced raw materials, energy-efficient machinery, and waste reduction strategies.
- Resource Minimization: The company focuses on optimizing usage of metals and other materials in production, reducing excess and maximizing efficiency.
- Energy Efficiency: Employing advanced technologies allows for cost-effective manufacturing with lower energy consumption. This is particularly relevant in a world where energy conservation is paramount.
- Waste Management: Hillman adheres to strict guidelines for waste disposal, ensuring that excess materials are recycled or repurposed, rather than sent to landfills.
These practices not only lessen the environmental burden but also resonate with the values of consumers who prefer to engage with sustainable brands in their purchases.
Recyclability of Materials
The recyclability aspects of the screws produced by The Hillman Group are critical for sustainability efforts. Most Hillman screws are made from metals that can be easily recycled, thus contributing to a circular economy.
- Metal Recycling: Steel and aluminum, commonly used in screw production, have high recycling rates. Scraps generated during production can be melted down and remade into new products, reducing the need for virgin materials.
- Consumer Awareness: Educating customers about proper disposal methods ensures that the products can be effectively recycled at the end of their lifecycle. This not only encourages responsible consumer behavior but also aids in lowering the overall demand for new resource extraction.
By producing reusable and recyclable screws, Hillman fosters an understanding of how sustainable choices can assist in preserving environmental health.
Lifecycle Assessment
The lifecycle assessment (LCA) examines the environmental impacts of a product from its initial extraction of raw materials to its end-of-life disposal. The Hillman Group employs LCA to evaluate and improve the sustainability of its screws. This thorough approach provides insights into potential areas for improvement across several stages:
- Material Extraction: The sourcing of raw materials is assessed for its ecological impact, encouraging changes to more sustainable sourcing techniques.
- Manufacturing Phase: Scrutinizing energy use and emissions during production helps identify areas to implement more efficient technologies and processes.
- Usage and Maintenance: Evaluating how products are used in different applications can inform users on the best practices that prolong product life and performance.
- Disposal: By understanding how products are disposed of, Hillman can design products that take recyclability into greater consideration.
Finale
The conclusion of this article ties together the various facets of The Hillman Group screws, from their manufacturing to applications in agriculture. Understanding these aspects is vital for farmers and enthusiasts alike. The correct choice of screws can influence the durability and safety of agricultural projects, making informed selection essential.
Moreover, by recognizing the specifications, installation strategies, and environmental impacts, agricultural professionals can enhance their practices. It aids in making decisions aligned with sustainability goals while ensuring structural integrity in applications. The subsequent sections emphasize key points and future trends, guiding users to grasp how advancements can further benefit their endeavors.
Summary of Key Points
This article dissected crucial elements concerning The Hillman Group screws, including:
- Different types of screws and their specific uses in agriculture.
- Detailed manufacturing processes that ensure quality and reliability.
- Importance of selecting the right screw for appropriate applications.
- Installation techniques that can minimize errors and enhance performance.
- Environmental considerations related to screw production and utilization.
Each element discussed is pivotal in helping professionals navigate their choices effectively. Knowing these points articulates a clearer understanding of the hardware needs in the agricultural domain.
Future Trends in Screw Manufacturing
As industries evolve, screw manufacturing is also set to undergo significant transformations. Several trends are worth noting:
- Smart Manufacturing: The integration of technology will allow for precision machining, resulting in screws that meet exact specifications while reducing waste.
- Sustainability Efforts: Demand for eco-friendly materials is rising. Screw manufacturers, including The Hillman Group, will likely focus on biodegradable or recyclable materials.
- Customization: Growth in personalized solutions for specific agricultural applications can lead to an increase in tailor-made products that better serve farmers' needs.
- Innovation in Coatings: Advanced coatings can improve corrosion resistance and durability, making screws more efficient for various climates and conditions.
These trends signal the commitment within the industry to adapt to the changing needs of the agricultural sector. As farmers and hardware suppliers align with these developments, the overall effectiveness and sustainability of agricultural practices will improve.