Essential AC Calculations for Optimal Grow Room Temperature
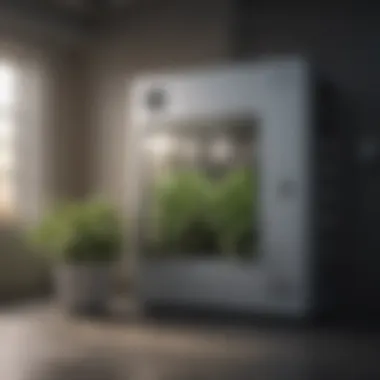
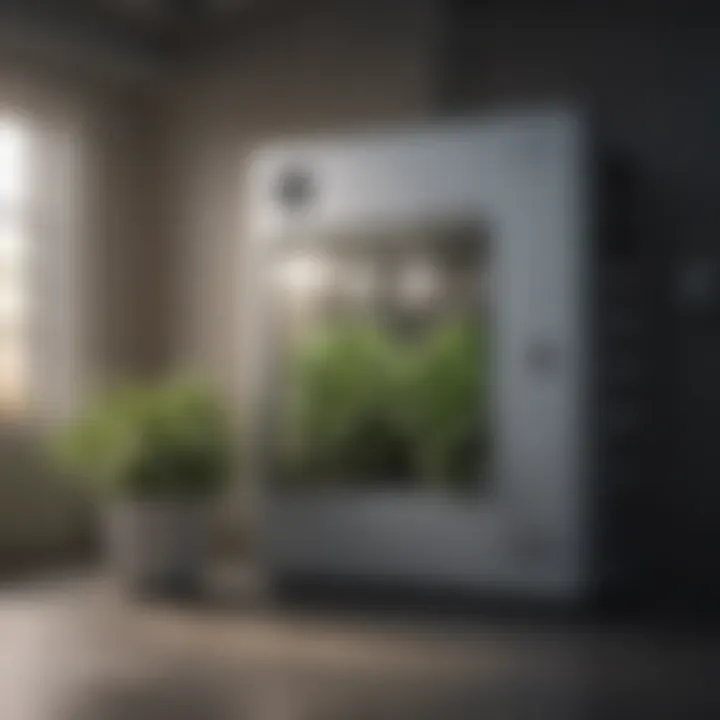
Intro
Effective temperature control is essential for running successful grow rooms. Advanced air conditioning calculations can significantly impact the growth and health of plants. With climate variations and the need for optimal conditions, understanding the principles behind air conditioning for grow rooms can empower agricultural stakeholders.
Topic Overview
Definition of Key Terms
In the realm of grow room management, a few terms stand out. Air Conditioning (AC) refers to systems designed to control the temperature and humidity within a space. Ventilation is crucial, as it ensures airflow, replacing stale air with fresh oxygen. Cooling Load indicates the total heat energy that must be removed to maintain desired temperatures.
Relevance in Agriculture, Horticulture, and Agronomy
Temperature regulation plays a pivotal role in plant growth. In agriculture, failures in temperature management may lead to reduced crop yields. Horticulturists rely on precise ambient conditions to nurture delicate plants. Agronomy, concerned with soil management and crop production, also underscores the necessity of accurate AC calculations.
Current Trends and Innovations
Recent Advancements in the Field
Innovations in climate control technology enhance efficiency and sustainability. Smart sensors now provide real-time data on temperature and humidity, optimizing AC operations. These systems can automatically adjust based on measurements, reducing energy consumption.
Emerging Technologies and Practices
Technological advancements include geothermal cooling and evaporative cooling systems. Geothermal systems utilize the earth's stable temperatures to reduce cooling loads. Meanwhile, evaporative cooling systems leverage water evaporation to lower air temperature, thus enhancing the cooling effect.
Practical Applications
Step-by-Step Guides or How-Tos
Calculating AC requirements may appear daunting, but following structured steps simplifies the process:
- Assess the grow room size: Measure the space to determine its volume.
- Identify heat sources: Calculate any heat generated by grow lights, equipment, and plants.
- Determine cooling load: Use a formula to calculate the required cooling capacity based on the heat sources identified.
- Select appropriate AC units: Match the cooling load with an AC unit that meets the requirements.
Tips and Best Practices for Implementation
Implementing effective AC systems involves careful planning:
- Regular maintenance of equipment extends its lifespan and efficiency.
- Monitor environmental factors to adapt settings as needed.
- Consider zoning within the grow room to cater to different climate needs.
Proper temperature management is essential for maximizing plant productivity, making accurate AC calculations indispensable.
With these tools and insights, professionals in agriculture can enhance grow room productivity by optimizing temperature control through precise air conditioning calculations.
Prelims to Grow Room Climate Control
Effective climate control is vital in grow rooms, where the conditions directly influence plant health and yield. This article focuses on how optimizing temperature through precise AC calculations is essential for growers. Understanding the main factors affecting temperature and air quality can significantly enhance the growth process.
Importance of Temperature Management
Temperature management is not merely a matter of comfort. It plays a crucial role in photosynthesis, nutrient uptake, and overall plant metabolism. Plants thrive within specific temperature ranges. Deviation from these ranges can hinder growth and lead to diseases. Particularly in controlled environments, temperature regulation helps avoid stress on plants, resulting in higher-quality yield.
Maintaining optimal temperature is essential when different growth stages require different conditions. For instance, seedlings generally prefer warmer climates compared to mature plants. Moreover, sudden temperature fluctuations can disrupt physiological processes, ultimately impacting productivity. Therefore, precise management and understanding of temperature needs are paramount for farmers and cultivators.
Role of Air Conditioning in Grow Rooms
Air conditioning systems are fundamental in establishing a stable environment in grow rooms. They serve multiple purposes: regulating temperature, controlling humidity, and ensuring proper air circulation. The effectiveness of an air conditioning unit can significantly influence the success of the entire growing operation. By dissipating heat generated from grow lights and equipment, AC units maintain a consistent temperature.
When selecting an air conditioning system, growers must take into consideration factors such as room size, insulation, and the type of plants being cultivated. Different systems, such as split systems or portable AC units, may better fit specific needs.
The integration of air conditioning in grow rooms is a strategic aspect that not only aids in maintaining conditions but also promotes energy efficiency. Modern units can be equipped with smart technologies, providing real-time data monitoring and energy management, which lead to cost savings over time.
"Effective temperature management in a grow room is directly linked to the success of crop production. Air conditioning units provide essential tools to achieve this."
In summary, the growing environment must be effectively controlled to optimize plant growth. Understanding the importance of temperature management and the role of air conditioning sets the foundation for effective climate control strategies.
Understanding Air Conditioning Basics
Understanding how air conditioning systems function is crucial for effectively managing the climate within grow rooms. The right Air Conditioning (AC) system can aid in maintaining stable temperatures essential for plant health. Good knowledge of AC basics enables growers to make informed decisions tailored to their specific needs. Hence, this section serves as a foundational pillar in achieving optimized conditions for plant growth.
How AC Units Operate
Air conditioning units utilize the principles of thermodynamics to control temperature and maintain desired humidity levels. The core components include a compressor, condenser, expansion valve, and evaporator. The compressor circulates refrigerant through these components, absorbing heat from the air inside the grow room and expelling it outside. During this process, the refrigerant changes from a liquid to a gas and back again, allowing it to absorb and release heat effectively.
In essence, the compressor compresses the refrigerant gas, raising its temperature and pressure. This gas moves to the condenser, where it releases heat to the outside environment and condenses back into a liquid. The liquid refrigerant then passes through the expansion valve, lowering its pressure before entering the evaporator. Within the evaporator, the refrigerant absorbs heat from the indoor air, cooling it before it flows back to the compressor. This cycle continues, thus maintaining a stable temperature within the grow room.
In terms of energy efficiency, modern AC units feature advanced technologies that can significantly reduce energy consumption while still delivering effective cooling.
Types of AC Systems for Grow Rooms
Selecting the appropriate type of AC system is vital for effective climate control. The following systems are commonly used in grow rooms:
- Central Air Conditioning Systems: These units cool air in a centralized location and distribute it through ductwork. They are suitable for larger spaces, providing uniform temperature control.
- Split Systems: Split systems consist of an indoor unit and an outdoor unit. The design allows for quiet operation and efficient cooling, making them popular for smaller grow rooms.
- Portable Air Conditioners: These AC units can be relocated easily and are ideal for those who need temporary cooling solutions. They usually require a window for venting hot air.
- Window Units: These are installed directly into a window frame and offer a simple and cost-effective cooling option for smaller grow rooms.
Each system comes with advantages and disadvantages. For instance, central systems offer extensive cooling capacity but require significant installation efforts. On the other hand, portable units require less setup but may not cool larger spaces efficiently.
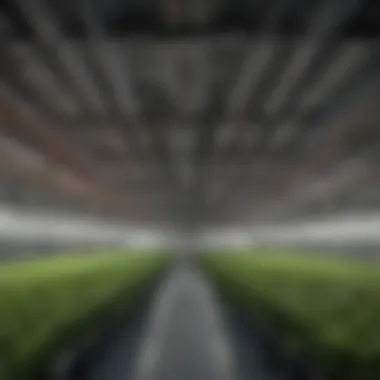
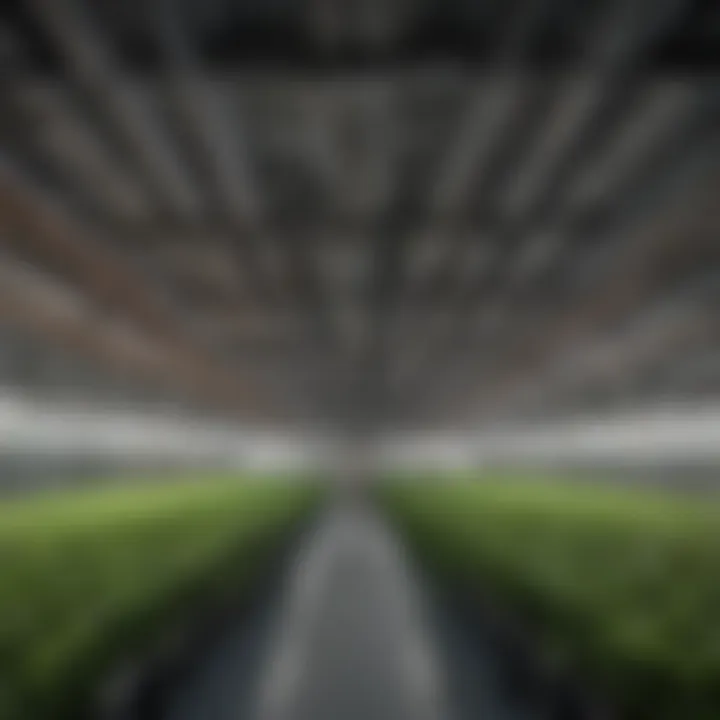
Understanding these types will help growers choose a system that adequately addresses both their space and specific climate control demands.
Fundamentals of Climate Control Calculations
Understanding the fundamentals of climate control calculations is essential for anyone involved in optimizing grow room environments. Proper calculations ensure that plants receive the ideal conditions for growth. Ignoring these calculations can lead to subpar plant health and lower yields.
Effective climate control is not just about controlling temperature; it also encompasses humidity and air circulation. Combining these elements carefully results in a richer understanding of how to manage a grow room sustainably and more effectively.
Key Factors Affecting Temperature
Temperature regulation in grow rooms is influenced by several critical factors that must be accounted for. Start with the most significant contributors:
Heat Load from Grow Lights
Heat from grow lights is a primary source of temperature increase in any grow room. Grow lights emit significant energy, generating heat as they operate. The characteristic of this heat load is substantial enough to raise internal temperatures considerably. It is a beneficial consideration because understanding how much heat is generated by these lights allows for better AC unit selection to mitigate their effects.
Unique Feature: Different grow lights produce varying amounts of heat. For example, high-intensity discharge (HID) lights generally emit more heat compared to LED lights.
Advantages: Using LED lights can reduce the overall heat load, which in turn stabilizes temperature levels within the grow room more effectively. However, this option often requires higher initial setup costs.
Heat from Equipment
Equipment such as fans, pumps, and dehumidifiers also contribute to the heat load within a grow room. This aspect cannot be overlooked. The key characteristic here is visibility; equipment often operates continuously, generating heat consistently throughout the day. This makes it a popular choice for any grow room climate calculation.
Unique Feature: Each piece of equipment has a heat output rating, which needs integration into calculations to understand overall heat contributions.
Advantages: Recognizing equipment heat loads can help make informed decisions about necessary cooling equipment, potentially saving energy costs. However, it can also complicate calculations if not managed properly.
Human Activity
Human activity in the grow room also introduces another layer of complexity. The presence of individuals contributes additional heat, which may seem minor but can accumulate. The key characteristic here is the unpredictable nature of human behavior; activities such as watering, harvesting, or simply working can impact temperature. Sometimes it becomes a less considered element in planning.
Unique Feature: Implementation of attendance scheduling can better manage temperature variations caused by human activity.
Advantages: Actively monitoring and scheduling work can lead to efficiency in temperature control, minimizing unnecessary fluctuations. However, constant monitoring may not always be feasible depending on the operations.
Calculating Heat Loads
Once the key factors are acknowledged, the next step is calculating the total heat loads. This process involves precise measurements and formulas to make informed decisions about climate control.
Formula for Heat Load
The formula for calculating heat load integrates various factors including those discussed previously. It typically starts with the mathematical representation:
- Q = (U x A x ΔT) + (Qlight) + (Qequipment) + (Qhuman)
Where:
- Q = total heat load in BTUs/hr
- U = heat transfer coefficient for walls/ceiling
- A = surface area of walls/ceiling
- ΔT = difference between indoor and outdoor temperature
- Qlight, Qequipment, and Qhuman represent heat loads from their respective sources.
Key Characteristic: This formula provides a comprehensive picture of heat contributions, ensuring nothing is left out.
Advantages: By using this complete equation, growers can make educated decisions about AC unit sizing, potentially improving overall energy efficiency and comfort in the grow room. However, the calculations are intricate and may require professional insight or software for accuracy.
Unit Conversion
Unit conversion is vital in ensuring all measurements are compatible. Commonly, heat loads are measured in BTUs, while other factors can be in different units, such as watts or degrees Celsius. This aspect of calculations ensures clarity in understanding how much cooling is necessary.
Key Characteristic: Familiarity with conversion factors helps in converting heat outputs effectively.
Advantages: Proper unit conversion prevents miscalculations that could lead to over- or under-sized cooling systems. However, it demands a clear understanding of the relevant measurements, which can be a barrier for some.
Managing optimal grow room conditions requires thorough understanding of these fundamentals. Knowledge of heat loads and accurate calculations set the groundwork for successful climate control strategies.
Components of Grow Room AC Calculators
Understanding the components of grow room AC calculators is crucial for optimizing temperature control. These calculators serve as tools that consolidate various input variables and output measures to facilitate informed decision-making. By grasping the underlying features and advantages of each component, users can better manage their grow room conditions, enhancing the health and yield of their plants.
Input Variables for Calculation
Room Size
The room size significantly influences the effectiveness of temperature management in a grow room. It determines the amount of air space that needs to be cooled and plays a critical role in calculating the needed BTUs (British Thermal Units). A critical characteristic of room size is its relationship with heat accumulation. Larger rooms may require more cool air to maintain optimum conditions. Therefore, correctly assessing room size is beneficial when determining air conditioning capacity.
The unique feature of room size is its variability in different setups. Commercial growers may have sprawling facilities while home growers may work with smaller spaces. Each scenario presents its own advantages and disadvantages. A larger room can offer more flexibility for plant arrangement but also faces challenges like uneven cooling. On the other hand, a smaller room might be easier to control but limits the overall plant capacity.
Insulation Quality
Insulation quality is another pivotal element that affects temperature retention within a grow room. The main objective of good insulation is to minimize heat exchange with the external environment. High-quality insulation decreases the load on the AC system, making it efficient in maintaining stable temperatures. This quality helps create a microclimate suitable for optimal plant growth.
What makes insulation particularly beneficial in this context is its impact on energy consumption. Better insulation lowers energy costs, making it an attractive option for growers keen on sustainability. However, subpar insulation can lead to fluctuations in temperature, which could stress plants. Therefore, investing in proper insulation is an important consideration for growers aiming for optimal conditions.
External Temperature
External temperature is an essential factor influencing the internal climate of a grow room. As the surrounding temperature fluctuates, it can significantly impact the performance of air conditioning units. A key characteristic here is the need to adjust the AC settings according to seasonal changes and time of day. Varying external temperatures must be accounted for to ensure the indoor environment remains consistent.
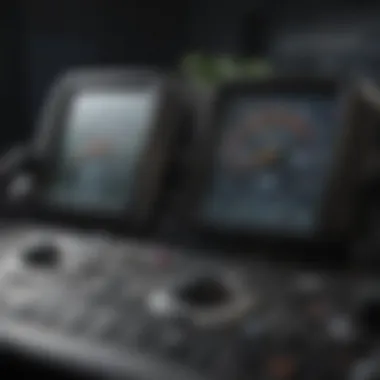
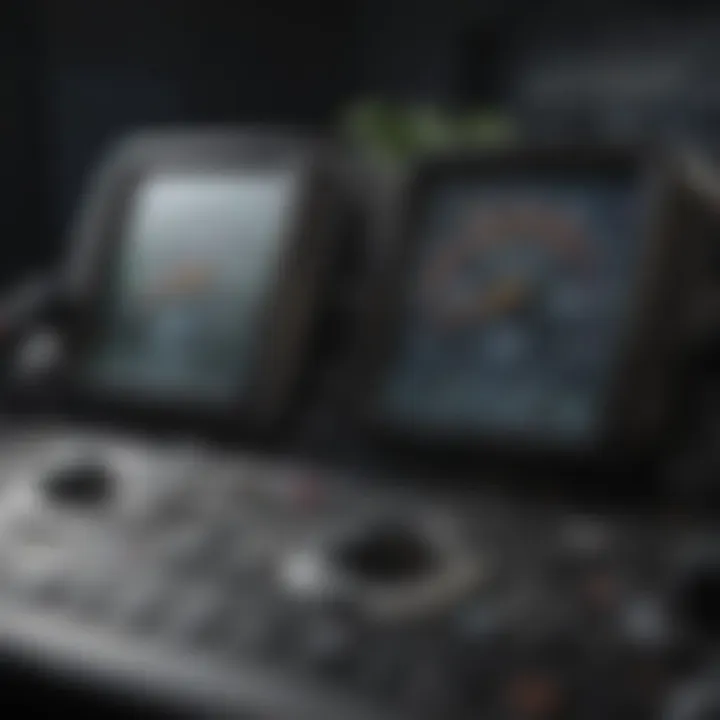
The unique aspect of external temperature affects not only the air conditioning load but also the overall energy efficiency of the system. While higher temperatures outside will require more cooling power from the AC, lower temperatures can ease the burden. Recognizing these variations is critical for real-time adjustments. Thus, understanding how external temperature interacts with internal conditions is vital for maintaining optimal growth conditions.
Output Measures and Interpretations
BTU Requirements
BTU requirements are a pivotal measure that emerges from the previous calculations. They indicate the cooling power needed to maintain a designated temperature within the grow room. Understanding BTU requirements helps growers select appropriate AC units specific to their environment. This characteristic makes BTUs a critical consideration for optimizing energy use and ensuring plant health.
The unique feature of BTU requirements is their ability to be closely tailored to individual setups. This adaptability means growers can calculate precise cooling needs based on room size, insulation quality, and external factors. However, miscalculating BTUs can lead to either undercooling or excessive energy use, which might lead to higher costs and stress on plants.
Recommendations for AC Units
Recommendations for AC units should stem from comprehensive analyses of input variables and BTU requirements. Choosing the right air conditioning unit becomes more accessible when the specific conditions of the grow room are well understood. A significant characteristic of these recommendations is their reliance on factors such as unit efficiency, size, and price.
What makes recommendations particularly relevant is their potential to improve both plant health and operational efficiency. A high-efficiency unit may have a higher upfront cost but can save money long-term through reduced energy bills. Conversely, selecting an oversized or undersized unit can lead to performance issues. Therefore, taking time to consider tailored recommendations is highly beneficial for the grower.
Advanced Calculation Techniques
Using advanced calculation techniques is critical for achieving effective temperature control in grow rooms. These methodologies enable growers to fine-tune the climate conditions, ensuring optimal plant growth. The fundamental understanding of advanced calculations can significantly affect the health of crops and overall yield. A thorough analysis of temperature and humidity levels, alongside energy efficiency measures, provides a comprehensive perspective on a grow room's environmental quality.
Incorporating Humidity Control
Humidity plays a vital role in plant growth. By integrating humidity control into AC calculations, growers can create a balanced environment conducive to thriving plants. Monitoring humidity levels allows for adjustments to be made in real-time. Proper humidity ensures that plants do not experience stress and can photosynthesize effectively.
An effective humidity level for most indoor gardens ranges from 40% to 60%. Use of hygrometers helps maintain these suggested percentages. When humidity is too high, it can lead to mold issues, while too low humidity can hinder growth. In this context, the AC unit must be equipped to handle both temperature and humidity levels.
Energy Efficiency Considerations
Energy efficiency should be a prominent factor in selecting AC systems for grow rooms. Optimizing for energy efficiency not only reduces costs but also supports environmental sustainability. There are two main aspects to consider when evaluating energy-efficient systems: SEER ratings and cost analysis.
SEER Ratings
The Seasonal Energy Efficiency Ratio (SEER) ratings serve as an important benchmark for comparing AC units. The higher the SEER rating, the more efficient the unit is at converting electricity into cooling. A higher SEER rating can lead to substantial savings on energy bills. For instance, units with a SEER rating of 16 or higher are considered efficient for grow rooms. This characteristic makes high SEER units a popular choice for energy-conscious growers.
However, while higher SEER units typically have a greater upfront cost, they will pay off in energy savings over time. The unique feature of these ratings lies in their ability to offer a quantifiable metric for efficiency. However, it is essential to consider the initial investment in relation to long-term savings when making a decision.
Cost Analysis
Cost analysis is a critical step when evaluating AC units. This involves understanding the total cost of ownership, which includes installation costs, maintenance costs, and operational expenses. By analyzing these factors, growers can make more informed choices. An initial low-cost unit may lead to higher operational costs down the line if it is not energy-efficient.
In addition, factors such as the cost of electricity and the projected growth timeline should factor into any cost analysis. For instance, if a grower plans to operate a facility long-term, investing in a higher-quality, energy-efficient unit may be advantageous. The unique feature of a detailed cost analysis allows growers to assess the total financial impact over time, rather than just the initial price. This consideration is especially vital as the demand for sustainable practices in agriculture continues to grow.
Selecting the Right AC Unit
Selecting the appropriate air conditioning unit is crucial in managing the climate of a grow room. The right AC can significantly influence plant growth, impact energy efficiency, and reduce operational costs. Many factors come into play when determining the most suitable unit for a specific grow environment. By paying attention to these elements, growers can create a stable atmosphere that fosters optimal conditions for their plants.
Brand Comparisons
When it comes to choosing an AC unit, various brands offer distinct features and performance levels. Here are a few notable brands:
- LG: Known for advanced technology and energy-efficient models, LG units often come with smart features like Wi-Fi connectivity.
- Mitsubishi Electric: This brand specializes in ductless systems which are quiet and efficient, making them suitable for small spaces.
- Daikin: Renowned for its durability and performance, Daikin units offer a wide range of sizes and capacities.
- Friedrich: Provides robust window and portable units that are popular among indoor growers due to their performance in high humidity.
Evaluating these options involves looking into aspects such as reliability, customer support, warranty, and reviews from other growers. The performance in terms of SEER ratings and cooling capacity should also weigh heavily in the decision.
Size and Capacity Considerations
Determining the correct size and capacity for an AC unit is imperative for achieving effective temperature control. An undersized AC unit will struggle to cool adequately, leading to fluctuating temperatures, while an oversized unit may cycle frequently, which can lead to inefficient energy consumption and humidity control issues.
Key elements to consider include:
- Room Size: Measure the dimensions of the grow room. Accurate room calculations can determine the necessary BTU (British Thermal Unit) output required to maintain optimal temperatures.
- Heat Load: Calculate heat load from grow lights, reflectors, and any equipment operating in the room. Each component emits heat, contributing to overall temperature conditions in the grow space.
- Plant Types: Different plants have varying temperature needs. Understanding these requirements can help define the cooling capacity needed.
A good rule of thumb is to use a cooling calculator or seek professional advice to find the right size for your specific situation. In short, selecting the appropriate AC unit by considering brand reliability and correct sizing will pave the way for effective and efficient temperature management in grow rooms.
Installation Best Practices
The installation of air conditioning units in grow rooms is a critical factor in ensuring optimal temperature control. Proper installation is vital not only for the efficiency of the system but also for the health and productivity of the plants. When done correctly, it can lead to significant improvements in energy consumption, plant yield, and overall operational effectiveness. This section highlights key elements and considerations regarding best practices for AC installation.
Positioning of AC Units
The placement of AC units is a foundational aspect of effective temperature control. Units should be positioned to maximize airflow while avoiding direct exposure to the plants. Avoiding direct airflow can prevent plant stress and potential damage. An optimal location usually involves positioning the unit near the room's center or in a corner where airflow can reach all areas of the room.
Additionally, installing the AC unit at a height that allows warm air to move towards it can further enhance efficiency. Sometimes, special mounting brackets might be necessary to achieve the correct height and angle. Regular inspection of the placement is necessary, as obstructions can develop, impacting the system's performance.
Ducting and Ventilation Setup
Ducting plays an essential role in ensuring that cooled air is effectively distributed throughout the grow room. Good ducting design comes with several elements to consider. First, the diameter and length of ducts must be selected carefully to minimize resistance and maximize airflow. Shorter ducts are generally preferred, as they reduce the likelihood of energy wastage.
Secondary to the ducting, adequate ventilation is also critical. It is important to integrate intakes and exhausts into the design. Ventilation greatly influences the cooling system's efficiency and helps maintain necessary humidity levels. Consider employing thermostatic controls that can adjust fan speeds based on temperature and humidity readings.
Proper ducting and ventilation facilitate balanced temperature distribution, critical for plant health in grow rooms.
Maintaining Optimal Conditions
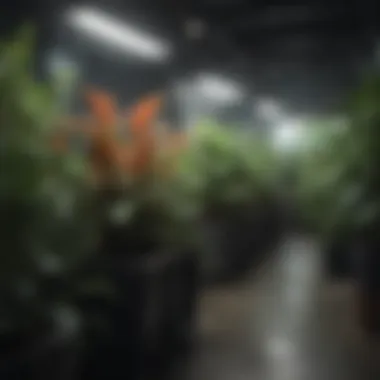
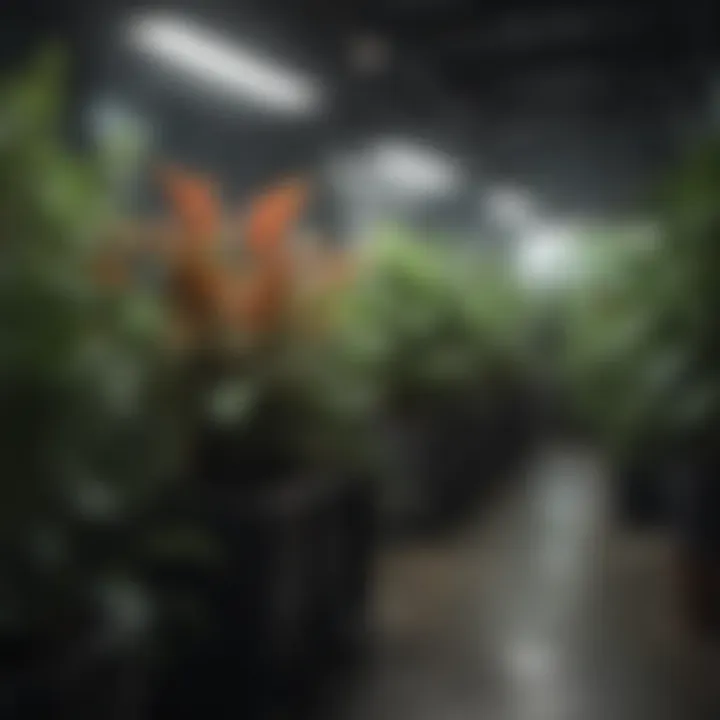
Maintaining optimal conditions in a grow room is critical for ensuring plant health and maximizing yields. If temperature and humidity levels are not carefully controlled, plants can suffer from stress, which may lead to poor growth and reduced harvests. A well-maintained environment not only promotes robust plant development but also enhances pest and disease resistance.
Several elements contribute to maintaining these ideal conditions. First and foremost, regular maintenance routines keep HVAC systems, dehumidifiers, and other climate-control technologies running efficiently. Second, investing in the right monitoring tools enables growers to respond quickly to any variations in the environment, which is crucial in agriculture where timing can greatly affect outcomes.
Additionally, it is important to be aware of seasonal changes and how they might impact internal conditions. For example, during hotter months, heat load increases significantly, which puts additional strain on cooling systems. Thus, thorough understanding of climate dynamics within grow rooms is a key factor in mitigating these fluctuations.
"Accurate monitoring and maintenance can enhance productivity and lead to better overall results in agricultural production."
In summary, sustaining optimal conditions is not just a one-time task but an ongoing responsibility. Implementing structured routines and keeping abreast of technological innovations in monitoring and maintaining climate control will ensure a productive growing environment.
Regular Maintenance Routines
Implementing regular maintenance routines is fundamental to achieving reliable climate control in a grow room. The HVAC system, which ensures temperature regulation, needs frequent checks for efficiency. This involves cleaning filters, inspecting ducts, and ensuring that no blockages exist which can impede airflow. A well-maintained AC unit operates more efficiently, reducing energy costs and prolonging the equipment's life.
Routine calibration of sensors and controls is also crucial. Temperature and humidity sensors are the eyes of your growing operation. If they are not properly calibrated, they may provide faulty readings, leading to inappropriate adjustments to the environment. Therefore, maintenance checks should include not only cleaning but recalibrating these instruments occasionally.
Monitoring Tools and Technologies
Monitoring tools and technologies have become indispensable in modern agriculture. They allow growers to constantly assess the environmental conditions within the grow room and make real-time adjustments as necessary.
In addition to traditional thermometers and hygrometers, advanced options like smart sensors can provide deeper insights. These devices can connect to your smartphone or computer, giving you remote access to real-time data. This means you can be alerted to problems even when you are away from your grow space.
Other tools include climate control software that integrates with HVAC systems, allowing for automated adjustments based on predefined parameters. Such systems help in achieving consistency, which is vital for plant health.
Using a combination of manual checks and automated technologies creates a comprehensive monitoring strategy. This dual approach ensures that while you have immediate knowledge of any changes, you are also taking advantage of technological advancements to streamline the monitoring process.
Troubleshooting Common Issues
Addressing the challenges associated with temperature management in grow rooms is crucial for optimal plant health and productivity. Understanding common issues such as temperature fluctuations and equipment failures can help growers implement effective solutions. This section focuses on the significance of troubleshooting these common problems, detailing key elements, benefits, and considerations that arise in the process.
The importance of effective troubleshooting cannot be overstated. It contributes not only to maintaining ideal growing conditions but also to reducing energy costs associated with inefficient systems. When growers can spot problems early, they can mitigate risks that may lead to crop loss or reduced yield.
Identifying Temperature Fluctuations
Temperature fluctuations can occur due to various factors such as changes in external weather conditions, equipment malfunction, or improper insulation. Observing these changes is essential in maintaining the stability of the grow environment.
To effectively identify fluctuations:
- Use Thermometers: Placing multiple thermometers in various parts of the grow room can help gather accurate data on temperature distribution.
- Data Logging: Employing temperature sensors that log data over time provides useful insights into patterns and extremes.
- Monitor External Conditions: Keeping track of weather updates aids in correlating indoor temperature shifts with outside influences.
"Continuous temperature monitoring is vital. It allows growers to react promptly to undesired changes."
The key is not only to notice when the temperature changes but also to analyze why it happened. Creating a schedule for regular checks can prevent prolonged exposure to unsuitable temperatures.
Resolving Equipment Failures
When equipment failures occur, they can disrupt the entire climate control system of a grow room. Common issues include air conditioning breakdowns, failure of exhaust fans, or issues with humidity control systems. Recognizing these failures promptly is essential to minimize impact on plant growth.
To manage these failures effectively:
- Routine Inspections: Regular checks on all equipment help spot potential problems before they escalate.
- Maintenance Schedules: Establish a maintenance regimen for all critical components. This can include filter changes and system cleaning.
- Backup Systems: Having a backup AC unit or fans can provide a quick solution in case of equipment failure.
Growers should also be familiar with common indicators of equipment failure such as unusual noises, higher energy bills, or inconsistent performance. By addressing these signs swiftly, one can either repair the malfunctioning equipment or seek replacements as necessary.
Understanding how to troubleshoot these common issues ultimately leads to a more productive and efficient grow room environment. By being proactive in maintenance and monitoring, growers can foster a thriving ecosystem for their plants, ensuring better yields throughout the growth cycle.
The Future of Temperature Management in Agriculture
The future of temperature management in agriculture stands as a focal point in optimizing grow room environments. This topic is essential not only for enhancing crop yields but also for adapting to changing climatic conditions. As agriculture faces increasing challenges from climate change, adopting advanced temperature control measures becomes paramount.
Key benefits of focusing on temperature management include improved plant health, increased productivity, and a more sustainable approach to farming. By integrating modern technological solutions, farmers can precisely monitor and control their growing conditions. This results in a more predictable and efficient growing cycle.
Emerging Technologies
Emerging technologies play a significant role in transforming temperature management within agricultural settings. Various innovative tools are becoming indispensable for growers worldwide.
- Smart Sensors: These devices can continuously monitor temperature and humidity levels inside grow rooms. They provide real-time data that helps in making informed decisions quickly, preventing any potential negative impacts on crop health.
- Automated Climate Control Systems: Systems like those developed by companies such as AC Infinity or EcoPlus can adjust environmental conditions automatically. By linking these units to external weather data, they optimize the internal climate based on real-time requirements.
- Data Analytics: Big data analytics helps in understanding patterns in temperature fluctuations over time. This can lead to predictive modeling, which aids in anticipating heat loads and making preemptive adjustments to ventilation and cooling systems.
- Artificial Intelligence: AI can analyze data from numerous farms to recommend temperature settings and adjustments tailored to specific crops and regions.
These technologies collectively represent a shift towards precision agriculture. They allow for better resource management, leading to greater yields and reducing waste.
Sustainable Cooling Solutions
Sustainable cooling solutions are vital components in the future of temperature management. As the environmental impact of traditional cooling systems comes under scrutiny, alternative methods of cooling are increasingly sought after.
- Geothermal Energy: By leveraging the natural temperature of the ground, geothermal systems can provide efficient, sustainable cooling with minimal energy consumption.
- Evaporative Cooling: This method utilizes water evaporation to lower temperatures. It consumes less energy compared to conventional air conditioning, making it a more eco-friendly option.
- Solar-Powered Systems: Integrating solar panels with cooling systems can significantly reduce reliance on electricity from the grid. By using renewable energy, operations become more sustainable.
- Insulation Improvements: Strengthening the insulation in grow rooms helps to maintain stable temperatures, reducing the overall reliance on cooling systems.
In summary, the future of temperature management in agriculture is poised for a significant evolution through technology and sustainable practices. Emphasizing these aspects not only prepares growers for environmental fluctuations but also enables them to achieve higher productivity while maintaining a commitment to sustainability.
Closure
In this article, we have explored the complexity and importance of optimizing temperature control in grow rooms through precise AC calculations. Effective temperature management is vital to maximizing plant growth and ensuring the health of agricultural yields. Proper climate control can lead to increased efficiency, higher quality produce, and reduced resource wastage.
Summary of Key Points
- Understanding Temperature Control: Temperature influences plant physiology. Managing it effectively ensures optimal growth rates and minimizes stress on plants.
- Calculations Matter: Accurate calculations of heat loads are fundamental. Assessing factors such as heat from grow lights, equipment, and even human activity provides insights into the cooling requirements of a grow room.
- Choosing the Right AC Unit: Selecting an efficient and appropriately sized air conditioning unit is crucial. The right system contributes directly to energy savings and maintenance of desired environmental conditions.
- Installation and Regular Maintenance: Proper installation and ongoing maintenance routines ensure the reliability of the cooling system, preventing unexpected failures and enabling optimal performance.
- Troubleshooting Skills: Understanding common AC issues and their resolutions aids in keeping the grow room climate steady. Proactive measures can significantly improve overall productivity.
- Future Considerations: As technology advances, innovations in cooling solutions and climate management strategies will become increasingly relevant for both sustainability and efficiency in agriculture.
Looking Ahead in Grow Room Management
Given the ever-evolving landscape of agricultural practices and technology, the future of grow room management appears promising. Innovations in climate control systems, such as smart thermostats and advanced humidity regulation, are being integrated into grow rooms, offering farmers enhanced capabilities for monitoring and adjusting conditions in real-time.
Furthermore, a growing focus on sustainability suggests an increase in energy-efficient solutions, which not only minimize energy consumption but also support environmental preservation efforts. The incorporation of renewable energy sources for powering AC units may become a common practice, aligning with broader agricultural strategies aimed at reducing carbon footprints.