Finding Reliable Toro Repair Services Near You
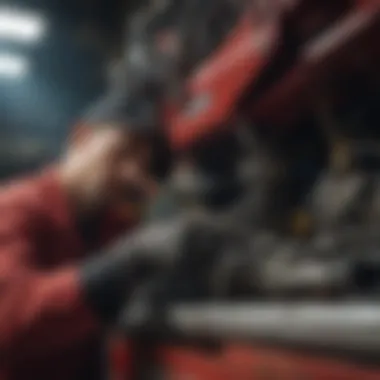
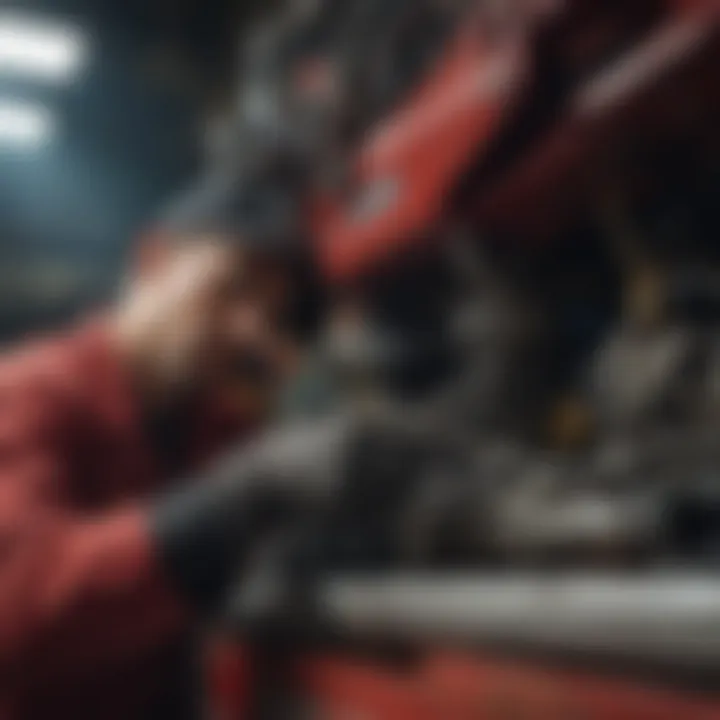
Intro
Locating reliable Toro repair services is crucial for anyone using Toro equipment, whether in agriculture, horticulture, or personal gardening. This need arises because equipment malfunctions can lead to costly downtime, affecting productivity and the overall health of cultivated plants. Understanding how to find these services will save time and ensure the longevity of your Toro products.
Key terms related to repair services, such as preventative maintenance, warranty claims, and service certifications, are essential to grasp. These terms help establish a common language when discussing repair needs and expectations with service providers.
Relevance in Agriculture, Horticulture, and Agronomy
Toro equipment plays a vital role in these fields. It includes a range of products such as mowers, tillers, and irrigation systems that are integral to efficient plant care and crop production. When any of these tools fail, it can create setbacks that hinder operational efficiency and crop yield. Thus, knowing how to locate dependable repair services becomes not just helpful but essential for success in farming and gardening endeavors.
Understanding Toro Equipment
Understanding Toro equipment is fundamental when seeking reliable repair services. Toro is known for its innovative designs and robust performance in landscaping and agricultural equipment. Having detailed knowledge about the products aids customers in making informed decisions regarding maintenance and repairs. Furthermore, familiarity with Toro equipment expands one’s ability to recognize potential issues early on, helping prevent costly repairs or breakdowns.
Overview of Toro Products
Toro offers a wide variety of products that cater to both commercial and residential needs. Their range includes lawn mowers, snow blowers, irrigation systems, and landscape maintenance tools. Many users rely on Toro's reputation for durability and efficiency, which is why understanding the specifications and operational requirements of particular models is crucial.
For instance, the Toro Recycler Lawn Mower is designed for easy handling and effective mulching capabilities, while Toro SnowMaster provides optimal snow clearing with a lightweight design. Knowing these product specificities enhances your capacity to convey issues accurately to repair technicians, leading to more efficient resolution of problems.
Common Applications of Toro Equipment
Toro products serve a multitude of applications, designed primarily for landscaping and turf management.
- Residential properties often utilize Toro lawn mowers to maintain lawns, resulting in even cutting and improved lawn health.
- Commercial landscapers rely on machines such as Toro zero-turn mowers for their efficiency and speed, ensuring vast areas are maintained in a timely manner.
- In agricultural settings, Toro’s irrigation systems facilitate adequate water distribution, promoting healthy crops.
- Seasonal products like snow blowers are essential in regions that experience heavy snow, ensuring pathways and driveways remain clear and safe.
Understanding these applications not only underscores the significance of proper maintenance but also highlights where one might need to seek repair services. Being informed enhances communication with service providers, ensuring an accurate understanding of equipment requirements and potential repairs.
Importance of Regular Maintenance
Regular maintenance is essential for the longevity and performance of Toro equipment. The benefits gained from routine care extend beyond mere functionality. Adequate maintenance can prevent major breakdowns and unexpected costs, ensuring that your equipment operates at optimal efficiency.
Benefits of Routine Maintenance
Routine maintenance provides several advantages:
- Enhanced Performance: Regular servicing helps keep the engine and other critical components running smoothly. This translates to better fuel efficiency and improved power output.
- Preventative Care: By identifying small issues before they escalate, you can avoid costly repairs. For instance, a simple oil change can prevent engine wear, extending its life considerably.
- Cost Savings: Investing in maintenance can save money in the long run. Repairs can be expensive, especially if equipment fails during peak work periods.
- Safety: Well-maintained equipment operates safely. Regular checks on brakes, lights, and other critical safety features reduce the risk of accidents or injuries.
- Higher Resale Value: A history of proper maintenance can enhance the resale value of equipment. Buyers prefer tools with good upkeep, knowing they come with reduced risks for future repairs.
Consequences of Neglect
Neglecting regular maintenance has significant drawbacks:
- Increased Breakdown Risk: Equipment that is not regularly maintained is susceptible to sudden failures. A breakdown can halt work and lead to costly delays.
- Higher Repair Costs: Small issues that are ignored can develop into major problems. Repairing or replacing a significant component is often much more expensive than routine maintenance.
- Reduced Safety: Failure to maintain safety systems can lead to dangerous situations. A malfunctioning brake or engine can endanger the operator and others nearby.
- Decreased Efficiency: As equipment ages without proper care, its efficiency diminishes. This can translate into higher operating costs, particularly concerning fuel consumption.
- Shortened Equipment Life: Equipment that does not receive regular maintenance will have a shorter lifespan. This means more frequent replacements and greater long-term costs for the user.
"Regular maintenance is not just beneficial; it is necessary for sustaining the value and functionality of Toro equipment."
In summary, regular maintenance is crucial for Toro equipment users. The advantages of consistent upkeep, ranging from enhanced performance to safety, cannot be overstated. Neglecting these practices can lead to dire consequences, affecting not just the equipment, but also the overall productivity and safety of operations.
Identifying Common Problems with Toro Equipment
Understanding the typical issues that can arise with Toro equipment is crucial for any user aiming to maintain optimal performance. Identifying these problems early allows you to minimize downtime and repair costs. This section will delve into the three main categories of common problems: engine issues, transmission problems, and electrical failures.
Engine Issues
Engine problems are often the first signs of distress in Toro equipment. An engine that does not start, runs roughly, or stalls can indicate several underlying issues. Common causes include fuel delivery problems, contamination, or worn-out components.
Regular inspection and maintenance are essential in preventing these issues. Cleaning air filters, checking fuel lines, and ensuring the correct oil levels can extend engine life. Users should also keep an eye on unusual sounds or smoke emission, which can highlight problems needing professional attention. Ignoring these signs can lead to more severe issues, necessitating costly repairs or replacements.
Transmission Problems
Transmission problems can severely impact the efficiency of Toro equipment. Users may notice issues like slipping gears or difficulty in shifting. These problems can stem from low fluid levels, worn-out seals, or internal damage. It is vital to inspect the transmission fluid regularly. Low levels can lead to inadequate lubrication and excessive wear.
Proper understanding of transmission components is beneficial. Familiarity with potential warning signs is also crucial. For example, delayed engagement when shifting gears often indicates underlying issues. Addressing these problems promptly ensures smoother operation and prevents larger repair needs later on.
Electrical Failures
Electrical failures present another common challenge. Toro equipment relies on electrical systems for starting, powering, and controlling various functions. Issues such as malfunctioning batteries, faulty wiring, or blown fuses can hinder performance.
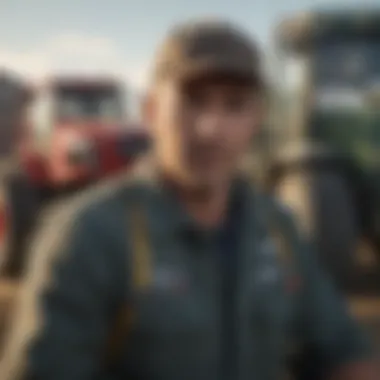
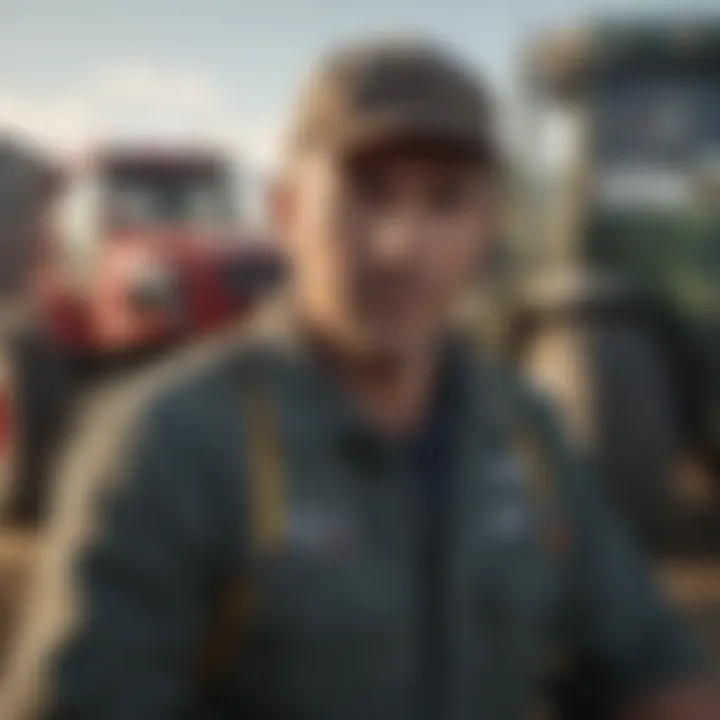
Routine checks on the battery condition and electrical connections can prevent most electrical issues. Look for corrosion on terminals or loose connections. Further, using manuals for troubleshooting can guide users in diagnosing some electrical problems. However, complex issues may require professional intervention, ensuring safety and proper handling.
In summary, understanding these common problems with Toro equipment is imperative for effective maintenance. Regular checks on engines, transmissions, and electrical systems ensure longevity while preventing unexpected breakdowns. For further reading on common mechanical issues, you may consider consulting sources such as Britannica or Wikipedia.
"Preventative maintenance is more effective and less expensive than waiting for problems to arise."
By staying vigilant and addressing these potential issues proactively, users can safeguard their Toro equipment's performance and reliability.
Locating Toro Repair Services
Finding reliable repair services for your Toro equipment is crucial for maintaining optimal performance and prolonging the life of your machinery. The right service provider ensures that issues are addressed efficiently, minimizing downtime and enhancing productivity. Moreover, locating these services allows you to build a trusted relationship with skilled technicians who understand the unique complexities of Toro products. In this section, we will discuss effective methods to find local Toro repair services, including online search strategies and using local directories.
Online Search Strategies
In today's digital era, many consumers start their search for services online. Locating Toro repair services through the internet involves several steps. First, use search engines effectively. Input relevant keywords such as "Toro repair services near me" or "Toro equipment repair". This helps generate a list of local service providers.
Additionally, take advantage of the geography features that various platforms offer to narrow your search results based on your location. Make sure to check each provider's website for detailed information about the services they offer, and any specializations in repairing specific Toro models.
Social media platforms can also serve as a valuable resource. For instance, engaging with local community groups on Facebook might lead to recommendations from other Toro equipment users. Another effective strategy is checking video platforms like YouTube, where repair tutorials and recommendations may guide you to trustworthy repair shops. When you find potential services, it’s wise to compile a short list for further consideration.
Using Local Directories
Local directories are a traditional yet reliable method for finding repair services. Websites like Yelp, Yellow Pages, and Angie’s List provide extensive listings of businesses in various categories, including machinery repair. When using these directories, look for repair shops with high ratings and positive reviews. Focusing on experiences shared by previous customers can offer insight into the service quality and reliability of each provider.
Moreover, consider narrowing your options by filtering for services that specifically mention Toro equipment in their description. This ensures the technicians possess the necessary expertise to handle your specific needs. Additionally, many directories list contact information, making it easy to reach out and inquire directly about services.
In summary, both online search methods and local directories are valuable tools for locating Toro repair services. Each approach has its benefits, and combining them can yield the best results.
Evaluating Repair Service Providers
Evaluating repair service providers is a critical step in maintaining and restoring your Toro equipment. In the realm of agricultural equipment, reliability and proficiency are indispensable. Finding a service provider who understands the nuances of Toro machines can determine the efficiency of your operations. This section discusses several key factors that contribute to a comprehensive evaluation of repair services.
Expertise and Qualifications
When assessing a repair service provider, the expertise and qualifications of the technicians are paramount. Knowledge of Toro products specifically is crucial. The right repair shop should employ certified technicians who have undergone formal training on Toro equipment. A provider with certified staff ensures that repairs will be done according to manufacturer standards.
It can be beneficial to inquire about their experience with specific models of Toro equipment. If your machine is specialized, such as a Toro Groundsmaster or Toro Dingo, it’s essential to find a provider that has dealt with these models before.
Consider the following:
- Certification: Look for certifications from Toro or related organizations.
- Training Programs: Check if staff regularly participate in training programs to stay updated on new technologies and methods.
- Accreditations: Check for any industry accreditations that speak to their professionalism and expertise.
Ultimately, a knowledgeable technician will diagnose issues faster and execute repairs more effectively, minimizing downtime and ensuring your equipment runs optimally.
Customer Reviews and Testimonials
Customer reviews and testimonials serve as a window into the service quality of repair providers. They reflect the experiences of others and help in making an informed decision. Trusting the words of previous clients can reveal insights about the provider’s reliability, customer service, and effectiveness in repair work.
Here are aspects to consider when reviewing feedback:
- Positive Feedback: High ratings and positive comments about service speed and quality can indicate a good choice.
- How Issues are Handled: Look for reviews that indicate how a provider addresses disagreements or mishaps. This speaks volumes about their customer service.
- Accessibility: Clients often mention how easy the service provider is to contact and discuss their needs. A provider who communicates well can build a better working relationship.
Online platforms such as Reddit and Facebook provide avenues for honest customer experiences. These reviews can offer a detailed perspective on the service provider’s local reputation.
The Role of Local Dealers
Local Toro dealers play a crucial role in the maintenance and repair of Toro equipment. They serve as a bridge between the manufacturer and the consumer, making them an important resource for anyone looking to ensure the longevity and efficiency of their machinery.
One of the primary benefits of local dealers is their expertise in Toro products. They are trained specifically to handle these machines, which means they can diagnose problems quickly and accurately. This expertise is especially valuable when dealing with complex issues, like engine malfunctions or hydraulic failures. Local dealers often provide specialized training to their technicians, ensuring that they stay up to date with the latest advancements in Toro technology. Therefore, when you visit a dealer for repairs, you are likely to receive top-tier service tailored to your specific needs.
Additionally, local dealers often have access to specific parts required for Toro equipment repairs. This brings us to the importance of authorized service centers and parts availability.
Authorized Service Centers
Authorized service centers can be found through your local Toro dealer. These centers are recognized by Toro and are equipped with the necessary tools and technology to service your equipment properly. Repairing Toro machinery often requires specialized knowledge and parts, and authorized service centers ensure this level of service.
Using an authorized service center guarantees that any repairs made on your equipment adhere to the standards set by the manufacturer. This not only protects your investment but also maintains the integrity of your machine. Authorized centers are more likely to use genuine Toro parts, which are designed to fit and function perfectly with your equipment.
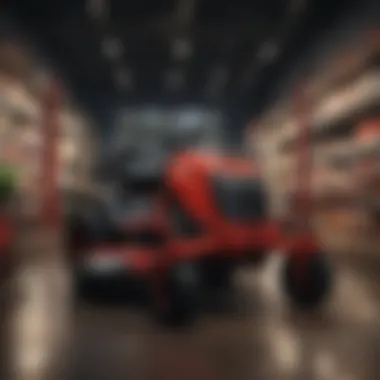
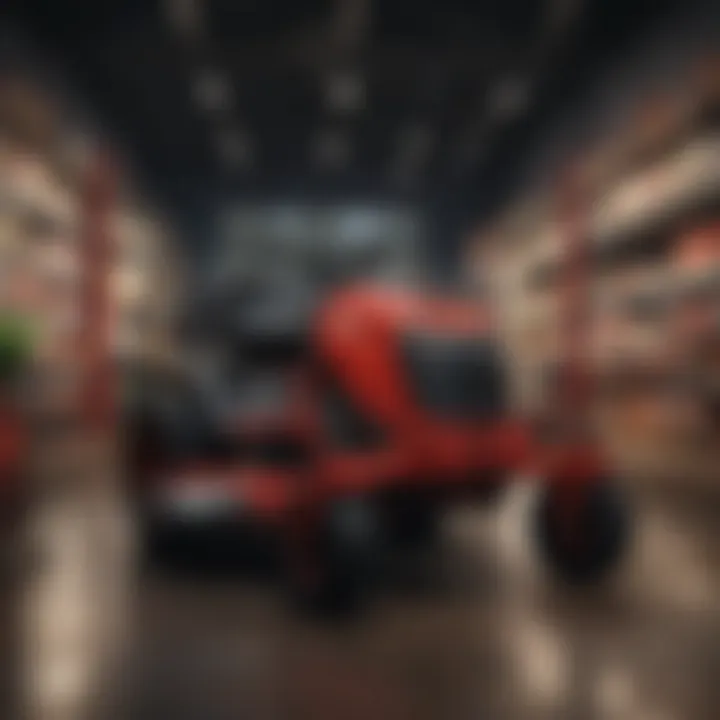
Parts Availability
Local dealers also provide a significant advantage in terms of parts availability. When your Toro equipment needs repairs, having access to the right parts is essential. Dealers stock a variety of parts, ensuring that repairs can be made without unnecessary delays.
It is worth noting that many repairs require genuine Toro parts for optimal performance and reliability. The use of non-genuine parts can lead to further problems and might void warranties. With local dealers, you benefit from a relationship that can provide quicker access to the correct parts, minimizing downtime.
"When you rely on a local Toro dealer for repairs, you're securing expertise and essential parts availability tailored to your equipment's needs."
Independent Repair Shops
Independent repair shops play a significant role in finding Toro repair services. They offer an alternative to authorized service centers, often providing competitive pricing along with personalized service. Understanding the overall advantages and disadvantages of these establishments is crucial for making an informed decision when choosing a repair service.
Pros and Cons of Independent Shops
When it comes to independent shop options, there are various elements to consider.
Pros:
- Cost-Effective: Independent shops tend to charge less than authorized dealers. They often have lower overhead costs, allowing them to offer favorable rates for services and parts.
- Flexibility: These shops may have more flexible working hours compared to larger authorized service centers. This can be convenient if you have specific timing needs.
- Personalized Service: Typically, independent shops provide a more personalized approach. You may find that the staff take the time to understand your individual needs and the nuances of your Toro equipment.
Cons:
- Varied Expertise: Not all independent shops have the same level of experience or knowledge regarding Toro products. This can lead to inconsistencies in service quality.
- Limitations in Availability of Parts: Obtaining OEM parts might be more challenging for independent shops. While they may source parts from various suppliers, there could be concerns regarding compatibility and warranty.
- Lack of Manufacturer Certification: Independent shops do not offer manufacturer-certified technicians, which can be a concern for consumers wanting assurance that their equipment is in expert hands.
Assessing Their Services
When evaluating independent repair shops, it is essential to conduct a thorough assessment of their offerings. Here are some recommended strategies:
- Check for Certifications: Although independent shops may not be manufacturer-authorized, look for any vocational training certifications or memberships in professional organizations.
- Request References: Ask the shop for references or testimonials from previous customers. This could provide insights into their reliability and service quality.
- Evaluate the Shop's Organization: A well-organized shop can reflect attention to detail. Look around for tools, cleanliness, and the way they interact with customers.
- Discuss Your Equipment: Engage in conversation about your Toro equipment. A knowledgeable technician should be able to discuss common issues and possible solutions confidently.
- Compare Estimates: Don't hesitate to gather estimates from multiple shops. This will help you gauge typical repair costs and identify any shops that seem overpriced or underpriced.
- Inquire About Warranties: Ask about warranties on parts and labor. A reputable shop should stand by their work, providing you with some assurance after service is completed.
Independent repair shops can offer unique benefits and challenges. Understanding these factors is key to ensuring your Toro equipment receives the best care possible.
By noticing these details and being proactive in your evaluation, you can decide if an independent repair shop is the right choice for your Toro equipment's needs.
Warranty and Service Agreements
Being aware of your warranty and service agreements is crucial when utilizing Toro equipment. These elements not only provide valuable protection but also enhance your overall maintenance strategy. Understanding the intricacies of your warranty can save you from unexpected expenses and extend the life of your equipment. As farmers and agricultural enthusiasts, knowing the details of your agreements allows you to make informed decisions about repairs and maintenance.
Understanding Your Warranty
A Toro warranty typically covers manufacturer defects and specific repair costs within a designated period. This timeframe varies among products, so knowing the duration and specifics of your warranty is essential.
- Coverage Details: Each warranty outlines covered parts and procedures. Familiarize yourself with items like engine or transmission coverage. Missing these details may lead to costly repairs not included in the warranty.
- Claim Process: Understanding how to file a claim is critical. Reach out to your local dealer or authorized service center to initiate a warranty claim if issues arise. Documentation is necessary, so keep all purchase records and service logs. This can strengthen your case for warranty claims.
- Transferability: Some warranties are transferable. If you sell your equipment, having a transferable warranty can add value. Verify with Toro whether your warranty can transfer to a new owner, as this can influence resale decisions.
A comprehensive understanding of your warranty empowers you to take action swiftly should any problems develop, ensuring you do not bear unnecessary costs.
Service Agreement Options
Beyond standard warranties, you may consider service agreements. These agreements provide a structured maintenance plan, which can significantly elevate the upkeep of your Toro equipment.
- Types of Agreements: Often, service agreements come in various formats, such as pay-as-you-go plans or fixed installments for scheduled maintenance. Evaluating what fits best your operational needs is key.
- Benefits of Service Agreements: Certain service agreements may include perks like annual tune-ups, priority support, and discounts on parts. These benefits enhance the longevity and efficiency of your equipment, which is vital for agricultural productivity.
- Customization: Some providers offer tailored agreements based on your equipment usage and specific farming practices. Engaging in a discussion with your dealer or service provider can lead to a customized plan that meets your unique requirements.
- Renewability: Check the terms regarding the renewability of these agreements. As your Toro equipment ages, having the option to renew can ensure continued service and support.
Conclusively, warranty and service agreements are integral aspects of owning Toro equipment. They help in managing repair costs and ensuring you have access to the necessary services to maintain optimal performance.
Cost Considerations for Repair Services
Understanding the costs associated with Toro repair services is essential for equipment owners. Repair costs can vary significantly based on several factors, including the nature of the repair, the specific equipment involved, and the location of the service provider. A comprehensive grasp of these elements ensures that you not only budget effectively but also choose the best option for your needs. In addition, being aware of cost considerations can help you avoid unexpected expenses that may impact your operation.
Factors Influencing Repair Costs
Many factors influence the overall expense of repairing Toro equipment. Recognizing these can assist you in making informed decisions. Here are some critical components:
- Type of Repair Needed: The complexity of the issue plays a major role. Minor repairs, such as replacing a filter, might be less costly than major engine repairs.
- Labor Expenses: Different repair shops have varying labor rates. Shops with specialized technicians often charge more due to their expertise.
- Parts Costs: Prices for replacement parts can fluctuate widely. Original equipment manufacturer (OEM) parts tend to be pricier than after-market alternatives, but they may offer greater reliability.
- Service Location: Urban areas often have higher costs for labor and services compared to rural settings. This is often due to the cost of living and availability of specialized technicians.
- Warranty Status: If your equipment is under warranty, some repairs may be covered. Always check your warranty terms to see what is included.
Estimating Total Costs
When estimating total repair costs, several methodologies can aid in deriving accurate figures. Here are some strategies:
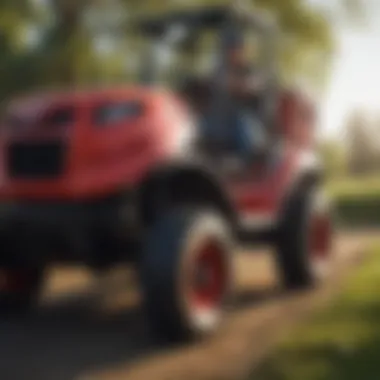
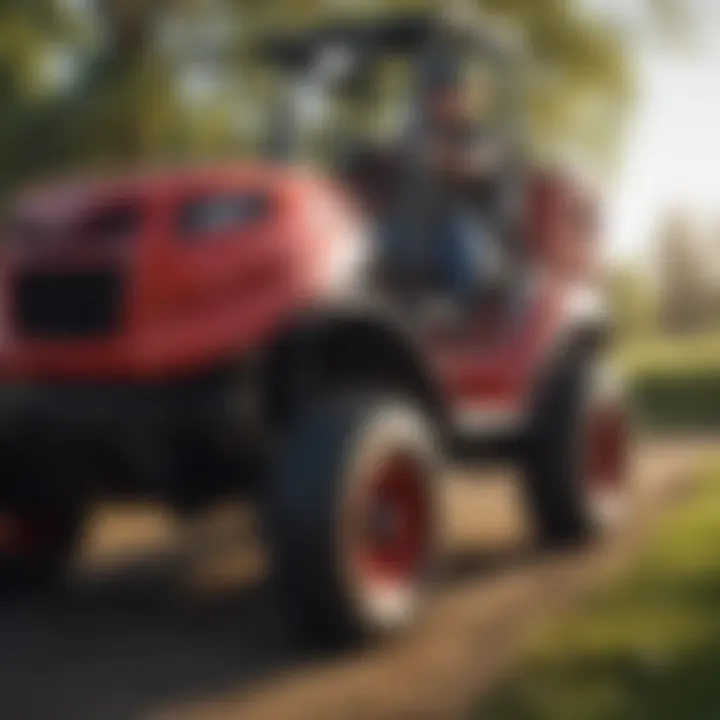
- Get Multiple Quotes: Before deciding on a service, obtain estimates from different repair providers. This gives a better sense of average market rates.
- Calculate Parts and Labor Separately: Assess the costs of parts and labor separately to understand where most of your budget will go.
- Consider Hidden Costs: Sometimes, quotes do not include additional fees such as diagnostics or disposal fees. Always ask for a detailed breakdown.
- Plan for Contingencies: Always have a buffer in your budget. Unforeseen issues may arise during repairs, increasing the overall cost.
- Review Service Agreements: If you have an ongoing service agreement, check what is covered under it, as this can change your total expected costs.
"Understanding and estimating repair costs can greatly aid in managing a budget for ongoing equipment maintenance."
By considering these aspects, you can make more informed choices regarding Toro repair services. This approach not only saves money but also helps in maintaining the functionality and longevity of your Toro equipment.
Creating a Repair Checklist
Creating a repair checklist is essential in ensuring your Toro equipment receives the necessary attention before it is taken in for repair. This proactive measure minimizes potential oversights and facilitates effective communication with service providers. A detailed checklist outlines the specific issues encountered, which can significantly streamline the diagnosis process. When repair technicians have a clear understanding of what problems are present, they can focus on these aspects, ultimately saving time and reducing repair costs.
Essential Items to Include
When compiling your repair checklist, it is prudent to cover key areas that can influence the performance of your Toro equipment. Here are some essential items to include:
- Model and Serial Number: Clearly document the model and serial number of your Toro equipment. This information helps technicians access the correct service manuals and parts for repairs.
- Detailed Description of Issues: Describe any specific problems you have observed. For instance, mention if the engine has not started, there are leaks, or strange noises occur.
- Last Maintenance Date: Indicating the last time maintenance was performed gives an idea of recent care and helps to identify if neglected maintenance contributes to the current issues.
- Operating Conditions: Note the conditions under which the equipment has been used. This includes the type of terrain, frequency of use, and any unusual incidents such as hitting an obstacle.
- Parts Replaced: If you have previously replaced any parts, document what was changed and when. This can indicate patterns of failure or recurring issues.
- Symptoms and Observations: Include any unusual symptoms like vibration, temperature changes, or warning lights. Even minor observations can aid in diagnosing complex problems.
Preparation for Service Visit
Preparing for the service visit goes beyond just creating the checklist; it involves ensuring that the technician has all necessary information readily available. Here are steps to ensure a smooth service visit:
- Organize Your Checklist: Keep the checklist concise and easy to read. Highlight critical issues or concerns so that they can be addressed quickly during the service.
- Clean Equipment: While it might seem trivial, cleaning the equipment can show the technician that you take care of your machinery, making it easier for them to perform their job effectively.
- Gather Documentation: Bring along any maintenance records, manuals, or previous service records. This helps the technician understand the equipment’s history.
- Ask Questions: Prepare a list of questions you may have regarding the repair process or recommended maintenance practices. Engaging with the technician can provide valuable insights.
- Be Available for Consultation: Ensure that you or a representative is available during the service if clarifications are needed.
Proper preparation significantly enhances the repair process and ensures that both you and your technician are on the same page. Knowing what to expect during your service visit can make the experience smoother and more productive.
By following these guidelines, you will facilitate a more effective and communicative relationship with your Toro repair service provider. This approach saves time and often leads to better maintenance outcomes.
Maintaining Your Toro Equipment
Maintaining Toro equipment is essential for ensuring its longevity and optimal performance. Like any machinery, consistent upkeep can prevent issues that may require costly repairs down the line. By investing in routine maintenance, Toro owners can improve the efficiency and reliability of their machines. This section outlines key tips for maintaining Toro equipment effectively while also offering common practices that can help keep your machinery in good working order.
Tips for Longevity
- Regular Inspection: Make it a habit to perform inspections before and after each use. Look for signs of wear, loose bolts, or leaks. Early detection can prevent bigger problems.
- Proper Cleaning: Clean your Toro equipment after each use. Debris can build up and cause parts to malfunction. Ensure that the undercarriage and cutting decks are free from grass or soil accumulation.
- Fluid Changes: Regularly check and change fluids such as oil, hydraulic fluid, and coolant. Each fluid has a life span, and neglecting this can lead to engine wear or breakdown.
- Inventory Check: Maintain an inventory of spare parts and accessories. Being prepared can reduce downtime when parts need replacement.
- Professional Servicing: Consider holding annual professional maintenance services. Experts can identify potential issues that an average user might overlook.
Implementing these practices can significantly extend the life of your Toro equipment, ensuring that it remains reliable and effective for your needs.
Common Maintenance Practices
- Blade Sharpening: Keeping blades sharp is crucial for cut quality. Dull blades stress the engine and may lead to uneven cutting. Sharpening them regularly will enhance performance and protect the engine's integrity.
- Tire Pressure: Maintaining proper tire pressure is vital. Deflated tires not only affect handling but also lead to uneven wear and can cause additional fuel consumption. Make sure to check tire pressure frequently to ensure they are adequately inflated.
- Battery Maintenance: Check the battery connections and clean any corrosion that may appear. A well-maintained battery will prolong its life and ensure reliable starting.
- Resistance Checks: Examine the electrical system for frayed wires or loose connections. Ensure that all lights and ignition systems are functioning correctly. This will contribute to overall operational safety.
- Storage Practices: Proper storage during off-season is fundamental. Clean the equipment and store it in a dry, protected area. Utilize covers to prevent dust and moisture from accumulating.
By adopting these common maintenance practices, Toro equipment owners can minimize breakdowns, enhance performance, and potentially preserve the resale value of their machinery.
Staying Informed on Product Updates
Staying informed on product updates is vital for a seamless ownership experience of Toro equipment. Regular information about your machines can significantly enhance their performance and longevity. Knowledge about updates can prevent unexpected problems and repair needs, keeping your equipment in peak condition. Furthermore, awareness of product changes can give you an edge in accessing better services and repairs.
Manufacturer Announcements
Manufacturer announcements play a crucial role in keeping Toro owners informed about their products. These notices could include information about new models, recalls, or important service updates. By subscribing to Toro's newsletter or following their official social media pages, owners can receive real-time updates directly from the source. This proactive approach means you won't miss critical information that could affect the efficiency of your machinery.
- Keep an eye on Toro's official site for new product releases.
- Register your equipment for notifications on recalls or important updates.
- Attend local or online Toro events where they showcase innovations and improvements.
Staying connected ensures that you are well aware of potential issues that could affect your equipment.
Technology Advancements in Toro Products
Technology advancements are continually reshaping efficiency and performance of Toro equipment. As a Toro owner, being abreast of these innovations allows you to leverage new features that can enhance your work processes. For example, updated models may come equipped with better fuel efficiency, improved cutting systems, or advanced diagnostic tools.
Industry trends often push manufacturers to enhance user experience. Embracing these advancements aids in maximizing the functionality of your equipment.
- Research recent technological improvements and how they compare with your current model.
- Utilize forums and community discussions on platforms such as Reddit or Facebook to gather insights and experiences from other Toro users.
- Consider upgrading if newer technology significantly impacts productivity in your work environment.
Technological literacy is an asset in the agriculture sector, and being aware of Toro's latest offerings can streamline operations, saving both time and resources.
Epilogue
Summarizing Key Points
- Understanding Toro Equipment: Familiarity with the product enables better comprehension of potential issues.
- Importance of Regular Maintenance: Regular checks can prevent bigger breakdowns, saving time and money.
- Identifying Common Problems: Knowledge of typical failures helps in troubleshooting before seeking repairs.
- Locating Repair Services: Knowing how to search online and utilize local directories can lead to quicker solutions.
- Evaluating Providers: Assessing qualifications and customer reviews ensures trustworthiness in service.
- Role of Local Dealers and Independent Shops: Each option offers unique advantages, from authorized parts to personalized service.
- Warranty and Service Agreements: Understanding these aspects can provide added security during repairs.
- Cost Considerations: Anticipating costs helps in budgeting for necessary repairs.
- Creating a Repair Checklist: Being prepared for service visits enhances the efficiency of repairs.
- Staying Informed: Keeping up with updates can help avoid obsolescence of tools.
Final Recommendations
When looking for Toro repair services, always begin with a clear understanding of your equipment and common issues. Use both online and offline methods to find potential service providers. Do not hesitate to check reviews and qualifications. Remember, whether you choose a local dealer or an independent shop, the focus should always be on expertise and customer service.
Finally, maintain regular upkeep of your Toro equipment. By doing this, you can minimize the necessity of repairs while optimizing your operational efficiency. Engaging with knowledgeable professionals and staying informed about your equipment will ultimately lead to more productive farming endeavors.