Essential Guide to Diesel Filter Cleaning Techniques
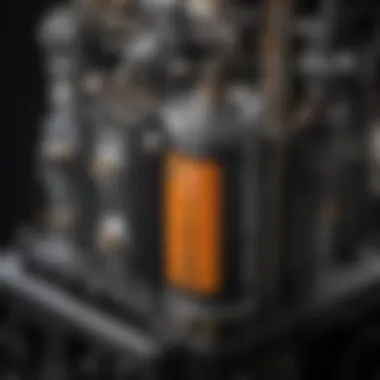

Topic Overview
Diesel filter cleaning is an essential process within the maintenance routines for diesel engines, notably where agricultural machinery is concerned. Diesel filters play a crucial role in the filtration system, ensuring that impurities do not enter the engine. These impurities can include dirt, water, and fuel contaminants, which can degrade engine performance. Therefore, understanding the methods and significance of diesel filter cleaning is critical for one’s machinery longevity and efficiency.
Definition of Key Terms
- Diesel Filter: A device that removes particles and water from diesel fuel before it enters the engine.
- Filtration System: A system composed of various components that work together to filter contaminants from the fuel.
- Contaminants: Foreign particles in the fuel, such as sediment, rust, and biological growth that can harm the engine.
Relevance in Agriculture, Horticulture, and Agronomy
In agricultural settings, diesel engines power many essential machines such as tractors, harvesters, and irrigation systems. Considering the rigorous demands placed on these machines, it is imperative to maintain the diesel filtration system. Neglecting the filtration system can lead to operational inefficiencies and costly repairs. By understanding diesel filter cleaning, agricultural professionals can optimize performance and extend service life of their equipment.
Current Trends and Innovations
Recent Advancements in the Field
Recent developments in diesel filter technology are shifting toward more efficient designs which enhance fuel flow while trapping even smaller particles. Certain models now incorporate dual filtration systems, which improve contamination removal rates. This is particularly beneficial for long operating hours typical in agricultural applications.
Emerging Technologies and Practices
New diagnostic tools are emerging, offering real-time monitoring of fuel quality and filter status. These technologies can alert operators to potential issues before they escalate. Incorporating software solutions that analyze engine performance data can also indicate the effectiveness of the filtration system, leading to smarter maintenance practices.
Practical Applications
Step-by-Step Guides or How-Tos
- Check the Filter: Begin by visually inspecting the diesel filter. Look for discoloration and signs of excessive dirt accumulation.
- Gather Required Tools: You will need a wrench, a cleaning solution designed for diesel filters, rags, and possibly a new filter.
- Remove the Filter: Use the wrench to loosen the filter. Be careful, as some residual fuel may spill.
- Clean the Filter: If the filter is reusable, submerge it in the cleaning solution and scrub gently. Ensure compliance with manufacturer specifications.
- Reinstall or Replace: After cleaning or if necessary, replace the filter with a new one. Ensure it's securely fastened.
Tips and Best Practices for Implementation
- Always follow the manufacturer's guidelines for specific cleaning methods.
- Schedule regular maintenance to prevent excessive contamination build-up.
- Keep spare filters on hand to minimize downtime during cleaning operations.
"Regular maintenance, including filter cleaning, is not just about keeping equipment running; it impacts productivity and efficiency significantly."
Understanding Diesel Filters
Diesel filters play a crucial role in the performance and longevity of diesel engines, particularly in the context of agriculture, where heavy machinery relies on reliable fuel systems. Understanding diesel filters involves recognizing their definition, their different types, and the significance they hold in ensuring efficient engine operation. This knowledge is essential for professionals seeking to maintain their equipment effectively and to avoid operational issues that can arise from neglecting these components.
Definition of Diesel Filters
Diesel filters are mechanical devices designed to remove impurities and contaminants from diesel fuel before it enters the engine. Their primary function is to filter out solid particles, such as dirt and rust, as well as water and microbial growth, which can significantly impair engine performance. Typically, a diesel filtration system consists of several components, including primary filters, secondary filters, and water separators. Understanding these filters' specific roles can greatly benefit individuals looking to optimize their diesel machinery.
Importance of Diesel Filters in Engine Performance
The importance of diesel filters in engine performance cannot be overstated. A clean diesel fuel system ensures that the engine receives optimal quality fuel, which directly affects its efficiency and reliability. Below are some key points that underscore this significance:
- Clogged filters can lead to insufficient fuel flow, resulting in power loss and increased fuel consumption.
- Contaminants that bypass the filter may cause wear and tear on engine components, leading to costly repairs.
- Regular maintenance and cleaning of diesel filters prevent breakdowns, minimizing downtime in agricultural operations.
It is also worth noting that neglecting the maintenance of diesel filters can lead to severe consequences. The decision to prioritize clean fuel systems not only enhances equipment longevity but also contributes to overall operational efficiency, providing a competitive edge for agricultural professionals.
"In the world of diesel mechanics, understanding your filters can save you time and money." - Diesel Mechanic Expert
Investing the effort to learn about diesel filters can lead to better decision making in maintenance practices, allowing for informed choices that keep machinery running smoothly.
Components of Diesel Filtration Systems
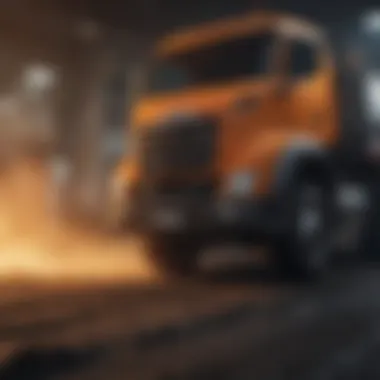

Understanding the components of diesel filtration systems is essential for maintaining diesel engines effectively. These systems play a vital role in ensuring fuel cleanliness, enhancing engine longevity, and promoting optimal performance. With poor filtration, contaminants can lead to engine damage and decreased efficiency. Thus, proper knowledge of the different components is necessary for effective maintenance practices.
Types of Diesel Filters
Primary Filters
Primary filters are the first line of defense in the diesel filtration process. Their main function is to remove larger particles and contaminants from the fuel before it reaches the more sensitive secondary filters. The key characteristic of primary filters is their capacity to handle a significant amount of dirt and debris, making them a beneficial choice for overall filtration systems.
One unique feature of primary filters is their ability to be serviced easily. Usually, they come with a simple design enabling farmers to replace or clean them regularly. However, one disadvantage is that over time, if not properly maintained, their efficiency can decline, leading to clogging that can affect engine performance.
Secondary Filters
Secondary filters serve as a subsequent layer of filtration after primary filters. This component is critical in filtering out smaller particulate matter and any remaining water. The key characteristic of secondary filters is their fine filtration capability, which enhances overall fuel purity. Because of this, they are considered vital for protecting high-precision components in the engine.
A unique aspect of secondary filters is their often replaceable filter element. This feature allows for more cost-effective maintenance without needing to change the entire unit. However, one downside could be their higher cost compared to primary filters, but they provide a crucial benefit by safeguarding engine integrity.
Water Separators
Water separators are integral for protecting engines from the harmful effects of water in diesel fuel. These filters specifically target and remove water, which can cause significant damage to engine components. The key characteristic of water separators is their ability to efficiently separate water from diesel through a process of coalescence.
A unique feature of many modern water separators is an automatic drain mechanism that allows for easy removal of accumulated water without regular manual intervention. While generally advantageous, one limitation may be that they can require more frequent servicing if the diesel fuel contains high levels of moisture, thus demanding vigilance from operators.
Filter Materials and Their Properties
Effective filtration depends significantly on the materials used in filter construction. Different materials offer various characteristics that can impact performance in distinct environments. Common filter materials include cellulose, synthetic fibers, and metal mesh. Each has its dexterity in capturing particles while ensuring adequate fuel flow.
Using the right materials not only aids in prolonging engine life but also maximizes efficiency. For instance, synthetic filters tend to offer higher dirt-holding capacities and longer service life, albeit sometimes at a higher initial cost.
The ongoing advancements in filtration material technology continue to improve the potential of diesel filtration systems, leading to better durability and efficiency.
Continuous advancements in standard filtration materials enhance the longevity and performance of diesel engines in agricultural machinery.
The Role of Diesel Filter Cleaning
Diesel filter cleaning is more than a routine maintenance task; it is a critical element in ensuring the longevity and performance of diesel engines, especially in agricultural applications. When filters are clean, they facilitate smooth fuel flow, which directly relates to fuel efficiency and overall engine performance. Keeping these filters in optimal condition can also lead to reduced emissions, aligning with modern agricultural practices that emphasize sustainability and environmental stewardship. As such, a sound approach to cleaning diesel filters is essential for any professional involved in the management of diesel-powered equipment.
Impact on Fuel Efficiency
One of the primary benefits of regular diesel filter cleaning is its significant impact on fuel efficiency. When filters become clogged with dirt, water, and other contaminants, the engine has to work harder to draw fuel. This increased effort leads to higher fuel consumption and, consequently, escalates operating costs for farmers and agricultural professionals. Studies show that clean filters can enhance fuel efficiency by as much as 10% or more, depending on the vehicle and operating conditions. Additionally, improved fuel efficiency directly contributes to better engine performance, enabling machinery to run at peak power.
Maintaining clean filters allows for optimal fuel atomization and combustion within the engine cylinders, which not only improves power delivery but also reduces the likelihood of misfires. Agriculatural machinery relies on precision; hence, it is critical to ensure filters are not a limiting factor for operations. In summary, clean diesel filters are crucial for maximizing fuel economy and engine power, thus enabling farmers to operate their equipment more effectively.
Consequences of Clogged Filters
Neglecting to clean diesel filters can lead to significant consequences, primarily manifesting as severe engine performance issues. Clogged filters restrict the flow of diesel fuel, often leading to fuel starvation in the engine. The implications of this can be serious. For instance, prolonged operation with clogged filters may cause the engine to stall or misfire, resulting in a lack of power delivery when needed most. This is especially critical during peak operations, such as planting or harvest season, where efficiency is paramount.
Moreover, the potential damage caused by neglected filters can incur high repair bills or even necessitate engine replacement in severe cases. Filters that are not adequately maintained can also contribute to increased wear on the engine components and can lead to premature engine failure. In a business sense, these consequences translate to downtime, which can affect productivity and profitability.
"A small investment in regular filter maintenance can save farmers significant costs and time in the long run."
The farming community must recognize the importance of regular filter cleaning and replacement in order to avoid these setbacks. Clogged filters are not just an inconvenience; they can cause extensive damage and affect the overall efficiency of diesel engines.
Methods of Diesel Filter Cleaning
Cleaning diesel filters is crucial for maintaining optimal engine performance. Filters can accumulate dirt and debris, which can significantly affect fuel efficiency and engine reliability. Understanding different cleaning methods can help ensure that the filters function effectively, minimizing downtime and repair costs. Here, we explore both manual and automated cleaning techniques, each offering unique benefits and considerations for diesel filter maintenance.
Manual Cleaning Techniques
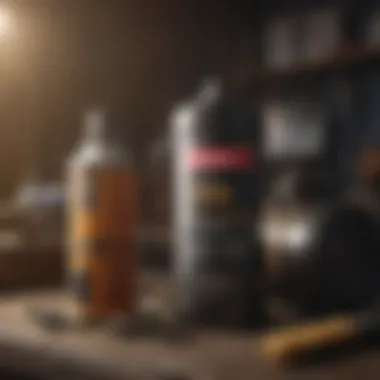

Dismantling and Inspection
Dismantling and inspection is a foundational aspect of manual cleaning techniques. This process involves removing the diesel filter from the vehicle and inspecting it for wear, clogs, or damage. The key characteristic of this method is the thoroughness it provides. Inspecting the filter allows users to assess its condition accurately, ensuring that cleaning efforts are targeted. It is a beneficial choice for those who wish to have a hands-on understanding of their diesel filtration systems.
One unique feature of dismantling is that it also enables the inspection of related components, such as hoses and fittings, which may also need attention. The advantage of this method is the ability to catch issues early, potentially preventing more significant problems down the line. However, this method does require mechanical knowledge and access to proper tools, which could be a disadvantage for some users.
Cleaning with Solvents
Cleaning with solvents is another manual technique used to maintain diesel filters. This method involves applying specific cleaning agents designed to dissolve contaminants that accumulate on the filter. The primary characteristic of solvent cleaning is its efficiency; it can effectively remove stubborn deposits that manual scrubbing might miss. Users find this method popular since it requires less physical effort compared to dismantling and inspecting.
The unique feature of solvent cleaning is its versatility. Different solvents may be used for various types of filters, providing tailored solutions. A significant advantage of this method is the reduced time spent on cleaning, allowing professionals to quickly get equipment back in service. However, a disadvantage is that some solvents can be hazardous, requiring safe handling and disposal practices. Proper ventilation and personal protective equipment are crucial when using solvents.
Automated Cleaning Systems
Automated cleaning systems offer advanced methods for diesel filter maintenance. These systems utilize technology to simplify the cleaning process, increasing efficiency and effectiveness. Among automative techniques, two prominent methods include ultrasonic cleaning and chemical bath cleaning.
Ultrasonic Cleaning
Ultrasonic cleaning utilizes high-frequency sound waves to agitate a cleaning solution, creating tiny bubbles that clean surfaces thoroughly. This method is highly effective for diesel filters, as it reaches areas that are often difficult to clean manually. The key characteristic of ultrasonic cleaning is its ability to clean intricate shapes without harsh scrubbing. This technology is popular for its precision and thoroughness.
One unique feature of this method is that it can remove microscopic impurities that manual techniques might overlook. The advantage of ultrasonic cleaning is its gentle yet effective approach, minimizing the risk of damaging the filter itself. However, the initial cost of ultrasonic cleaning equipment can be a barrier for some users.
Chemical Bath Cleaning
Chemical bath cleaning involves submerging filters in a bath of specialized cleaning chemicals. This method effectively removes dirt and contaminants without the need for intensive manual labor. The essential characteristic of this method is its effectiveness for heavy-duty cleaning tasks where filters are significantly soiled.
One unique feature of chemical bath cleaning is the versatility it provides. Different chemical solutions can be selected based on the level of contamination and filter material. The primary advantage is that this method allows for batch processing, making it suitable for large operations. However, the disadvantage lies in the need to manage and handle chemical solutions properly, which may require specific training and safety measures.
To maintain the longevity and efficiency of diesel engines, proper filter maintenance is essential. Both manual and automated cleaning methods provide unique advantages, making it important to choose a method that fits the specific needs of the equipment and user expertise.
Best Practices for Diesel Filter Maintenance
Maintaining diesel filters is essential for optimal engine performance and fuel efficiency. Ignoring regular maintenance can lead to decreased engine life and costly repairs. Best practices include regular inspection and timely replacement. These aspects not only extend the life of the filter but also ensure the entire filtration system works effectively.
Regular Inspection and Schedule
Setting up a regular inspection schedule is crucial in diesel filter maintenance. Farmers should check the filters at defined intervals, ideally aligned with regular service checks for their agricultural machinery.
- Frequency of Inspection: Depending on usage and environmental conditions, filters may need inspection every 100 to 500 hours of operation.
- Visual Checks: Look for signs of clogging or wear. Discoloration or visible dirt can indicate it is time to clean or replace the filter.
- Monitoring Performance: Pay attention to engine performance. A decrease in power or any irregularities can suggest filter issues.
Implementing a checklist can make this task easier:
- Review inspection schedule.
- Examine the physical condition of the filter.
- Check for leaks or unusual noises from the filtration system.
- Document findings for future reference.
Proper Replacement Guidelines
When filters become clogged or worn out, they need to be replaced. Following proper replacement guidelines ensures the filtration system maintains its efficiency. Here are some key points to consider:
- Select the Right Filter: Always use filters that meet the specifications for your machinery. Using OEM (Original Equipment Manufacturer) filters is usually a safe choice.
- Follow Manufacturer Instructions: Replacement processes can differ based on filter type and machinery. Review the service manual to understand the correct procedure.
- Perform a Clean Installation: Ensure that the mounting surfaces are clean before installing the new filter. Any dirt can compromise the filter's performance and cause premature failure.
- Dispose of Old Filters Properly: Environmental regulations often govern the disposal of used filters. Check local guidelines to ensure compliance.
Adhering to these practices not only ensures the effective operation of diesel filtration systems but also aids in reducing environmental impact. Regular maintenance diligence can result in significant cost savings in the lifespan of your machinery.
Challenges in Diesel Filter Cleaning
The process of diesel filter cleaning presents diverse challenges that demand attention from professionals and enthusiasts alike. These challenges directly influence the maintenance routines and overall efficiency of diesel filtration systems, particularly within agricultural machinery. Understanding these difficulties can lead to more effective strategies for keeping engines in optimal condition, which is crucial for maximizing productivity in the field.
Common Issues Faced
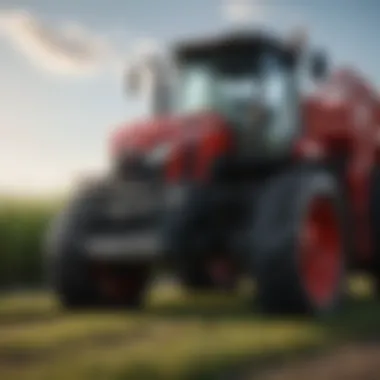

Access and Location of Filters
Accessing diesel filters can be a significant hurdle due to their positioning within the machinery. Filters may be located in cramped areas, making them hard to reach without removing other components. This complexity not only extends the time required for maintenance but also increases the risk of damaging surrounding parts. Adjustments like redesigning equipment for easier filter access can greatly enhance maintenance efficiency. It is vital to consider the layout of machinery when planning for regular cleaning or replacement tasks.
Incorporating easier access points can lead to quicker repairs and routine inspections. Thus, knowing the common locations for filters can save time and resources while ensuring consistent performance of the engine.
Material Compatibility and Selection
Choosing the right filter material is essential for effective filtration. Diesel filters are made from various materials like paper, synthetic fibers, or metal meshes, each having its own properties. It is important to select a material that can effectively capture particles without compromising the flow of fuel. Filtering materials that are not compatible with specific diesel types can lead to inefficiencies. The quality of the selected materials affects both the lifespan of the filter and the engine’s performance.
For instance, a filter with poor material selection can become clogged faster, leading to increased maintenance costs. Therefore, understanding compatibility and material selection is critical when maintaining diesel filters.
Environmental Considerations
Environmental factors also influence diesel filter cleaning. The proper disposal of used filters and cleaning solvents is necessary to minimize ecological impact. Many regions have regulations regarding waste disposal, particularly for materials that may be hazardous. Incorporating environmentally friendly practices, like using biodegradable cleaning agents, aids in sustainability efforts.
Engaging with local guidelines ensures compliance while promoting environmental stewardship. The choices made during the maintenance of diesel filtration systems can affect broader environmental health, emphasizing the importance of responsible practices in the agricultural sector.
Emerging Technologies in Diesel Filter Cleaning
Emerging technologies in diesel filter cleaning represent a significant evolution in how maintenance is approached for diesel filtration systems. These innovations offer new methodologies that cater to increasing demands for efficiency and sustainability in agriculture. Incorporating advanced technologies can enhance cleaning processes, ensuring filters work optimally and prolonging equipment lifespan.
Innovations in Cleaning Processes
Nanotechnology in Filtration
Nanotechnology is an emerging field that applies scientific principles to create materials at a microscopic scale. In diesel filter cleaning, nanotechnology can be utilized to enhance filter materials. One key characteristic is the ability of nanoparticles to improve the filtration process. They help capture smaller particles and contaminants that traditional methods might miss. As a result, fuel quality improves significantly, advancing overall engine performance.
The unique feature of this technology is that it often results in reduced maintenance needs due to the extended filter life. Farmers benefit from less frequent replacements, ultimately leading to cost reduction. However, one disadvantage could be the initial investment in nanotechnology-based filters, which may be higher than conventional options.
Smart Diagnostics for Filters
Smart diagnostics represents a shift toward data-driven maintenance practices. This technology involves using sensors and software to monitor filter performance continuously. The key benefit is the ability to detect issues early, allowing for proactive maintenance before significant failures occur.
The standout feature of smart diagnostics is its capability to analyze real-time data, providing insights into filter condition. This innovation leads to targeted cleaning processes, optimizing maintenance schedules based on actual need rather than guesswork. The downside might be the requirement for staff training to effectively interpret data and implement necessary actions.
Impact of Technology on Maintenance Practices
The influence of technology on maintenance practices for diesel filtration systems cannot be overstated. Automated cleaning processes, driven by innovations like nanotechnology and smart diagnostics, transform maintenance from a reactive to a proactive approach.
- Enhanced Efficiency: Modern technologies streamline workflow, significantly reducing the time required for filter maintenance.
- Cost Efficiency: Although upfront costs may be higher, the long-term savings on maintenance and improved equipment lifespan provide considerable financial benefits.
- User Empowerment: Farming professionals benefit from actionable insights provided by smart diagnostics, leading to more informed maintenance decisions.
The Future of Diesel Filtration Systems
The landscape of diesel filtration systems is evolving rapidly. Advances in technology, regulatory frameworks, and ecological considerations are redefining how these systems function. As the agricultural sector increasingly faces pressure to improve efficiency, reduce waste, and comply with stringent regulations, the future of diesel filtration will play a vital role in addressing these challenges. Understanding this facet is essential for farmers and mechanics alike, as it informs not only maintenance practices but also the long-term viability of diesel machinery.
Regulatory and Compliance Factors
Modern diesel filtration systems must adhere to strict regulatory standards. These regulations are often established by government bodies aiming to reduce emissions and protect environmental health. For instance, in many countries, diesel engines are required to equip advanced filtration technologies to meet emission limits. These regulations can affect the selection of diesel filters and their cleaning processes.
Incorporating advanced filtration systems may also require compliance with specifications set by equipment manufacturers. Failing to follow these requirements can lead to warranty voidance or reduced efficiency of equipment. Therefore, staying informed about local and international standards is critical for maintaining operational compliance.
Furthermore, the push for cleaner technology necessitates that farmers invest in training. This ensures that personnel are knowledgeable about the implications of current regulations. In summary, rigorous adherence to regulatory frameworks influences what filter systems are used, how they are maintained, and how effective they will be in the long run.
Sustainability in Filtration Practices
Sustainability has emerged as a pivotal concern in diesel filtration systems. In an era of climate awareness, the agricultural community is striving for techniques that not only enhance engine performance but also minimize environmental impact. Sustainable filtration practices may include the use of biodegradable cleaning agents or the adoption of filters designed for longevity, reducing waste generation.
Adopting sustainable filters can also lead to significant cost savings due to improved fuel efficiency. Renewable or recycled materials in filter construction help lessen the carbon footprint of diesel operations.
Additionally, integrating diagnostics and monitoring technologies can help farmers optimize their filtration processes. Understanding when a filter genuinely needs servicing — rather than following arbitrary schedules — can lead to reduced resource use and better environmental outcomes.
"Future-proofing diesel filtration systems through regulatory adherence and sustainable choices leads to ecological benefits and operational efficiency."