CNC Machine Hour Rate Calculation: A Complete Guide
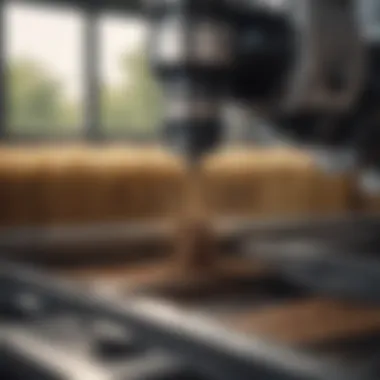
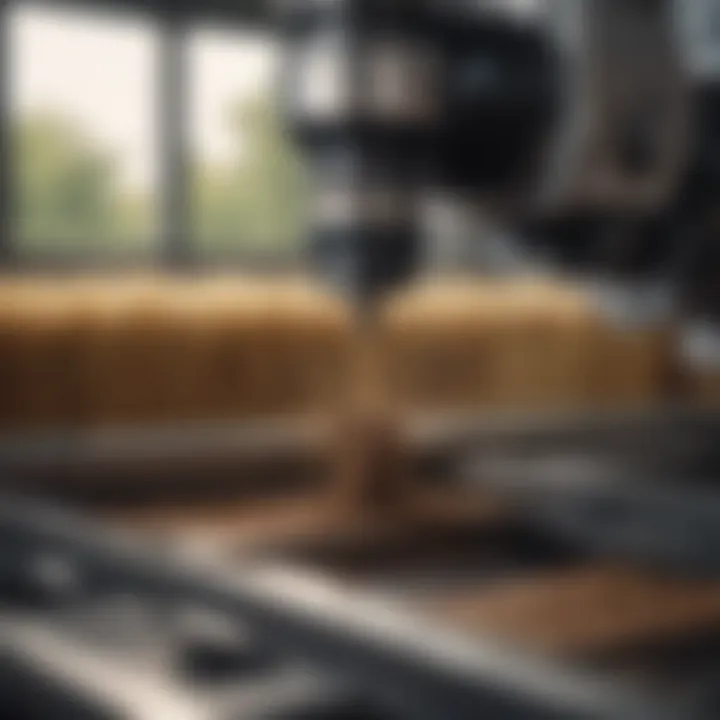
Intro
CNC machining has found a profound place within the agricultural sector, particularly as the demand for precision equipment increases. However, just knowing how to set up a CNC machine is one thing; being able to effectively calculate the hour rate can significantly tilt the scale towards profitability. With an increasing need to cut costs while boosting productivity, understanding these calculations is essential for farmers and agricultural professionals alike.
But what goes into calculating these rates? It isn’t just about the machine itself, but a medley of factors like maintenance, operational costs, and labor that weave into the broader picture. Let’s dig deeper into what this process entails, beginning with foundational concepts that are vital for any agricultural professional eager to optimize their CNC operations.
Understanding CNC Machines
CNC machines, or Computer Numerical Control machines, form the backbone of modern manufacturing and machining practices. They automate processes, allowing for precision and repeatability that is simply unattainable through manual means. This article focuses on the role of CNC technology in agriculture, emphasizing how understanding these machines is crucial for farmers and agricultural professionals looking to enhance their operations.
Overview of CNC Technology
CNC technology employs programmed commands to control machinery tools such as lathes, mills, and 3D printers. This precision equipment interprets coded instructions to perform intricate tasks, ranging from simple cuts to complex designs. By utilizing G-code, CNC machines can execute multiple operations without human intervention. This not only improves efficiency but also minimizes the likelihood of error, saving both time and resources.
Moreover, this level of automation encourages standardization across products, ensuring that each piece meets exact specifications. For the agricultural sector, where even the smallest variances can affect product quality and yield, CNC technology provides a significant advantage.
To break it down further, the key benefits of CNC technology include:
- Increased Precision: CNC machines maintain tight tolerances, essential for components used in farm equipment.
- Enhanced Productivity: Automation allows for continuous operation, reducing downtime and increasing output.
- Design Flexibility: Complex designs can be replicated easily, allowing for innovative agricultural solutions.
Applications in Agriculture and Horticulture
The landscape of agriculture has seen a notable transformation through the integration of CNC machines. Various applications highlight their versatility in farming and horticulture. For instance, CNC routers are increasingly employed to craft custom components for machinery and tools specific to farm needs. They can produce everything from bespoke planters to specialized harvesting tools that adapt to various crops.
Another significant application is in the manufacturing of precision parts for irrigation systems. CNC machines can create pipe fittings or drip irrigation components that require exact specifications to function effectively. This is particularly vital in areas where water conservation is paramount, allowing farmers to maximize yield while minimizing wastage.
To summarize, CNC machines play a pivotal role in:
- Parts Manufacturing: Crafting specialized tools and equipment for farming.
- Custom Fabrication: Building unique solutions tailored to specific agricultural tasks.
- Irrigation System Development: Producing precise components that improve efficiency.
The Importance of Hour Rate Calculation
Calculating the hourly rate for CNC machines is not just a matter of numbers; it's a critical aspect that influences various operational, financial, and strategic decisions in the agricultural sector. Understanding this rate helps farmers and agricultural professionals determine how effectively they can allocate resources and enhance productivity. The implications stretch far beyond simple cost assessment—it affects budgeting, project planning, and equipment utilization.
The relevance of hourly rate calculations is underscored by several key elements:
- Financial Transparency: Knowing how much it costs to run a CNC machine per hour helps in establishing transparency in financial dealings. This knowledge allows farmers to quote accurately for jobs, ensuring that all expenses are covered and profit margins are maintained.
- Resource Allocation: With a calculated hourly rate, farmers can make informed decisions regarding resource allocation. They can assess whether renting or purchasing CNC equipment will ultimately prove more cost-effective based on expected usage.
- Strategic Decision-Making: An accurate hourly rate provides data-driven insights essential for strategic planning. This can mean the difference between taking on certain projects or passing, based on their profitability.
- Cost Management: Understanding how various elements contribute to the hourly cost allows better control over expenses. Farmers can identify high-cost areas and modify practices to enhance efficiency.
In essence, calculating the hourly rate of CNC machines equips agricultural professionals with the tools to navigate a competitive market. Without this understanding, managers might find themselves in a quagmire of unforeseen expenses and ineffective strategies. Thus, the significance of this calculation cannot be overstated.
Defining Hourly Rate in CNC Context
In the CNC realm, the hourly rate is an aggregate of multiple variables. Primarily, it's calculated by combining all costs associated with running the CNC machine over a specific timeframe. This rate includes direct costs like labor and machine wear and tear, as well as indirect overheads such as utilities and maintenance.
While each operation will have unique cost structures, a basic formula helps lay the groundwork:
Hourly Rate = (Total Machine Cost + Labor Costs + Overheads) / Productive Hours
This formula not only serves as a benchmark but can be adapted depending on each operation's unique needs. In agricultural settings, knowing this cost can determine whether certain tasks are feasible or if they should be outsourced.
Impact on Project Budgeting
Budgeting is at the heart of any successful agricultural operation. When it comes to projects involving CNC machines, an accurate hourly rate becomes a pivotal element in shaping the entire budgeting process.
- Estimation Accuracy: Accurate hourly rate calculations allow for better estimates on project costs. If a machine is known to run at a specific rate, then project timelines can be adjusted accordingly, leading to more precise budget forecasts.
- Cash Flow Management: Understanding hourly rates assists in projecting cash flows more accurately. If a farmer knows their hourly rate, they can predict when to expect revenue from completed projects, thus aiding in effective financial planning.
- Risk Assessment: By grasping how machine rates fluctuate with market conditions, farmers can assess potential risks and prepare contingency plans. This proactive approach can safeguard against volatile swings in costs and revenues.
"In agriculture, precision matters—whether in planting or budgeting. Knowing your CNC machine's hourly cost can mean the difference between thriving and just surviving."
All these factors underscore that calculating the CNC machine’s hourly rate is not merely a technical requirement but a strategic necessity. Properly defined and understood, it opens up avenues for improving both operational efficiency and profitability.
Key Components Affecting Hour Rates
When it comes to calculating the hour rate for CNC machines, there are several key components that play a crucial role. Each of these elements influences the overall cost structure, affecting how a farmer or agricultural professional budgets for their operations. Understanding these components can mean the difference between a profitable venture and a financial burden.
Equipment Costs
Equipment costs represent a significant portion of the hour rate calculation. This encompasses both the initial investment and the ongoing expenses related to maintaining and operating the CNC machinery.
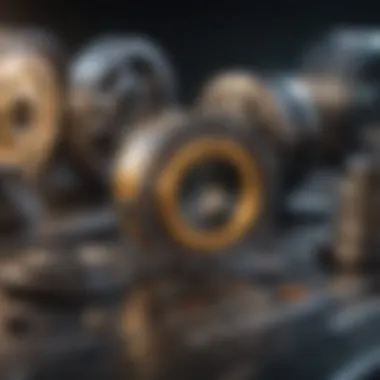
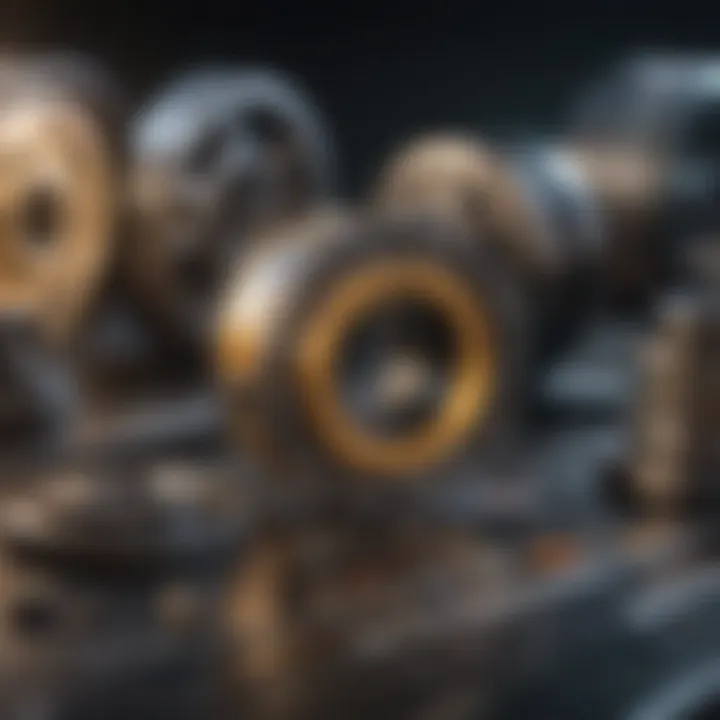
- Initial Purchase Price: The price paid for the CNC machine sets the foundation for all related calculations. This amount can vary dramatically, from a basic model for hobbyist use to advanced, high-capacity machines designed for commercial farming.
- Maintenance and Repairs: Over time, even the most robust machines require upkeep. Setting aside budget for regular inspections, parts replacement, and unexpected repairs is essential. Failing to do so can lead to downtime, which further increases operational costs.
- Resale Value: It's also critical to consider the depreciation of the machine. As years pass, some of its value may erode, impacting future plans for financial recovery. Keeping an eye on how market trends affect resale values can guide decision-making when it's time to upgrade or sell.
Labor Expenses
Labor costs are another key factor in calculating the hour rate. These go beyond just the wages paid to the CNC operators; they capture a broader spectrum of labor-related expenses.
- Skilled Operators: Skilled labor in CNC operations often commands higher pay due to the expertise required. Investing in training can yield dividends, as proficient operators can maximize machine capabilities.
- Workforce Efficiency: The productivity of the labor force also affects profitability. An efficient team can reduce machine idle time, thereby driving down the effective hour rate. Observing how each team member contributes to workflow can help identify areas for improvement.
- Benefits and Overheads: Beyond wages, benefits such as health insurance and retirement contributions can substantially impact costs. These should be factored into the hourly rate calculation to offer a clearer picture of total expenses.
Operational Overheads
Operational overheads are sometimes overlooked but play a vital role in the hour rate equation. These are the indirect costs associated with running the CNC operations.
- Utilities: Power consumption by CNC machines can pivot costs significantly. With electricity prices on the rise, it's wise to track energy usage carefully to keep expenses in check.
- Facility Costs: Renting or maintaining a workshop space also adds to the overhead. Whether it's a small shed or a large production facility, these costs must be divided over the hours of operation to find a fair hourly rate.
- Insurance and Licensing: Protecting your equipment and ensuring compliance with local regulations incurs costs that need careful consideration.
"When you factor in every piece of the puzzle, from equipment to labor to operational costs, the actual cost of running a CNC operation can surprise even seasoned professionals."
In summary, each of these components, from equipment costs to labor expenses and operational overheads, plays a pivotal role in defining the CNC machine hourly rate. Understanding these factors is crucial for anyone in the agriculture sector, as it enables better planning and helps in maintaining a healthy bottom line.
Methods for Calculating Hourly Rate
Calculating the hourly rate for CNC machines is a process that can mean the difference between profit and loss. Particularly in sectors like agriculture, where margins can be tight, understanding and applying the right method to determine this rate is critical. Each method has its pros and cons, making it vital to assess which is most appropriate for the specific context.
Direct Cost Method
The Direct Cost Method is one of the simpler approaches to estimating hourly rates. This method focuses solely on the expenses that can be directly attributed to the machine's operation, such as:
- Machine depreciation: Over time, machines lose value. Accounting for this loss ensures you're not operating at a loss by the time a project wraps up.
- Energy consumption: CNC machines do not run on air. You need to calculate the electricity used per hour.
- Maintenance costs: Regular upkeep keeps machines in prime condition but also costs money. These should be factored in as per usage intervals.
This method can be beneficial for farms just dipping their toes in CNC operations. By explicitly identifying variable costs, it can offer a clearer picture of what it takes to operate a CNC machine for any specific task. However, it lacks the broader overview of fixed expenses, which can lead to skewed results if the costs are not monitored over time.
Markup Method
The Markup Method takes a different angle. Here, the hourly rate is set by applying a percentage increase to the total direct costs. This approach is especially useful for farmers looking to ensure a profit margin on CNC operations. Typically, you might see something like:
Total Cost of Operation + (Total Cost of Operation × Markup Percentage) = Hourly Rate
For instance, if direct costs amount to $50 per hour and you decide on a 20% markup, the final rate would be:
- Calculation: $50 + ($50 × 0.20) = $60
This method provides a nice cushion for unforeseen expenses or losses, covering not just direct costs but also allowing a buffer for profit or reinvestment into operations. The downside, however, is that farmers must be careful not to set the markup too high, as that would make their services less competitive in the market.
Cost-Plus Pricing Strategy
The Cost-Plus Pricing Strategy blends both direct costs and a guaranteed profit. It’s somewhat similar to the Markup Method but usually involves calculating total costs, and then adding a fixed amount or percentage. This is significant because:
- It ensures all costs are recuperated.
- You have a set profit that can contribute to business growth.
The formula might look something like:
Total Costs (Fixed + Variable) + Desired Profit = Hourly Rate
For example, if all costs total $70 per hour and the desired profit is set at $30, then the hourly rate would be:
- Calculation: $70 + $30 = $100
This approach can be particularly beneficial for larger projects where comprehensive planning allows for a detailed breakdown of both fixed and variable costs, ensuring all bases are covered.
In practice, picking the right method depends largely on individual circumstances, such as the competitiveness of the market, the stability of input costs, and the unique operational setups that each farmer or agricultural company may face. Understanding the nuances of these methods can aid in crafting a more sustainable operational budget and ultimately lead to better financial health.
Calculating Depreciation of CNC Machines
Calculating depreciation of CNC machines is more than just a number on a balance sheet. It's an essential undertaking for any agricultural professional looking to manage finances prudently. Understanding how depreciation affects the lifetime costs of CNC equipment can help farmers and producers make better budgeting decisions. It helps identify when it's time to upgrade or replace machinery, ultimately impacting productivity and financial health.
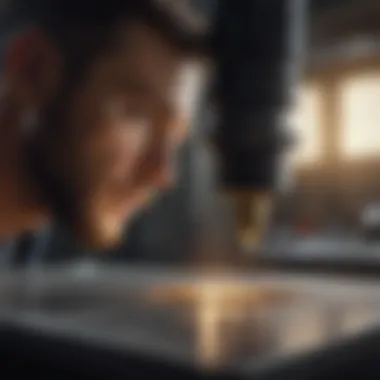
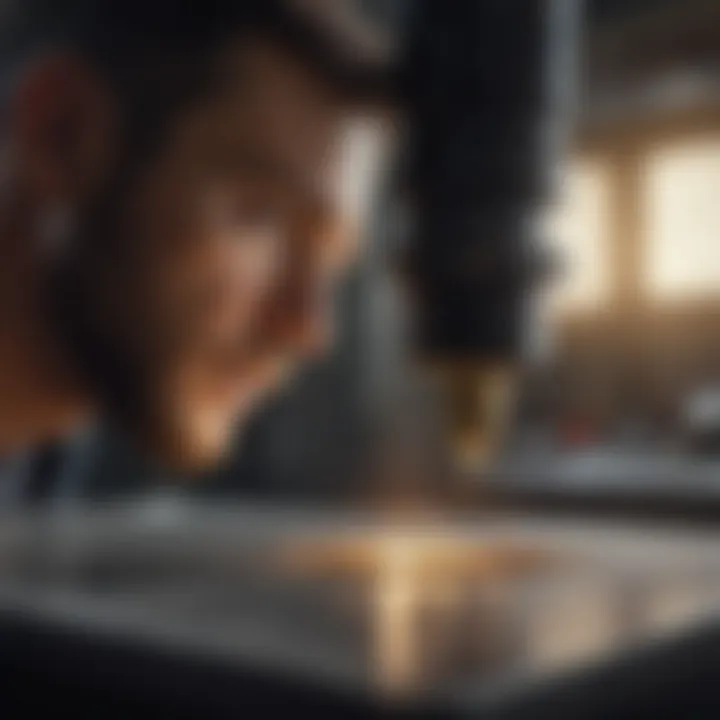
This section delves into the various aspects of depreciation, its significance in the agricultural sector, and how it can play a role in effective resource management for CNC operations.
Understanding Depreciation
Depreciation refers to the decrease in the value of physical assets over time due to wear and tear, age, or obsolescence. For CNC machines, this means recognizing that the equipment will not hold its initial purchase price indefinitely. As a CNC machine is used extensively in tasks like planting, harvesting, or processing, it incurs wear and tear, which affects its value.
In agriculture, the insights gained from tracking depreciation can inform not just equipment cycles, but also tax considerations, ensuring that farmers don't miss out on potential deductions. Knowing how depreciation functions provides a framework that helps in planning for future investments. A farmer must incorporate these calculations into their overall financial strategy for optimal effectiveness.
Methods of Depreciation Calculation
There are various methods for calculating depreciation, but two popular ones stand out for their utility in the context of CNC machinery in agriculture: the Straight-Line Method and the Declining Balance Method. Each method has its merits and drawbacks, and selecting the right one depends on individual operational needs and financial strategies.
Straight-Line Method
The Straight-Line Method is straightforward—an asset's cost is evenly spread over its useful life. One of its key characteristics is simplicity; farmers can easily apply it without needing complex financial tools. This method assumes that a CNC machine will lose value consistently over time, which makes financial forecasting much simpler.
Since it results in the same depreciation expense each period, it provides predictability in budgeting for equipment costs. However, while it's easy to understand, it may not accurately represent the actual usage and wear on the machine, especially if the use fluctuates throughout its lifespan.
Key Points:
- Easy to calculate and predict expenses.
- Great for consistent operations.
- May not reflect actual value loss in variable conditions.
Declining Balance Method
The Declining Balance Method presents a different approach. It calculates depreciation based on the current book value of the asset, leading to higher deductions in the earlier years of use. The main characteristic of this method is its accelerated depreciation, offering the potential for tax benefits sooner rather than later.
With CNC machines, the concept of obsolescence can be significant. By using this method, a farmer could recognize that a CNC machine loses functionality or value quicker at the beginning of its life due to the rapid evolution of technology in agriculture. However, this method requires more detailed tracking and can be tricky if the equipment is used irregularly.
Key Points:
- Accelerated depreciation is advantageous for early tax deductions.
- Reflects the more realistic value loss of rapidly changing technology.
- More complex, requiring diligent bookkeeping and calculations.
Understanding the methods of calculating depreciation is crucial for any agricultural business operating CNC equipment, as it impacts budgeting, financial planning, and ultimately, productivity and profitability.
Case Studies in Agricultural Applications
In the realm of CNC machining, there is a pressing need to understand how these technologies integrate within agriculture. Examining real-world applications helps illustrate both the theoretical and practical aspects of CNC machine hour rate calculation. Case studies present valuable insights that can benefit stakeholders in farming, from optimizing productivity to understanding potential pitfalls.
Utilizing case studies in agricultural applications is not simply an academic exercise; it bridges the gap between theory and real-world practice. For farmers and agricultural engineers, these case analyses can offer critical lessons that pave the way for better decision-making processes. They reveal the multifaceted nature of CNC technology and its economic implications. Observing outcomes from both successful and less favorable implementations can lead to more informed strategies, ultimately enhancing operational efficiencies.
Successful Implementations in Farming
Successful case studies in farming illustrate how CNC technology can revolutionize traditional practices. For instance, a farm in California integrated CNC routers to automate the cutting of plastic seed trays. This automation not only reduced the time taken for production but also improved the uniformity of the trays, yielding a more efficient planting process. The hourly rate was calculated effectively by analyzing the direct costs associated with machinery and labor but was complemented by the savings realized from improved production efficiencies.
These successful implementations resonate beyond mere financial savings. They serve as a blueprint for farmers looking to adopt advanced techniques. Precise scheduling of machinery operation can significantly reduce idle time, which lowers the overall hourly rate. Additionally, improved machinery quality and better maintenance practices ensure that equipment remains operational and minimizes unplanned downtime. In more complex cases, some operations have leveraged CNC technology to tailor equipment to specific farming tasks, resulting in higher yield from carefully managed resources.
"Seeing tangible benefits from technology can often lead to greater buy-in from farmers who might be skeptical about its implementation."
Lessons Learned from Failures
On the flip side, it’s equally important to study the failures in CNC applications within agriculture. An illustrative example involves a large-scale wheat farm that invested in CNC grain handling systems without thoroughly considering the local labor market. The technology was top-notch, but the farmers underestimated the associated training costs for their staff. The initially calculated hourly rate appeared attractive on paper, but when labor expenses tripled due to training and turnover, the operation became unsustainable.
Another noteworthy failure occurred when an organization attempted to implement a complex CNC machine for precision planting without the necessary integration into existing farming workflows. The machine often broke down during peak planting seasons, resulting in costly downtimes and subsequent lost opportunities. The case highlights the fact that understanding labor rates and equipment compatibility is crucial before making investments. Such blunders not only inflate the calculation of the hourly rate but also hinder the overall trust in CNC technology.
Both success and failure stories teach important lessons. Engaging with these narratives equips agricultural enthusiasts with a more nuanced understanding of CNC operations. As technology evolves, ensuring that farmers are equipped with accurate information becomes essential. Studying these cases promotes a more exhaustive approach to implementing CNC technologies, ultimately helping to refine the hourly rate calculations essential for budget management.
Challenges in Hour Rate Calculations
Calculating the hourly rate for CNC machines is a complex endeavor, fraught with challenges that can easily trip up even seasoned professionals. Recognizing these challenges is key, as they not only affect the accuracy of your calculations but also can have broader implications for project success and budgeting. In an industry striving for efficiency, understanding these obstacles can lead to more informed decisions, ultimately translating to cost-effectiveness and better resource management.
Fluctuating Costs of Components
One of the significant hurdles in determining the hour rate is the fluctuating costs of the raw materials and components necessary for CNC operations. Prices might change abruptly due to market fluctuations, trade tariffs, or supply issues, leaving businesses in a bind when it comes to accurate budgeting. For instance, if a farmer relies heavily on aluminum for their agricultural machinery, any sudden hike in aluminum prices can skew their calculated costs dramatically.
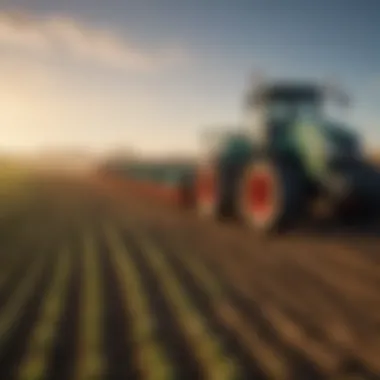
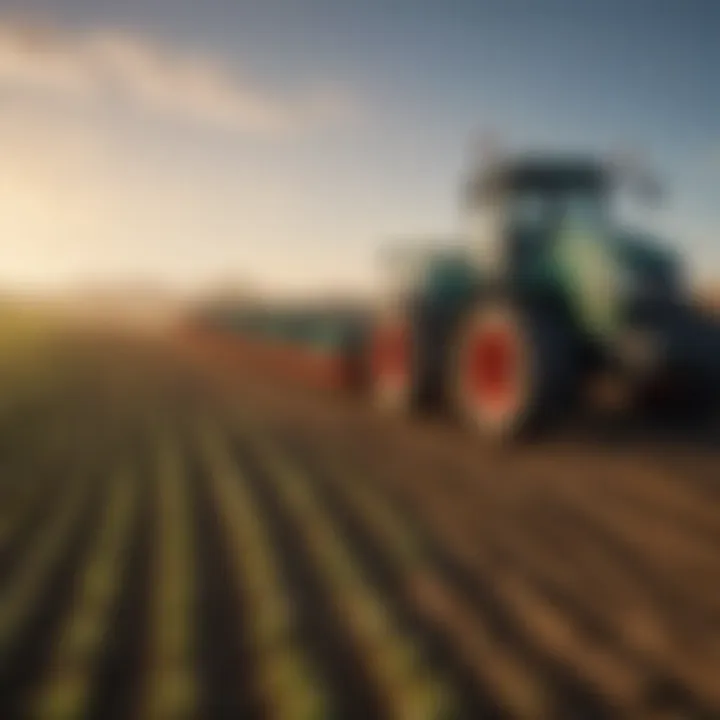
To navigate this, consider developing a buffer system to account for such fluctuations. Maintaining a close watch on market trends and having alternative suppliers can also mitigate risks associated with cost unpredictability. Integrating these practices into your calculations can enhance both accuracy and reliability.
Variability in Labor Rates
Another facet that complicates hour rate calculations is the variability in labor rates. Labor costs can fluctuate based on various factors such as regional wage disparities, skill levels of workers, and economic conditions. For instance, a skilled operator in a metropolitan area might command a much higher wage than one in a rural setting, affecting the overall cost for operating CNC machinery.
To address this challenge, it might be helpful to establish a consistent method for evaluating labor costs. Regularly reviewing pay rates, considering seasonal variations in labor availability, and factoring in potential overtime can provide a more rounded view of labor expenses. A detailed payroll analysis can help you pinpoint not just the costs but also the skill levels required to operate different CNC machines effectively.
Maintenance and Downtime Concerns
Lastly, maintenance and downtime are the ever-looming specters in CNC operations that can pose challenges to accurate hour rate calculations. A machine that’s constantly breaking down can lead to unexpected costs and operational stoppers. These downtimes not only prevent utilization of resources but might also create delays that affect overall project timelines.
It's essential to incorporate maintenance schedules and associated costs into the overall calculations. Having a preventive maintenance program can reduce the likelihood of unexpected breakdowns. Additionally, using software tools to track machine utilization and maintenance history provides valuable data that can be reflected in the hourly rate calculations.
"Every hour wasted in downtime can mean lost profits. Keeping tabs on maintenance isn't just smart; it's essential."
By recognizing these challenges in hour rate calculations, agricultural professionals can devise strategies that not only address the immediate concerns but also lead to long-term enhancements in efficiency and productivity. A thorough understanding of these challenges empowers decision-makers to navigate the complexities of CNC operations with foresight.
Future Trends in CNC Operations
The world of CNC machining is continuously evolving, shaped by technological advancements and changing market demands. It's essential to keep an eye on the future trends in CNC operations as they hold significant implications for agricultural practices. This discussion is critical because understanding these trends not only prepares farmers and manufacturers for what's on the horizon but also helps them adapt to and capitalize on innovations that can streamline processes, reduce costs, and enhance productivity.
CNC machines are no longer just tools of precision; they have become smarter and are increasingly integrating with various technologies that revolutionize how we approach manufacturing.
Emerging Technologies in CNC Machining
The emergence of new technologies in CNC machining is a game-changer. For instance, the application of Artificial Intelligence (AI) in CNC programming allows for real-time adjustments based on feedback. Machines equipped with AI can analyze data during operation, optimizing at the moment rather than relying on preset parameters. Some CNC units use advanced sensors that gather performance metrics, enhancing predictive maintenance and thus minimizing downtime.
Another promising trend is 3D printing capabilities integrated into CNC machines. This confluence offers the practicality of producing complex parts directly from digital files, reducing waste and material costs. The combination of subtraction CNC techniques with the addition processes of 3D printing leads to innovations in product design, which can be an exciting prospect for agricultural machinery and part production.
Cloud computing is another significant addition. It enables CNC machines to connect to remote servers for data analysis and program management. By utilizing cloud technology, farmers can access performance data anywhere, making operational adjustments on-the-go. This connectivity fosters a collaborative environment, allowing for shared advancements across organizations in the agricultural sector.
Integration with Precision Agriculture
The integration of CNC processes with precision agriculture is becoming increasingly relevant. Precision agriculture relies on data-driven decisions to maximize yield and minimize waste. By utilizing CNC machinery in conjunction with technology such as GPS and Geographic Information Systems (GIS), farmers can achieve higher levels of precision in planting, fertilizing, and harvesting.
For instance, CNC technology can aid in producing customized agricultural equipment that meets specific crop needs. This tailored approach not only enhances efficiency but also contributes to more sustainable practices. For example, farmers can utilize CNC machines to create unique planting equipment suited for varying soil types and conditions, leading to better resource management.
Furthermore, the future will likely see more collaborations between CNC manufacturers and agricultural tech companies, leading to the development of innovative solutions. This partnership can drive the creation of machines that not only produce components at a lower cost but also align with environmentally friendly practices.
"The integration of CNC technology with precision agriculture promises a future where productivity meets sustainability."
In summary, the future trends in CNC operations cannot be ignored. As technology leaps forward, those involved in agriculture must adapt and embrace these changes, leveraging the benefits for improved efficiency and cost-effectiveness. Understanding and implementing these trends can ultimately lead to a competitive edge in the market.
Finale and Best Practices
Wrapping up this intricate look at CNC machine hour rate calculations, it’s evident that knowing how to accurately gauge costs is crucial in the world of agriculture. An effective determination of these rates supports farmers in making financially sound decisions. Not only does this understanding enhance overall productivity, but it also ensures resource allocation is optimized.
By leveraging the right methodologies and keeping track of the variables that influence hour rates, agricultural professionals can navigate their operations with a sharper focus.
"A stitch in time saves nine." This proverb holds true in the machinery sector—addressing issues related to costs promptly can prevent larger problems down the road.
A careful approach to these calculations allows for:
- Better Financial Planning: Knowing the hourly rate aids in setting clear budgets for projects.
- Increased Profit Margins: By managing costs effectively, farmers can focus on profit rather than losses.
- Strategic Operational Decisions: Farmers can choose machinery based on cost-efficiency, rather than just capability.
This section is the bridge between theoretical understanding and practical application. Farming today demands not just the knowledge of how to use CNC machines but fully understanding how these machines impact the bottom line.
Key Takeaways
- Cost Transparency: The explicit calculation of hourly rates illuminates all hidden costs in CNC operations, from maintenance to labor.
- Improved Budgeting Skills: By understanding these calculations, farmers can forecast expenses more accurately.
- Holistic Lens on Operations: A grasp of the financial implications encourages a comprehensive view of farming practices, influencing both machinery selection and long-term strategy.
These insights empower farmers to make informed decisions, ultimately leading to sustainable practices that will keep operations thriving amidst fluctuating market conditions.
Recommendations for Optimizing Costs
In agriculture, every penny counts. Here are practical ways to optimize costs related to CNC machine operations:
- Regular Maintenance: Routine checks can go a long way in preventing unexpected downtimes, directly affecting hourly rate calculations.
- Staff Training: Ensure that all personnel are well-trained to maximize the efficiency of the machinery. An experienced operator can often do more in less time, lowering effective hourly rates.
- Accurate Cost Tracking: Utilize software or DIY spreadsheets to meticulously track all expenses related to CNC operations. This not only aids in precise calculations that contribute to profitability but can also highlight areas needing improvement.
- Invest in Energy Efficiency: Sometimes, investing more upfront in energy-efficient machinery can lead to significant savings in operational costs.
Ultimately, staying proactive about cost management will lead to stronger financial health for farming operations. By understanding the nuances of CNC machine hour rate calculations, farmers can glean insights that pave the way for enhanced productivity and sustainability.